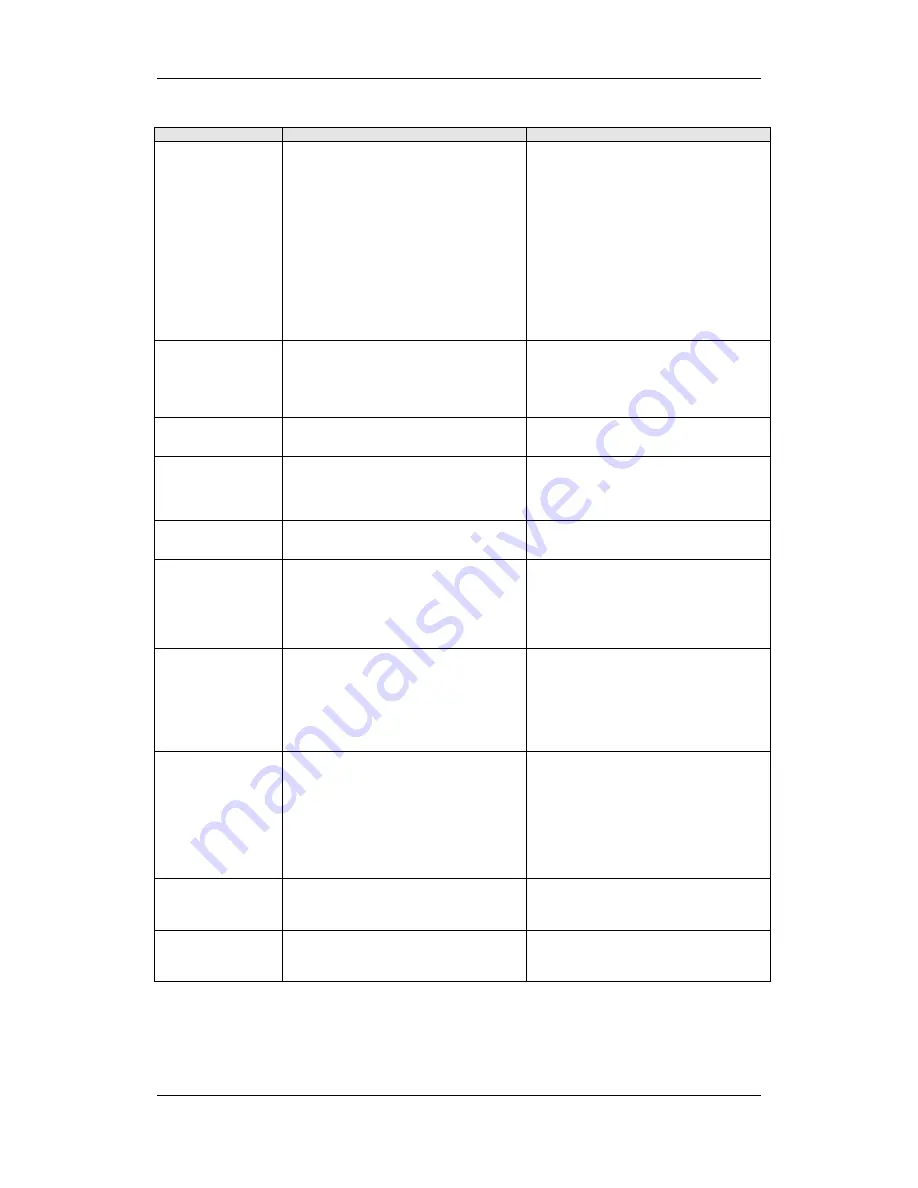
10.2001
Faults and Alarms
Siemens AG
6SE7087-6JP60
SIMOVERT MASTERDRIVES
Operating Instructions
13-19
Number / Alarm
Cause
Counter-measure
A022
Inverter temperature
The threshold for initiating an alarm has been
exceeded.
- Measure intake air or ambient temperature.
- Observe the derating curves at theta >50°C
(Compact PLUS) or 40°C.
Check
- Whether the fan -E1 is connected and is
rotating in the correct direction.
-The air intake and discharge openings for
blockage.
- The temperature sensor at -X30.
- r833 indicates the maximum converter
temperature of all existing measuring points.
A023
Motor temperature
The parameterizable threshold for initiating an
alarm has been exceeded.
Check the motor (load, ventilation, etc.). The
current temperature can be read in r009 Motor
Tmp.
Check the KTY84 input at connector
-X103:29,30, or -X104:29,30 (Compact PLUS)
for short-circuit.
A024
Motor movement
The motor has moved during motor data
identification.
Lock the motor.
A025
I2t Inverter
If the instantaneous load condition is
maintained, then the inverter will be thermally
overloaded.
Check:
- P72 Rtd Drive Amps
- MLFB P70
- P128 Imax
- r010 Drive Utilizat
A026
Ud too high
Ud is above the continuously permissible DC
link voltage for more than 30sec in a time
interval of 90sec
A029
I2t motor
The parameterized limit value for the I2t
monitoring of the motor has been exceeded.
Motor load cycle is exceeded!
Check the parameters:
P382 Motor Cooling
P383 Mot Tmp T1
P384 Mot Load Limits
A033
Overspeed
Bit 3 in r553 status word 2 of the septoint
channel. The speed actual value has
exceeded the value of maximum speed plus
the set hysteresis.
P804 Overspeed Hys plus
P452 n/f(max, FWD Spd) or
P453 n/f(max, REV Spd) has been exceeded
Increase the parameter for the maximum
frequencies or reduce the regenerative load.
A034
Setpoint/actual value
deviation
Bit 8 in r552 status word 1 of the setpoint
channel. The difference between freqeuncy
setpoint/actual value is greater than the
parameterized value and the control
monitoring time has elapsed.
Check
- whether an excessive torque requirement is
present
- whether the motor has been dimensioned too
small.
Increase values P792 Perm Deviation Frq/
set/actual DevSpeed and P794 Deviation Time
A035
Wire break
The clockwise and/or the counter-clockwise
rotating field is not enabled, or a wire
breakage is present in the terminal wiring
(both control word bits are zero)
Check whether cable(s) to the corresponding
digital input(s) P572 Src FWD Spd / P571 Src
REV Spd is (are) interrupted or released
A036
Brake checkback
"Brake still closed"
The brake checkback indicates the "Brake still
closed" state.
Check brake checkback (see FD 470)
Aotewell Ltd
www.aotewell.com
Industry Automation
HongKong|UK|China
+86-755-8660-6182