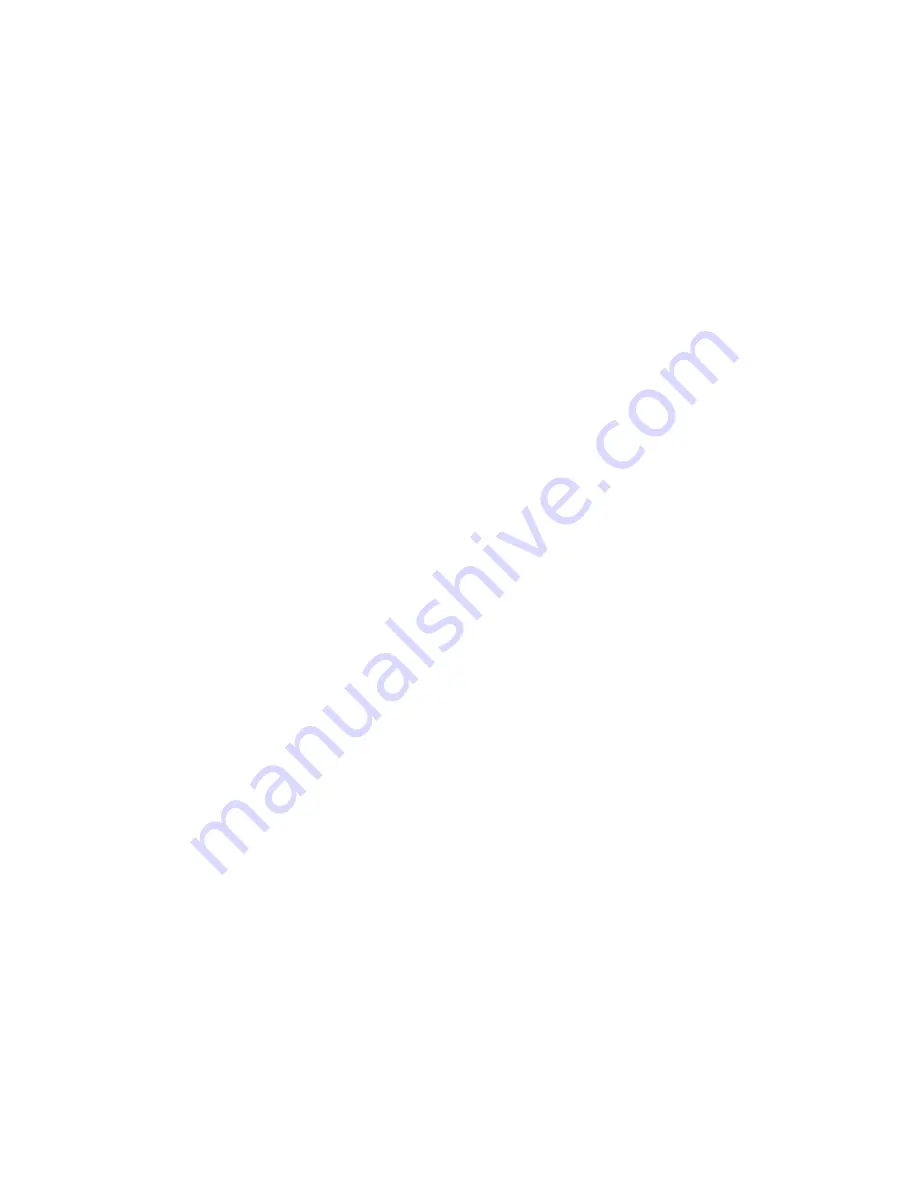
132
Gemini GV6K/GT6K Command Reference
FOLEN
Examples
Example #1:
The Gem6K drive is controlling a rotary motor, the master is a 1000-line incremental encoder mounted on
the back of an externally controlled motor, and programming units are to be revs/second (rps).
