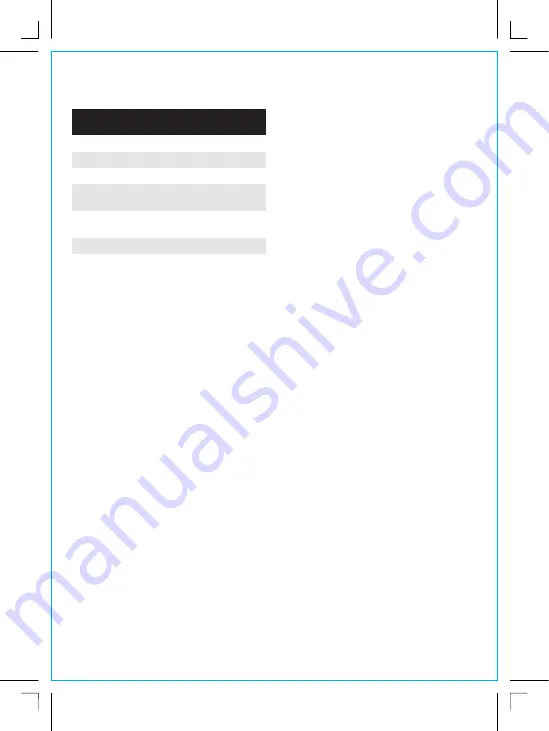
166
3M™ 6000 Series Fullface
Mask with
Nominal Protection Factor
P1 Particulate Filters
5 x TLV
P2 Particulate Filters
15 x TLV
3M™Air Supply Unit
SeeAirline user instruction
P3 Particulate Filters
1000 x TLV
Class 1 Gas & Vapour Filters
2000 x TLV or 1000ppm
(Whichever is lower)
Class 2 Gas & Vapour Filters
2000 x TLV or 5000ppm
(Whichever is lower)
Zealand 0800 364 357.
• Do not use in concentrations above those
specified in
Technical Specification
.
• Do not use for respiratory protection against
atmospheric contaminants/concentrations which
have poor warning properties or are unknown or
immediately dangerous to life and health (IDLH) or
against contaminants/concentrations which
generate high heats of reaction with chemical filters.
• Do not use in atmospheres containing less than
19.5% oxygen. (3M definition. Individual countries
may apply their own limits on oxygen deficiency.
Seek advice if in doubt).
• Do not use these products in oxygen or
oxygen-enriched atmospheres.
• Only use with the Filters/Air Supply Units and
Spares/Accessories listed in the Reference Leaflet
and within the usage conditions given in the
Technical Specification
.
• Only for use by trained competent personnel.
• Leave the contaminated area immediately if:
a) Any part of the system becomes damaged.
b) Airflow to the face piece decreases or stops.
c) Breathing becomes difficult or increased
breathing resistance occurs.
d) Dizziness or other distress occurs.
e) You smell or taste contaminants or irritation
occurs.
• Never modify or alter this product. Replace parts
only with original 3M spare parts.
• In case of intended use in explosive atmospheres,
contact 3M Technical Service.
• Do not use these products with self-contained
breathing apparatus.
• Do not use for escape purposes.
• Do not use with beards or other facial hair that
may inhibit contact between the face and the
product thus preventing a good seal.
• Only use with the spectacle kit available as an
accessory with this product, and ensure spectacle
arms do not interfere with the faceseal.
• National regulations may impose specific
limitations on the use of filters depending on the
filter class and the facepiece used. Use of any 3M™
Face piece / Filter combination should be in
accordance with applicable Health and Safety
standards, AS/NZS 1715, Respiratory Selection
Tables or in accordance with the recommendations
of an Occupational Hygienist.
• Filters need to be regularly changed. The
frequency of change depends on usage time and
the concentration of contaminant.
• For more information call the 3M Tech Assist
Helpline 3M Australia 1800 024 464, 3M New
Zealand 0800 364 357.
•
If using with a 3M™ Air Supply Unit:
• At very high work rates, the pressure in the face
piece may become negative at peak inhalation flow.
Adjust equipment as appropriate or consider an
alternative form of respiratory protective device.
• If using in Supplied Air mode, ensure that:
• The source of the air supply is known.
• The purity of the air supply is known.
