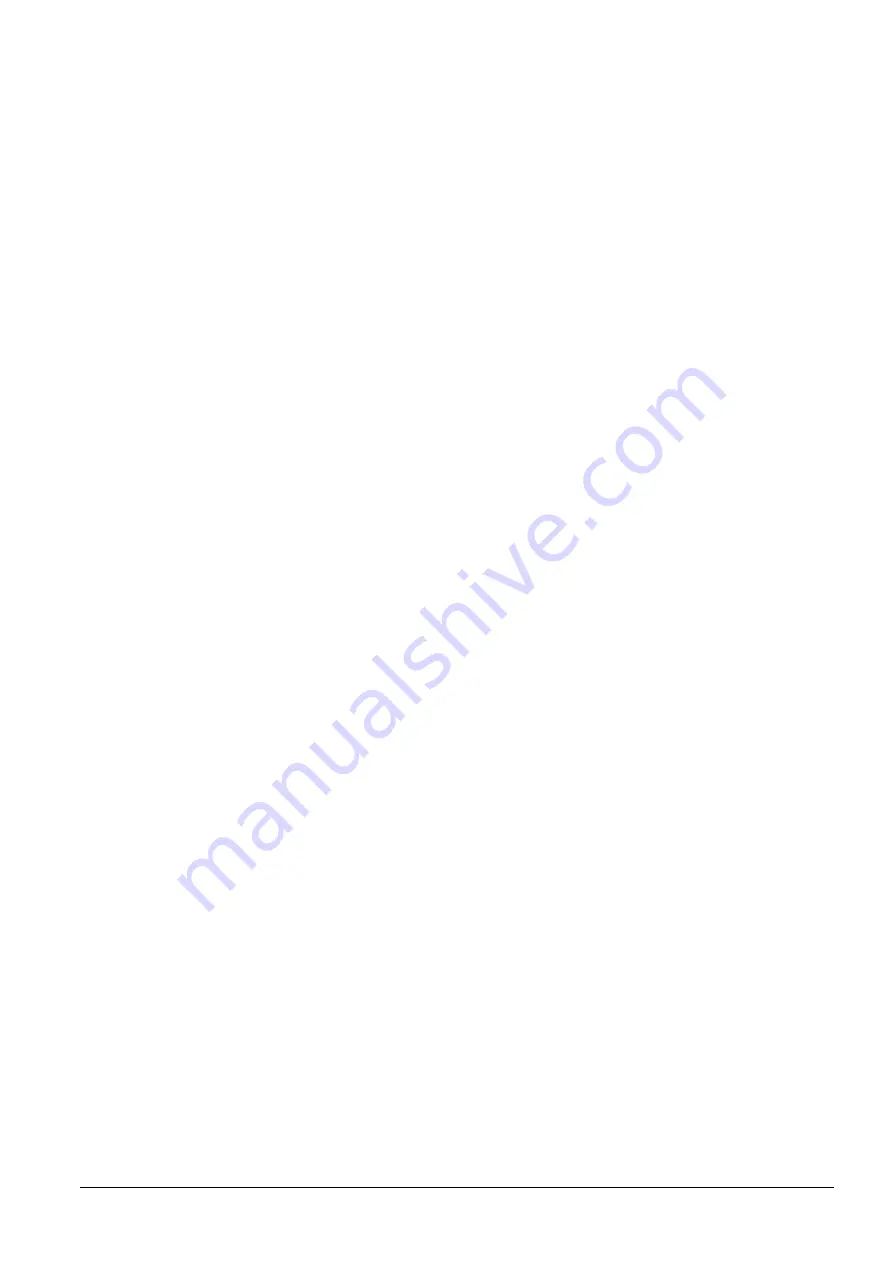
3
Building Technologies
FL-III Maintenance and Repair
CPS Fire Safety
08.2012
1
About this Document..............................................................................4
1.1
Documentation structure...........................................................................4
1.2
Purpose of the document..........................................................................4
1.3
Qualified personnel ...................................................................................4
1.4
Warranty and liability.................................................................................5
1.5
Legal notices .............................................................................................5
2
Safety .......................................................................................................6
2.1
Safety instructions.....................................................................................6
2.2
General safety...........................................................................................6
2.3
Electrical safety .........................................................................................7
2.4
Laser safety...............................................................................................7
2.5
Application specific safety.........................................................................9
3
Maintenance ..........................................................................................10
3.1
General ...................................................................................................10
3.2
Maintenance work on the controller........................................................10
3.2.1
The controller ..........................................................................................10
3.2.2
Regular maintenance work .....................................................................13
3.3
Maintenance work on the sensor cable ..................................................14
3.3.1
Tools .......................................................................................................14
3.3.2
Cleaning the fibre-optical connectors......................................................15
3.3.3
Cleaning the internal fibre-optical connectors.........................................17
4
Fault Diagnostics ..................................................................................21
4.1
Hardware.................................................................................................21
4.1.1
The controller does not show a response, no LED is lit..........................21
4.1.2
The controller does not show a response, LED “Power On” is lit ...........23
4.1.3
The controller does not start the measurement ......................................24
4.2
Software ..................................................................................................24
4.2.1
Status messages, Quick Start.................................................................24
4.2.2
Errors ......................................................................................................25
4.2.3
Warnings .................................................................................................26
4.2.4
Messages................................................................................................26
5
Repairs ...................................................................................................27
5.1
General ...................................................................................................27
5.1.1
Tools .......................................................................................................27
5.2
Repairs on the closed controller .............................................................28
5.2.1
Replacement of the fuse .........................................................................28
5.2.2
Replacement of the memory card...........................................................29
5.3
Repairs on the open controller................................................................31
5.3.1
General ...................................................................................................31
5.3.2
Battery replacement................................................................................34
5.3.3
Power supply replacement......................................................................36
5.3.4
Interface cards replacement or expansion..............................................42
5.4
Repair of sensor cables ..........................................................................50
6
Accessories and Spare Parts ..............................................................51
7
Repair Report ........................................................................................51