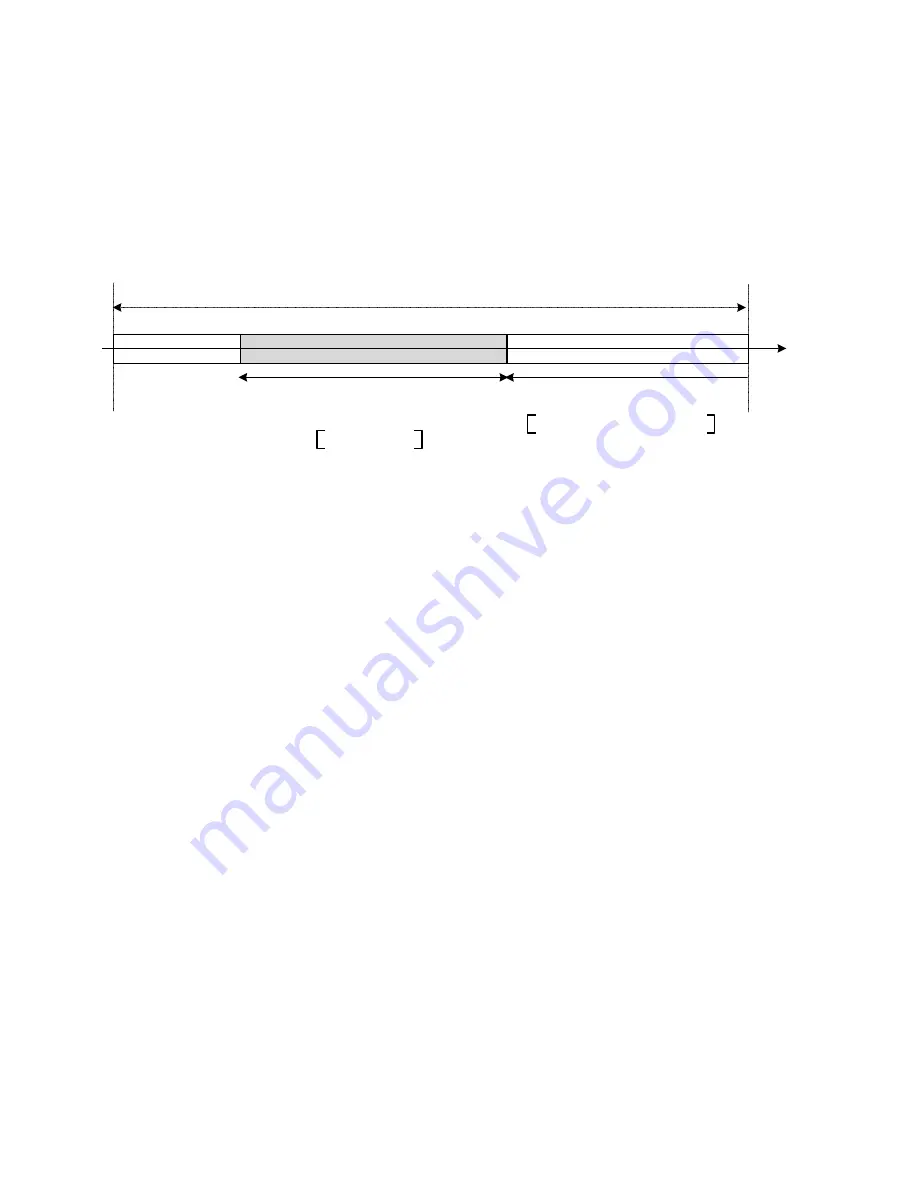
2.5 Holdover Mode
The DSPLL will automatically enter Holdover mode when the selected input clock becomes invalid and no other valid input clocks
are available for selection. It uses an averaged input clock frequency as its final holdover frequency to minimize the disturbance of
the output clock phase and frequency when an input clock suddenly fails. The holdover circuit stores up to 120 seconds of historical
frequency data while locked to a valid clock input. The final averaged holdover frequency value is calculated from a programmable
window within the stored historical frequency data. Both the window size and the delay are programmable as shown in the figure below.
The window size determines the amount of holdover frequency averaging. This delay value allows recent frequency information to be
ignored for Holdover in cases where the input clock source frequency changes as it is removed.
Programmable delay
Clock Failure
and Entry into
Holdover
time
0s
Historical Frequency Data Collected
Programmable historical data window
used to determine the final holdover value
120s
1s,10s, 30s, 60s
30ms, 60ms, 1s,10s, 30s, 60s
Figure 2.3. Programmable Holdover Window
When entering Holdover, the DSPLL will pull its output clock frequency to the calculated averaged holdover frequency. While in
Holdover, the output frequency drift is determined by the reference clock temperature drift. If a clock input becomes valid, the DSPLL
will automatically exit the Holdover mode and reacquire lock to the new input clock. This process involves pulling the output clock
frequency to achieve frequency and phase lock with the input clock. This pull-in process is Glitchless and its rate is controlled by the
DSPLL bandwidth or the Fastlock bandwidth, if Fastlock is enabled. These options are register programmable.
The recommended mode of exit from holdover is a ramp in frequency. Just before the exit begins, the frequency difference between the
output frequency while in holdover and the desired, new output frequency is measured. It is quite possible that the new output clock
frequency will not be exactly the same as the holdover output frequency because the new input clock frequency might have changed
and the holdover history circuit may have changed the holdover output frequency. The ramp logic calculates the difference in frequency
between the holdover frequency and the new, desired output frequency. Using the user selected ramp rate, the correct ramp time is
calculated. The output ramp rate is then applied for the correct amount of time so that when the ramp ends, the output frequency will
be the desired new frequency. Using the ramp, the transition between the two frequencies is smooth and linear. The ramp rate can be
selected to be very slow (0.2 ppm/sec), very fast (40,000 ppm/sec) or any of approximately 40 values that are in between. The loop
BW values do not limit or affect the ramp rate selections and vice versa. CBPro defaults to ramped exit from holdover. Ramping is also
used for ramped input clock switching. See
for more information. See
AN1057: Hitless Switching using
for more information on Hitless and Ramped Switching with Rev. E devices.
As shown in
Figure 2.1 Modes of Operation on page 10
the Holdover and Free run modes are closely related. The device will only
enter Holdover if a valid clock has been selected long enough for the holdover history to become valid, i.e., HOLD_HIST_VALID = 1.
If the clock fails before the combined HOLD_HI HOLD_HIST_DELAY time has been met, HOLD_HIST_VALID = 0 and the
device will enter Free run mode instead. Note that when switching between input clocks with different (non-0 ppm offset) frequencies,
the holdover history requires a time of 2 * HOLD_HI HOLD_HIST_DELAY to update the average frequency value. If a switch
is initiated before this time, the average holdover frequency will be a value between the old input frequency and the new one.
Note:
The Holdover history accumulation is suspended when the input clock is removed and resumes accumulating when a valid input
clock is again presented to the DSPLL.
Si5386 Rev. E Reference Manual • Modes of Operation
Skyworks Solutions, Inc. • Phone [781] 376-3000 • Fax [781] 376-3100 • [email protected] • www.skyworksinc.com
14
Rev. 1.2 • Skyworks Proprietary Information • Products and Product Information are Subject to Change Without Notice • December 9, 2021
14