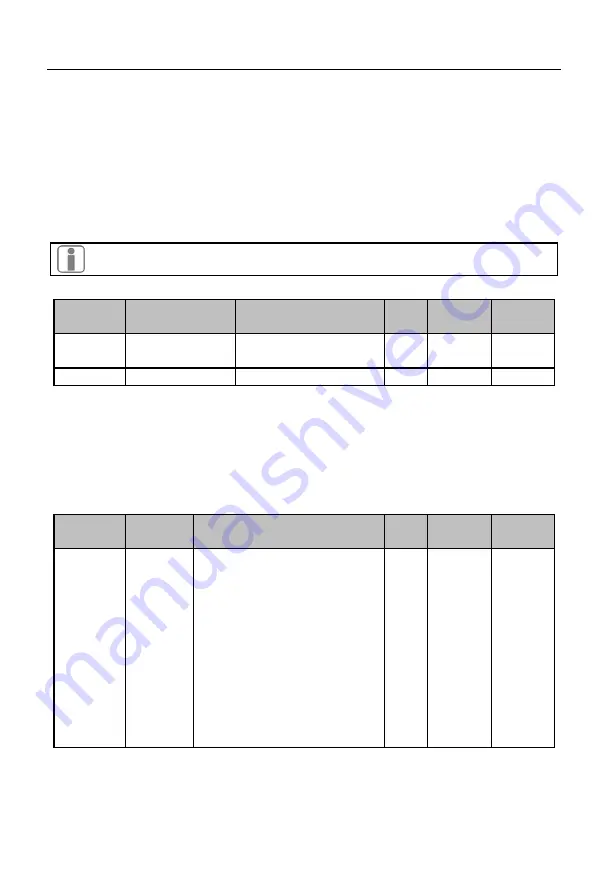
User Manual of A90 Series Inverter
162
reverse rotation. If the inverter is started immediately, it may have an overcurrent fault. In
order to avoid such faults, it is necessary to perform DC braking to stop the motor and then
make the motor run in the set direction to the set frequency before the inverter is started.
When F04.03 is set to different values, DC braking torques can be enabled.
F04.04 is used to set the time to enable DC braking. The inverter will start running
once the set time is up. If F04.04=0.00, DC braking is invalid during start.
★
DC braking is started as shown in Fig. 7.
When multiple motors are driven by a single inverter, this function can be applied.
Function
code
Function code
name
Parameter description
Unit
Default
setting
Attribute
F04.06
Pre-excitation
current
50.0-500.0 (100.0 =
no-load current)
%
100.0
○
F04.07
Pre-excitation time 0.00 - 10.00
s
0.10
○
The inverter will start running after the magnetic field is established according to the
set pre-excitation current F04.06 and the set pre-excitation time F04.07 is up. If the
pre-excitation time is set to 0, the inverter will be started directly without pre-excitation.
The pre-excitation current F04.06 is the percentage relative to the rated no-load current
of the motor.
Function
code
Function
code name
Parameter description
Unit
Default
setting
Attribute
F04.08
Speed
tracking
mode
Ones place: Tracking start
frequency
0: maximum frequency
1: stop frequency
2: power frequency
Tens place: Selection of search
direction
0: search only in command
direction
1: Search in the opposite direction
if the speed cannot be found in the
command direction
0
○
When the speed tracking start mode (F04.00=1) is selected, the inverter will be subject
to speed tracking according to the setting of F04.08 during the start. For quicker tracking to