• The air supply is of a breathable quality to AS/NZS
1715.
If during use the air supply stops or is reduced,
vacate the contaminated area immediately and
investigate the cause.
• Take care to prevent the breathing tube from
becoming looped around protruding objects
• These products do not supply oxygen.
NOTES REGARDING ALLERGIC
REACTIONS
Materials which may come into contact with the
wearer's skin are not known to cause allergic
reactions to the majority of individuals.
These products do not contain components made
from natural rubber latex.
PREPARATION FOR USE
Inspect the package contents for shipping damage
and ensure all components are present.
Check apparatus is complete, undamaged and
correctly assembled. Any damaged or defective
parts must be replaced with original 3M spare parts
before use.
Inspection
The following inspection procedure is
recommended before use:
1. Check the face piece for cracks, tears and dirt.
Be certain the face piece, especially the face seal
area, is not distorted. The material must be pliable –
not stiff.
2. Examine the inhalation valves for cracks or tears.
Lift valves and inspect valve seat for dirt or cracks.
3. Ensure that the head straps are intact and have
good elasticity.
4. Examine all plastic parts for signs of cracks or
fatigue.
5. Make sure all gaskets are properly seated.
6. Remove the exhalation valve cover and examine
the exhalation valve and valve seat for signs of dirt,
distortion, cracks or tears. Replace the exhalation
valve cover.
7. Inspect lens for any damage that may impair
respirator performance or vision.
ASSEMBLY INSTRUCTIONS
See appropriate User Instructions for assembly
instructions (e.g. 3M™ Filter/3M™ Air Supply Unit).
FITTING INSTRUCTIONS
Select most appropriate size from the 3 sizes of the
face piece available (S / M / L). Fitting Instructions
must be followed each time the product is worn.
DONNING
1. Fully loosen all 4 head straps and put straps over
front of facepiece.
2. If necessary, pull hair back out of facepiece
sealing area.
3. Place chin in respirator chin cup and make sure
that respirator is centred on your face.
4. Pull head harness over your head (Figure 1).
Remove any bumps or kinks in the head harness
and ensure straps are flat to the head.
5. Whilst holding the mask in place with one hand,
tighten each strap evenly a little at a time, starting
the neck straps, followed by the forehead straps.
Repeat until the mask feels secure on the face.
(Figure 2).
DO NOT OVERTIGHTEN.
6. Ensure that there are no creases or gaps around
facepiece perimeter. Figure 3 shows a poorly fitted
mask with creases around the face piece,
WARNING
Such creases may impact fit. Use of a
mirror or the help of a colleague is recommended.
Readjust straps and/or reposition facepiece as
necessary.
Perform a positive and/or negative pressure seal
check.
SEAL CHECK
• Positive Pressure User Seal Check (for all
approved configurations)
(all Filters except 3M™
6035 /6038/ 2000 Series Filters).
Place palm of hand over exhalation valve cover and
exhale gently. Figure 4.
If the facepiece bulges slightly and no air leaks are
detected between the face and the facepiece, a
proper seal has been obtained.
If an air leak is detected, reposition the respirator on
the face and / or re-adjust the tension of the elastic
strap to eliminate the leakage.
Repeat the above fit check.
• Negative Pressure User Seal Check with 6035 /
6038 Filters Also 2000 Series filters.
Press your thumbs into the central indentation of
the filters (2000 Series), or press filter cover and
filter body together (6035/6038), inhale gently and
hold your breath for ten seconds If the face piece
collapses slightly a proper fit has been achieved.
Figure 5. If an air leak is detected, reposition the
respirator on the face and / or re-adjust the tension
of the elastic strap to eliminate the leakage. Repeat
the above fit check.
If you CANNOT achieve a proper fit, DO NOT
enter the contaminated area.
Quantitative Fit Testing
For information regarding fit testing procedures,
please contact 3M.
DOFFING
^
Do not remove the face piece, filters or turn
off the air supply until you have vacated the
contaminated area.
1. Release the tension on the head straps.
2. Carefully lift face piece off the face and remove
the respirator by lifting up and away from the face.
3. If appropriate, switch off the air supply unit or
disconnect the compressed air supply tube from the
regulator, and unbuckle the waistbelt.
