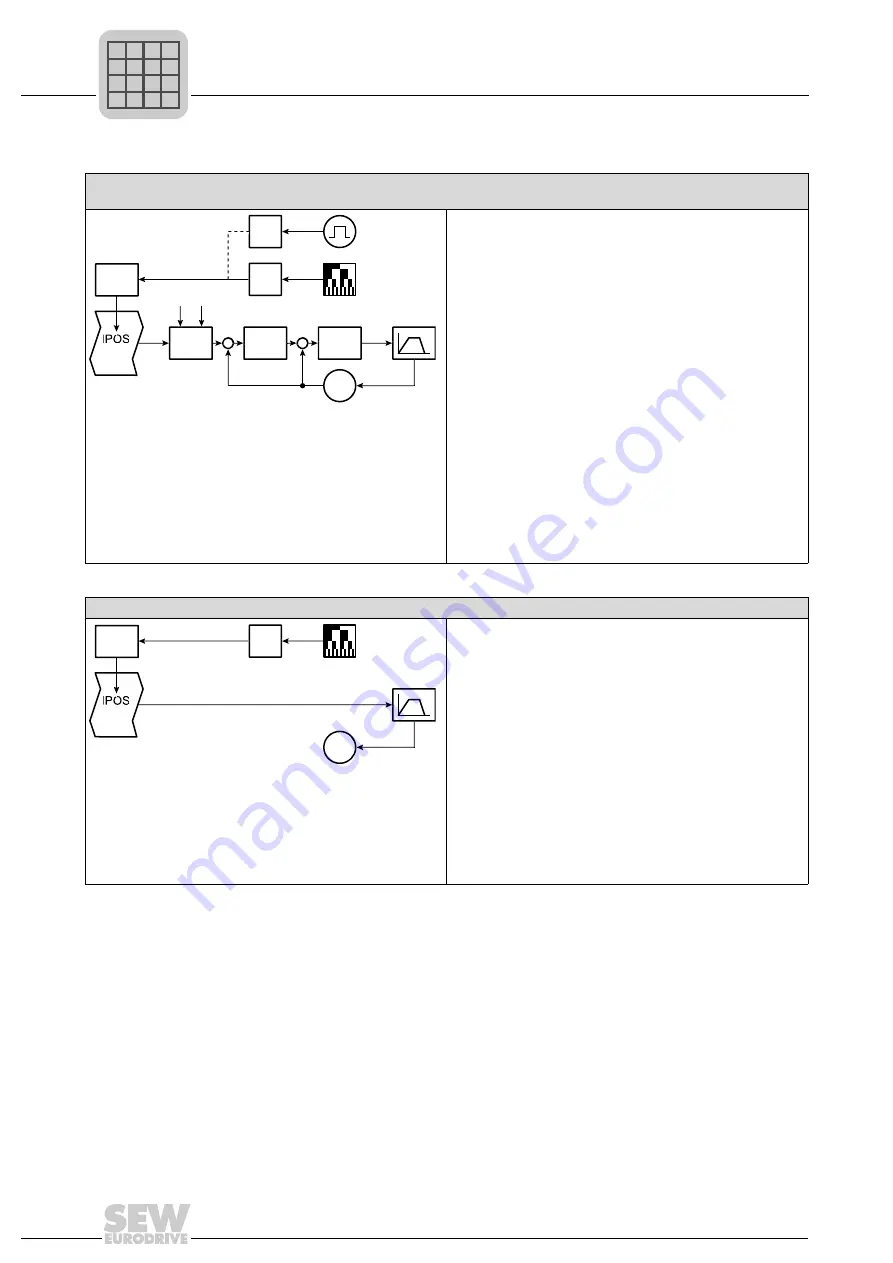
56
Manual – IPOSplus®
6
Encoder combinations
Position Detection and Positioning
Position control with motor encoder,
Processing the second encoder in the IPOS
plus
®
program as master encoder
474583563
•
Position control is performed in IPOS
plus®
using the motor
encoder connected to X15.
•
An encoder is always required on the motor for speed
feedback.
•
The high dynamic response of the inverter can be used
directly for positioning.
•
The position information of the second encoder is mapped
automatically in an IPOS
plus®
variable and can be processed
using program control.
•
This design is used when the inverter runs in relation to a
second encoder (for example, synchronous angel or
electronic cam)
v
max
= maximum speed
a
max
=
maximum
acceleration
PG
= Profile generator
P
act
= Actual position of the motor encoder
PC
= Position controller
n
act
= Actual speed
nC
= Speed controller
ABS = absolute encoder
EXT
= external encoder
SV
= System variable
IPOS = IPOS
plus®
program
v
max
a
max
PG
PC
nC
n
act
M
+
+
-
DIP
ABS
P
act
-
SV
O
X14
EXT
Processing the absolute encoder position in the IPOS
plus
®
program
474585099
•
The position information of the absolute encoder is mapped
automatically in an IPOS
plus®
variable and can be processed
using program control.
•
The DIP11 or a HIPERFACE
®
encoder on X14 can be used in
particular to replace applications in which positioning usually
takes place using rapid speed/creep speed by means of
several proximity switches.
•
An incremental encoder^/resolver on the motor for speed
feedback is not required, you can use a standard
asynchronous motor. The operating mode "... & IPOS" is not
required.
•
Refer to the manual "Positioning with Absolute Encoder
DIP11" The application module "Absolute positioning" is
available in SHELL to perform this type of positioning task.
ABS = absolute encoder
SV
= System variable
IPOS = IPOS
plus®
program
n
thres
= Setpoint speed
M
DIP
ABS
SV
O
n
thres
P
i
f
kVA
Hz
n
P
i
f
kVA
Hz
n