Stepper Products:
The follower will start ramping to a ratio of 1:1 when trigger #1 (TRG-1A) goes active. This
means the actual step ratio of follower to master is 25000 to 4000, or 6.25 follower steps for
every master. After 25 master revolutions, the follower will decelerate to a 0.5:1 ratio (3.125
follower steps for every master). After a total of 75 master revolutions, the follower will ramp
to zero ratio (i.e., stop) and repeat the cycle when trigger #1 is activated. All ramps to new
ratios, including zero ratio, take place over one master revolution.
Scaling Set Up:
(prior to defining program)
SCALE1
; Enable scaling
SCLD25000
; Set follower distance scale factor to 25,000 steps/rev
; (assumes a resolution of 25,000 steps/rev)
SCLMAS4000
; Set master scale factor to 4000 steps/rev
Servo Products:
The follower will start ramping to a ratio of 1:1 when trigger #1 (TRG-1A) goes active. This
means the actual step ratio of follower to master is 4000 to 4000, or 1 follower steps for every
master. After 25 master revolutions, the follower will decelerate to a 0.5:1 ratio (0.5 follower
steps for every master). After a total of 75 master revolutions, the follower will ramp to zero
ratio (i.e., stop) and repeat the cycle when trigger #1 is activated. All ramps to new ratios,
including zero ratio, take place over one master revolution.
Scaling Set Up:
(prior to defining program)
SCALE1
; Enable scaling
SCLD4000
; Set follower distance scale factor to 4,000 steps/rev
; (assumes an encoder resolution of 4,000 steps/rev)
SCLMAS4000
; Set master scale factor to 4000 steps/rev
The application program is defined as follows:
DEL FOLTST
; Delete program called FOLTST
DEF FOLTST
; Begin definition of program called FOLTST
INFNC1-H
; Set input #1 (TRG-1A) to be "trigger interrupt" (used with GOWHEN later)
COMEXC1
; Select continuous command processing mode
MC1
; Select continuous positioning mode
FOLMAS1
; Assign master encoder input as master
FOLMD1
; Follower should change ratios over 1 master revolution
FMCLEN100
; Set master cycle length to 100 revs
FOLRD1
; Set follower-to-master Following ratio denominator to 1
; (applies to all subsequent FOLRN commands)
FOLEN1
; Enable Following
D+
; Set motion to the positive- direction
$STRMV
; Label to repeat move
TRGFNA1
; Suspend execution of next move until trigger (TRG-1A) is active
TRGFNAx1
; Begin new master cycle (counter at 0) when trigger (TRG-1A) is active
FOLRN1
; Set follower-to-master Following ratio numerator to 1 (ratio set to 1:1)
GO1
; Start continuous Following move (when TRG-1A is active)
WAIT(AS.26=b0 AND FS.4=b1) ; Wait for profile to actually start
; (when TRG-1A is active) and be at ratio
GOWHEN(PMAS>=25) ; Suspend execution of next move until master position >= 25
FOLRN0.5
; Set Following ratio numerator to 0.5 (ratio set to 0.5:1)
GO1
; Initiate new move according to new Following ratio
; (when master position >= 25)
WAIT(AS.26=b0 AND FS.4=b1) ; Wait for profile to actually start
; (when master position >= 25) and be at ratio
GOWHEN(PMAS>=75) ; Suspend execution of next move until master position >= 75
FOLRN0
; Set Following ratio numerator to zero
; (ratio causes follower to ramp to stop)
GO1
; Initiate new move with new Following ratio (when master pos. >= 75)
WAIT(AS.26=b0 AND FS.1=b0) ; Wait for profile to actually start
; (when master position >= 75) and the follower is not moving
JUMP STRMV
; Repeat the cycle
END
; End of program
www.comoso.com
Содержание Gemini GT6K
Страница 24: ...www comoso com ...
Страница 40: ...www comoso com ...
Страница 344: ...www comoso com ...
Страница 350: ...www comoso com ...