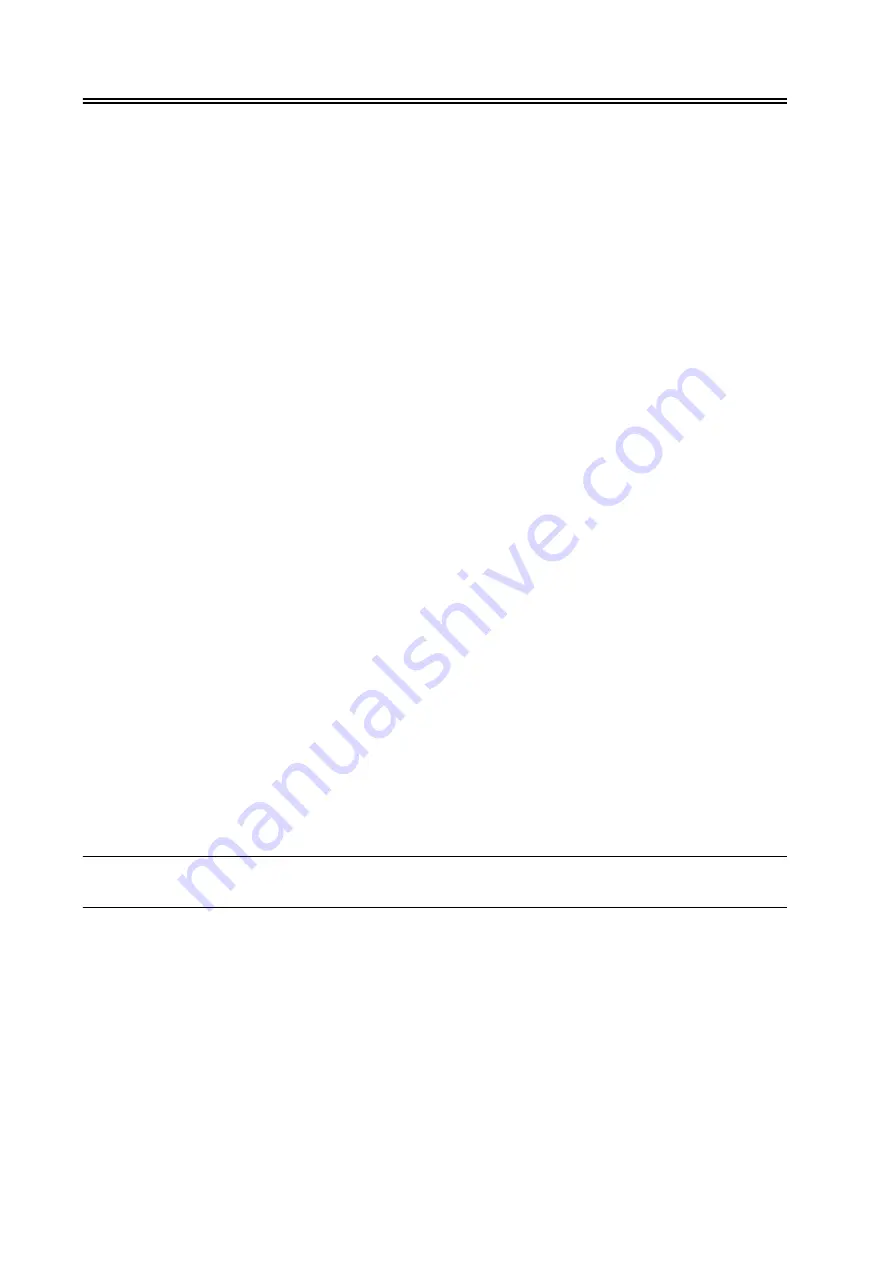
Operating Instructions
6-20
UNIT PROTECTION DEVICES
Units equipped with a TG-VI, MT µP-IV, µP-V, µP-VI, SR-2 or SR-3 controller use the microprocessor to protect the engine.
FUSES (TG-VI, MT µP-IV, µP-V, µP-VI , SR-2 and SR-3 control systems).
A number of fuses located on the relay board
protect unit circuits and components.
• A 40 amp fuse protects the main power circuit.
• 25 amp fuses protect the remote evaporator fan motors on SL TCI and SL Spectrum models.
• 15 amp fuses protect the damper motor or solenoid; high speed solenoid; and various control relays and components.
• Several 3 amp fuses protect microprocessor circuits, control relay circuits, remote light circuits (optional) and other
components.
