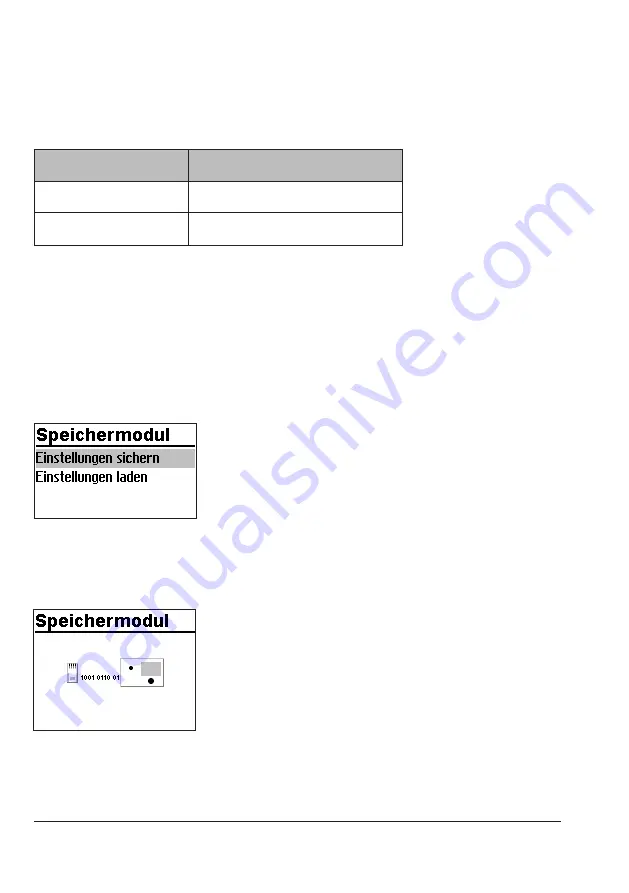
122
EQJW146F002 EN
Communication
All communication modules are designed for operation at the communication interface
coordinated. The interface properties cannot be parameterized.
Property
Setting
Baud rate
19200 Baud
Data bit, parity, stop bit
8 bits, none (no), 1 stop bit
For more details on the Communication accessory, refer to the Communication Connection
Manual.
10.1 Memory module
A memory module ( 0440210010) is particularly useful for transferring all the set data
from one EQJW146F002 controller to several other EQJW146F002 controllers.
- Pressing the control knob to confirm the “Save settings” display causes the controller
setting to be transferred to the memory module.
- Press the rotary pushbutton to confirm “Load settings” to transfer the settings from the
memory module to the controller.
The memory module is connected to the RJ-45 socket on the
side. After connection, "Save settings" appears in the con-
troller display. If the memory module already contains data
from another SAUTER EQJW146F002 controller, the "Load
settings" display can be called up by turning the control
During the data exchange a ticker consisting of zeros and
ones is displayed. After successful data transfer “Ok” ap-
pears in the display. The connection between controller and
memory module can then be disconnected.
Содержание EQJW146F002
Страница 2: ...2 EQJW146F002 EN ...
Страница 125: ...EQJW146F002 EN 125 Installation 1 2 2 5 3 4 5 62 15 41 57 Panel mounting Wall mounting Rail mounting Fig 9 Installation ...
Страница 158: ...158 EQJW146F002 EN ...
Страница 159: ......