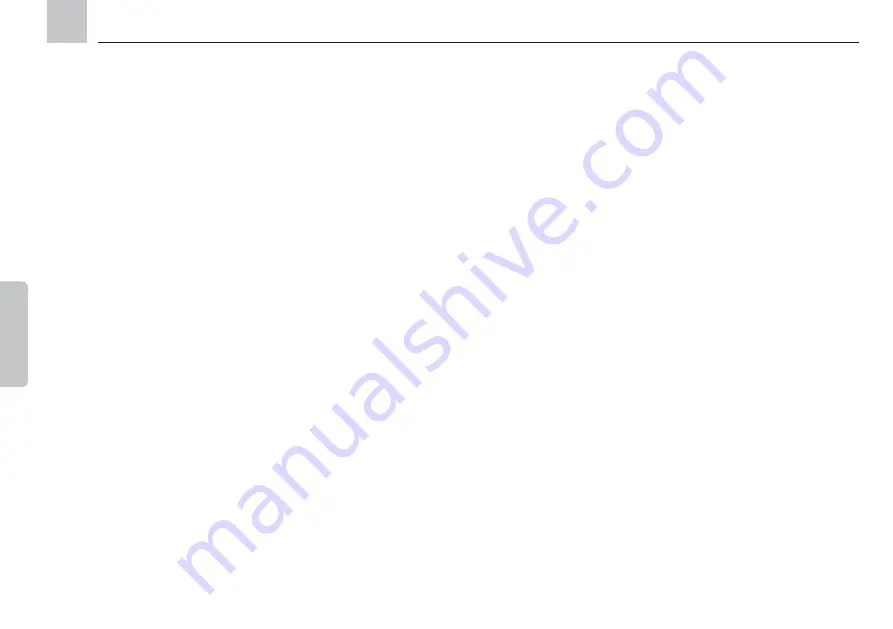
Page 64
EN
6.3.5 Conigurable parameters
The control unit contains 16 pre-set sets of
parameter data which can be programmed
as desired. A parameter set contains all the
information required to control and monitor
the lubrication process, e.g., the number of
lubrication zones, the interval times, the pump
cycle times, the number of cycles, etc.
6.3.4 Display and documentation functions
During system operation, current operational
data (status data) is stored in the FRAM and
can be read at any time.
If the control unit is switched off or loses
power, the most recent status data remains in
the FRAM. When the control unit is turned on
again, it reads the saved data and the lubrica-
tion process continues where it left off, unless
the coniguration has been changed (zero
voltage signal).
All faults detected by the lubrication system's
monitoring functions are also given a time
stamp and stored persistently in the control
unit's non-volatile memory area.
6.3.3.7 Monitoring unit temperature
The printed circuit board of the LC-CAN 5000
control unit contains a temperature sensor. If
the temperature in the unit exceeds the limit
value (see Technical Data, Chapter 13), the
system is switched off and enters fault mode
(see Chapter 11).
6. Functional description in progressive systems
KF
G
C
Содержание KFG
Страница 115: ......