NOTE: Refer to the unit wiring diagram or the appropriate Controller Operation and Diagnosis Manual for additional fuse
number and size information.
LOW OIL PRESSURE SWITCH.
The low oil pressure switch confirms that the engine oil pressure is within tolerance. If low,
the oil switch will close and the unit will record an alarm.
LOW OIL LEVEL SWITCH.
The low oil level switch closes if the crankcase oil level becomes too low. If the switch stays
closed for more than 30 seconds, the controller will shut the unit down and record an alarm.
HIGH PRESSURE CUTOUTS.
One or two high pressure cutouts (HPCO) are located in the compressor discharge manifold.
The HPCOs are pressure sensitive switches that open if the discharge pressure becomes excessive.
One switch (HPCO1) opens the circuit to the fuel solenoid which stops the engine during engine operation.
The other switch (HPCO2) (Model 50 Units Only) opens the circuit to the electric motor contactor, stopping the electric motor
during electric operation.
If either switch opens, the unit will shutdown and record an alarm.
HIGH PRESSURE RELIEF VALVE.
The high pressure relief valve is designed to relieve excess pressure within the
refrigeration system. The valve is a spring-loaded piston that lifts off its seat when refrigerant pressure exceeds 34.48 +/- 3.45
bar, 500 +/- 50 psi. The valve will reset when the pressure drops to 27.58 bar, 400 psi. The valve could possibly leak refrigerant
after it has relieved excess pressure. Tapping the valve lightly may help the valve reseat and SEAL PROPERLY. The valve is
non-repairable and requires no adjustment. If the valve fails to reseat properly, remove the refrigerant charge and replace the
valve.
The high pressure relief valve is located on a high pressure line near the condenser. The location of the valve directs refrigerant
away from anyone servicing the unit if pressure is expelled from the valve.
OVERLOAD RELAY (MODEL 50).
An overload relay protects the standby electric motor. The overload relay opens the
circuit from the motor contactor to the electric motor if the motor overloads (e.g., low line voltage or improper power supply)
while the unit is on electric standby operation. Press the Motor Reset switch to manually reset the overload relay.
EVAPORATOR HIGH TEMPERATURE PROTECTION (Model 50).
Units equipped with a TG-VI, MT µP-IV, µP-V,
µP-VI, SR-2or SR-3 controller use the controller and the evaporator coil sensor to provide evaporator high temperature
protection.
PREHEAT BUZZER.
The preheat buzzer sounds whenever the unit is starting in either diesel or electric mode operation.This
should warn anyone near the unit that the unit is about to start the diesel engine.
WARNING: The glow plugs (or air heater) do not always preheat before the engine starts.
Unit Operation
Visual Pre-trip Inspection
The following Pre-trip Inspection should be completed before starting the unit and loading the trailer. While the Pre-trip
Inspection is not a substitute for regularly scheduled maintenance inspections, it is an important part of the preventive
maintenance programme designed to prevent operating problems and breakdowns before they happen.
FUEL.
The diesel fuel supply must be sufficient to guarantee engine operation to the next check point.
NOTE: The diesel fuel must comply with EN590 standard
ENGINE OIL.
The engine oil level should be at the FULL mark with the dipstick NOT threaded into the oil pan. Never overfill.
Содержание SLXi Spectrum
Страница 17: ...Safety Precautions 2 5 Warning Decals...
Страница 18: ...Safety Precautions 2 6 Warning Decals Information Decals...
Страница 74: ...Unit Description 5 30...
Страница 128: ...Controller Operation 7 28...
Страница 156: ...Electrical Maintenance 8 28...
Страница 177: ...Engine Maintenance 9 21 Integral Fuel Solenoid Components 1 Integral Fuel Solenoid 2 O ring 3 Fuel Injection Pump Groove...
Страница 234: ...Refrigeration Maintenance 10 22...
Страница 309: ...13 Mechanical Diagnosis TK 482 TK 486 and TK 486V Engines 13 2...
Страница 316: ...Mechanical Diagnosis 13 8...
Страница 322: ...Refrigeration System Diagnosis 14 6...
Страница 332: ...Single Temperature Refrigeration System Diagrams 15 10...
Страница 339: ...Multi Temperature Refrigeration System Diagrams 16 7...
Страница 340: ...Multi Temperature Refrigeration System Diagrams 16 8...
Страница 342: ...Wiring Diagrams and Wiring Schematics 17 2...