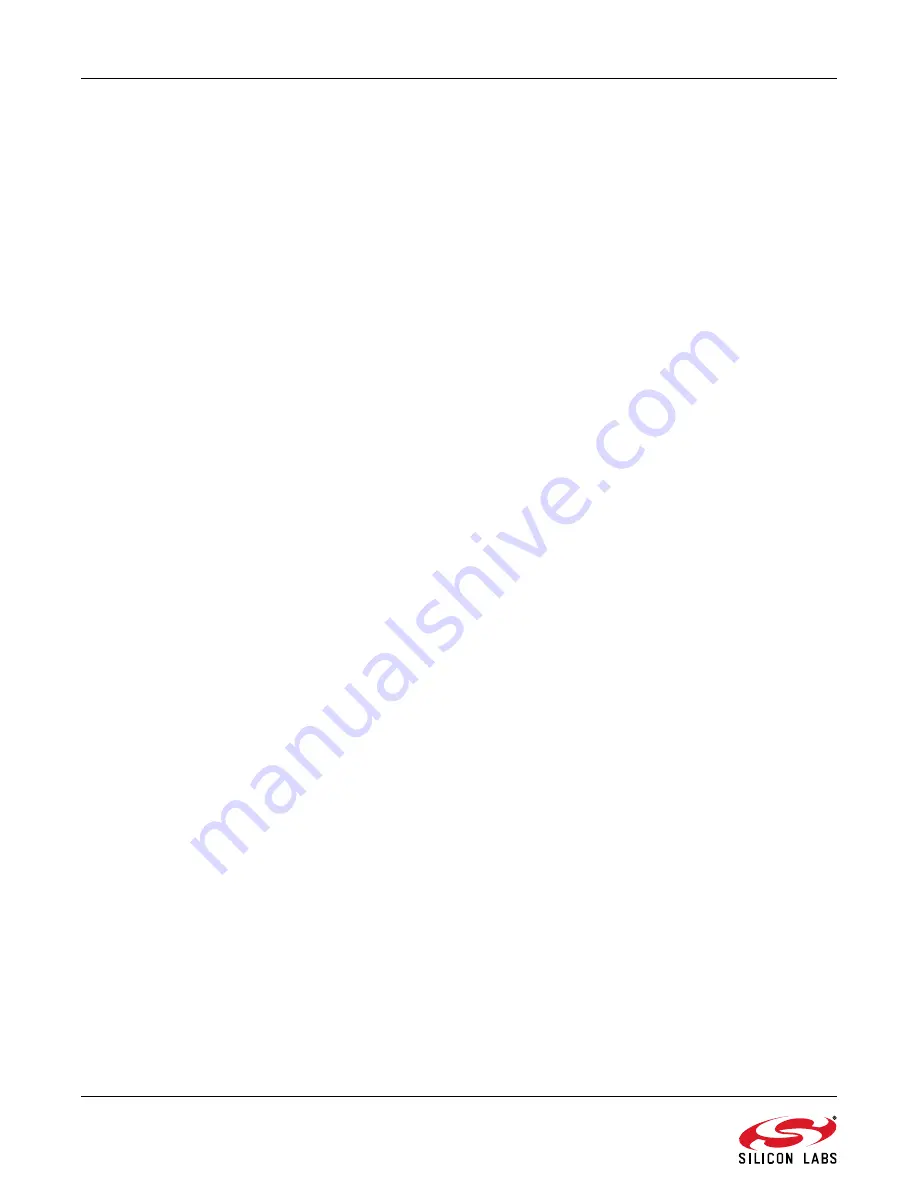
Si5345-44-42-D-RM
78
Rev. 1.0
13.2. Power Supply Recommendations
The power supply filtering generally is important for optimal timing performance. The Si5345/44/42 devices have
multiple stages of on-chip regulation to minimize the impact of board level noise on clock jitter. Following
conventional power supply filtering and layout techniques will further minimize signal degradation from the power
supply.
It is recommended to use a 0402 1 µF ceramic capacitor on each power supply pin for optimal performance. If the
supply voltage is extremely noisy, it might be necessary to use a ferrite bead in series between the supply voltage
and the power supply pin.
13.3. Power Supply Sequencing
Four classes of supply voltages exist on the Si5345/44/42:
1. VDD = 1.8 V (Core digital supply)
2. VDDA = 3.3 V (Analog supply)
3. VDDOx = 1.8/2.5/3.3 V ± 5% (Clock output supply)
4. VDDS = 1.8/3.3 V ± 5% (Digital I/O supply)
There is no requirement for power supply sequencing unless the output clocks are required to be phase aligned
with each other. In this case, the VDDO of each clock which needs to be aligned must be powered up before VDD
and VDDA. VDDS has no effect on output clock alignment.
If output-to-output alignment is required for applications where it is not possible to properly sequence the power
supplies, then the output clocks can be aligned by asserting the SOFT_RST 0x001C[0] or Hard Reset 0x001E[1]
register bits or driving the RSTB pin. Note that using a hard reset will reload the register with the contents of the
NVM and any unsaved changes will be lost.
Note:
One may observe that when powering up the VDD = 1.8 V rail first, that the VDDA = 3.3 V rail will initially follow the
1.8 V rail. Likewise, if the VDDA rail is powered down first then it will not drop far below VDD until VDD itself is
powered down. This is due to the pad I/O circuits which have large MOSFET switches to select the local supply
from either the VDD or VDDA rails. These devices are relatively large and yield a parasitic diode between VDD and
VDDA. Please allow for both VDD and VDDA to power-up and power-down before measuring their respective
voltages.
13.4. Grounding Vias
The pad on the bottom of the device functions as both the sole electrical ground and primary heat transfer path.
Hence it is important to minimize the inductance and maximize the heat transfer from this pad to the internal
ground plane of the PCB. Use no fewer than 25 vias from the center pad to a ground plane under the device. In
general, more vias will perform better. Having the ground plane near the top layer will also help to minimize the via
inductance from the device to ground and maximize the heat transfer away from the device.