NOTE If the respirator has been used in an area
that has caused it to become contaminated with
a substance requiring special decontamination
procedures it should be placed in a suitable
container and sealed until it can be
decontaminated or discarded.
MAINTENANCE
Maintenance, servicing and repair must only be
carried out by properly trained personnel. Since this
respirator is a low maintenance face piece only a
limited number of replacement parts are available
(See reference leaflet). If other parts are damaged
the respirator must be replaced.
^
{Insert warning triangle}
Use of unapproved
parts or unauthorized modification could result
in danger to life or health and can invalidate any
warranty.
General inspection must be carried out
before use or monthly if not in regular use. See
Inspection procedures for specific details. If disposal
of parts is required this should be undertaken in
accordance with local health and safety and
environmental regulations.
SPARE PARTS
Centre Adaptor (6864) Replacement.
To remove Centre Adaptor, remove the nose cup
assembly, by pulling the assembly over the three
notches which anchor it to the base of the centre
adaptor.(Fig 6). Grasp centre adaptor at cover and
twist counter-clockwise 1/4 turn to disengage and
withdraw centre adaptor from lens. Replace centre
adaptor by pushing three lugs in through the lens
gaps, (Fig7 )and turning it 1/4 clockwise. Replace
nose cup assembly.(Fig 8 )
Centre Adaptor Gasket (6896) Replacement.
The closed cell foam rubber centre adaptor gasket
is designed to seal the interface between the centre
adaptor and the lens. Remove nose cup assembly,
and center adaptor from lens centre port as
described above. Remove old gasket from centre
adaptor and replace with new replacement gasket.
Re-install centre adaptor into facepiece lens.
Replace nose cup assembly. (Figs 6-8)
Exhalation Valve (7583) Replacement.
Remove center adapter cover by pulling out from
bottom latch. Grasp valve and pull each valve stem
out from valve seat. Place exhalation valve
replacement over the exhalation port by inserting
stems and pulling through from the opposite side
until they are both snapped in place. Replace valve
cover by aligning top opening in the valve cover
with the top tab on the center adapter base and
snap to the center adapter base. Figure 9.
Inhalation Gaskets (6895) Replacement.
The inhalation gaskets are designed to seal the
interface between the bayonet attachment
inhalation ports on the face piece and filters / air
supply unit. The gaskets should be inspected with
each filter change and replaced whenever damaged
or seal integrity is questionable. Remove gaskets
from inhalation port bayonet fittings. Install new
gaskets onto face piece inhalation port under all
three bayonet lugs. Figure 10.
Inhalation Valves (6893) Replacement.
Inhalation valves are located on posts at the inside
of the face piece inhalation ports and inside the
nose cup inhalation ports. These valves should be
inspected before each respirator use and replaced
whenever valves become damaged or lost. Remove
existing Inhalation valve(s) by lifting from post(s) at
the inside of the face piece and nose cup inhalation
port(s). Install new valve(s) onto post(s). Be certain
valve is fully engaged under all three lugs on post,
lies flat, and spins freely on post.
Head Harness (6897) Replacement.
Unbuckle head harness straps and replace with
new head harness. Figure 11.
Lens Assembly (6898) Replacement.
Remove the two sets of screws using a screwdriver.
Then, pull the frame top and frame bottom away
from the faceseal. The frame top, frame bottom,
faceseal and the lens assembly have vertical line
markings that indicate their positions relative to one
another. Make certain these markings are aligned
for re-assembly. Figure 12.
Neck Strap (7883).
Connect loops at end of neck strap assembly onto
the face seal tabs at the top of the head harness.
ACCESSORIES
Spectacle Kit (6878).
Install rail assembly into Face Piece with the plastic
foot positioned on centre port adapter and the top of
rail is centered between the lugs or projections at
top of face seal. Install frame assembly onto rail
assembly by inserting pins into holes in rubber
slide. Spectacles can now be adjusted for optimal fit
and vision.
Lens Covers (6885).
Remove release liner from adhesive at each side of
replacement Lens Cover. Position lens cover over
the Face Piece Lens and adhere in place. Remove
used lens cover by lifting tab away from face piece.
