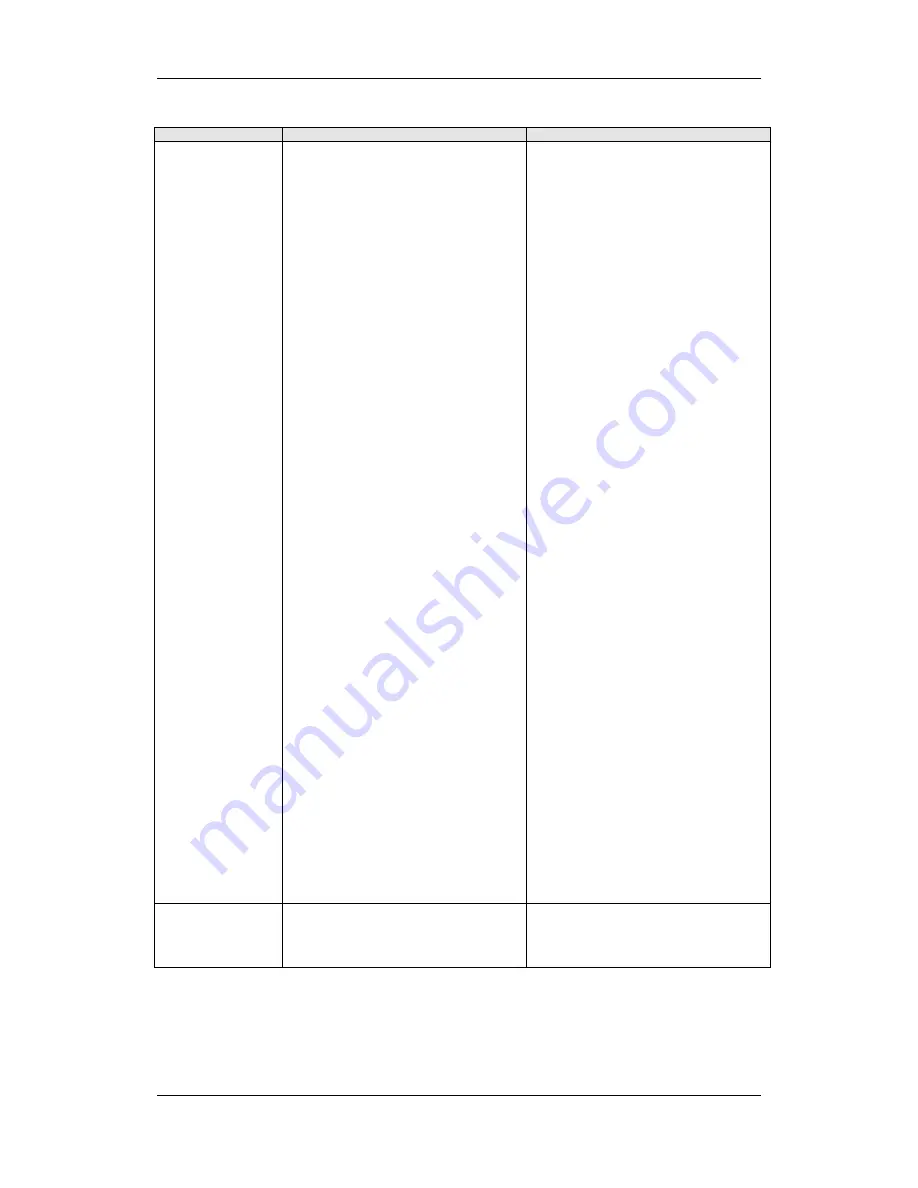
10.2001
Faults and Alarms
Siemens AG
6SE7087-6JP60
SIMOVERT MASTERDRIVES
Operating Instructions
13-3
Number / Fault
Cause
Counter-measure
F015
Motor stall
Motor has stalled or is locked:
- if the static load is too high
- if the acceleration or deceleration time is too
fast, or if load change is too fast and too great,
- due to incorrect parameterization of the pulse
encoder pulse number P151 or of the analog
tachometer scaling P138
- due to disturbed speed signals (tachometer
shield not connected)
The fault is only generated after the time set in
P805.
The binector B0156 is set in the status word 2
r553 Bit 28.
To detect whether the drive is blocked, see
P792 (Perm Deviation) and P794. With n/f
control, this fault is tripped if the torque limits
have been reached (B0234).
With speed control (P100 = 4) and master
drive (see P587), the fault can also point to an
interruption in the encoder cable. This case
has the same significance as if the drive is
locked.
With v/f control, the I(max) controller has to be
activated (P331). The monitor does not
operate with v/f textile applications (P100 = 2).
Motor has stalled or is locked:
In the case of synchronous motors (P095 =
12, 13): by reaching the maximum frequency
In the case of externally excited synchronous
motors (P095 = 12): as a result of missing or
excessively high excitation current (flux is too
small or too great).
When the maximum frequency (including
control reserves) (B0254) has been reached
on synchronous motors, the fault is generated
immediately. If the deviations in the rotor flux
are too great, first of all, the converter current
is switched to zero, the excitation current is
reduced and, after some time, the fault
message is tripped at the level of the double
damping time constant (2*r124.1). During this
wait time, the status word bit B0156 (r553.28)
is set already.
- Reduce load
- Release brake
- Increase current limits
- Increase P805 PullOut/BlckTime
- Increase P792 response threshold for
set/actual deviation
Only for f/n/T control (P100 = 3, 4, 5)
- Increase torque limits or torque setpoint
Only n/T control or v/f control with speed
controller: (P100 = 0, 4, 5)
- Check tachometer cable break
- Check pulse encoder pulse number
-Check analog tachometer scaling
- Connect shield of tachometer cable on motor
side and converter side
- Reduce smoothing of speed pre-control P216
(only n/T control) only frequency control:(P100
= 3)
- Slow down acceleration time (see also P467
ProtRampGen Gain). Increase current in the
lower frequency range (P278, P279, P280)
- Switch in speed controller pre-control
(P471>0). Set EMF controller more
dynamically (315) to max. approx. 2
- Increase changeover frequency for the EMF
model (P313). Replace by speed control with
pulse encoder in the case of overmodulated
n/f controller
- Track speed setpoint with the speed actual
value so that the set/actual deviation is always
less than that set in P792.
Only for synchronous motor: (P095 = 12)
- Check current limits of the excitation unit.
- Check excitation current setpoint and actual
value (incl. wiring)
- Check voltage limits of the excitation unit
during dynamic current changes.
- Check drive system for resonance
oscillations.
F017
SAFE STOP
Compact PLUS only
SAFE STOP operating or failure of the 24 V
power supply during operation (only for
Compact PLUS units)
Jumper applied for SAFE STOP?
SAFE STOP checkback connected?
On Compact PLUS units: check 24 V supply
Aotewell Ltd
www.aotewell.com
Industry Automation
HongKong|UK|China
+86-755-8660-6182