CLEANING AND DISINFECTION
Cleaning is recommended after each use. If the
respirator is to be used for more than one shift it
should be cleaned at the end of each shift and
stored between shifts in the original packaging or a
sealed container. To clean the respirator, the 3M™
504 Wipe should be used to wipe the face seal of
the product. Remove the filters and disconnect the
air supply unit if appropriate. Clean parts (excluding
filters) by immersing in warm cleaning solution
(water temperature not to exceed 50°C), scrub with
soft brush until clean. Add neutral detergent if
necessary. Disinfect respirator by soaking in a
solution of quaternary ammonia disinfectant or
sodium hypochlorite or other disinfectant. Rinse in
clean, warm water and air dry at room temperature
in a non-contaminated atmosphere.
CAUTION
Do not use cleaners containing lanolin or
other oils on these products. Do not autoclave. Do
not use petrol, chlorinated degreasing fluids (such
as trichloroethylene), organic solvents or abrasive
cleaning agents to clean any part of the equipment.
Do not reassemble parts until facepiece is
completely dry.
STORAGE AND
TRANSPORTATION
These products should be stored in the packaging
provided in dry, clean conditions away from direct
sunlight, sources of high temperature, petrol and
solvent vapours. The original packaging is suitable
for transporting the product. When stored as stated,
the expected shelf life of the product is 5 years from
date of manufacture. Store in accordance with
manufacturer’s instructions, see packaging.
]
End of Shelf Life
\
Temperature Range
,
Maximum Relative Humidity
The date of manufacture can be established by
examining the date clock on the inside of the
facepiece. Figure 13. The inner segment will display
the year, and the arrow will point to the month of
manufacture in the outer segment. The example
shows 01/09/2011 - 30/09/2011.
APPROVALS
These products are type approved and audited
annually by either: BSI Group The Netherlands B.V.
John M. Keynesplein 9, 1066 EP Amsterdam, The
Netherlands, Notified Body No. 2797. and / or BSI
Assurance UK Ltd, Kitemark Court, Davy Avenue,
Knowlhill, Milton Keynes MK5 8PP, UK, Notified
Body No. 0086. These products meet the
requirements of European Regulation (EU)
2016/425 and applicable local legislation. The
applicable European/local legislation and Notified
Body can be determined by reviewing the
Certificate(s) and Declaration(s) of Conformity at
www.3m.com/Respiratory/certs.
3M United Kingdom PLC, 3M Centre, Cain Road,
Bracknell, RG12 8HT, 08706080060.
Dispose in accordance with local regulations
TECHNICAL SPECIFICATION
Respiratory Protection
EN136 (Class 1) - for use
with 3M Filters (bayonet) to EN14387:2004 or
EN143:2000 and AS/NZS 1716:2012 (see
Reference Leaflet). This may not be the level of
respiratory protection that can be realistically
expected in the workplace by wearers.
Required Minimum Protection Factor (RMPF) - the
protection factor required to reduce exposure to an
acceptable level. It is expressed as a ratio of the
measured ambient airborne concentration of a
contamniant to an acceptable exposure level or
stanard.
Many countries apply Assigned Protection Factors
(APFs). For P3 rated filters: Provides P3 protection
only with a full facepiece respirator. Provides P2
protection with half facepiece respirator. Employers
may apply a value lower than the APF if deemed
applicable.
Please refer to AS/NZS1715 for application of these
numbers in the workplace. Please contact 3M for
further information.
Eye Protection
Meets the requirements of EN166
(Increased Robustness, Protection against High
Speed Particles (medium energy) and Lateral
protection. Meets high impact rating and protection
against hot solids to AS/NZS1337.
Flow Characteristics
Manufacturers Minimum Design Flow (MMDF) 150
l/min
Maximum Flow - See appropriate User Instructions.
Maximum Operating Temperature: +49 °C.
CAUTION
Care should be taken when using the
equipment at low temperatures as excessive
moisture may cause the valves to freeze.
Summary of Contents for 6000
Page 3: ...2 4 5 1 2 6 2 3 ...
Page 4: ...3 7 10 11 8 9 12 ...
Page 168: ...167 O 3 6000 3M 3M 3M 3M 3M 136 199 3M 3M 3M IDLH M3 19 55 a b c d e 3M 3M 3M 3M 3M 12021 ...
Page 172: ...171 ...
Page 175: ......