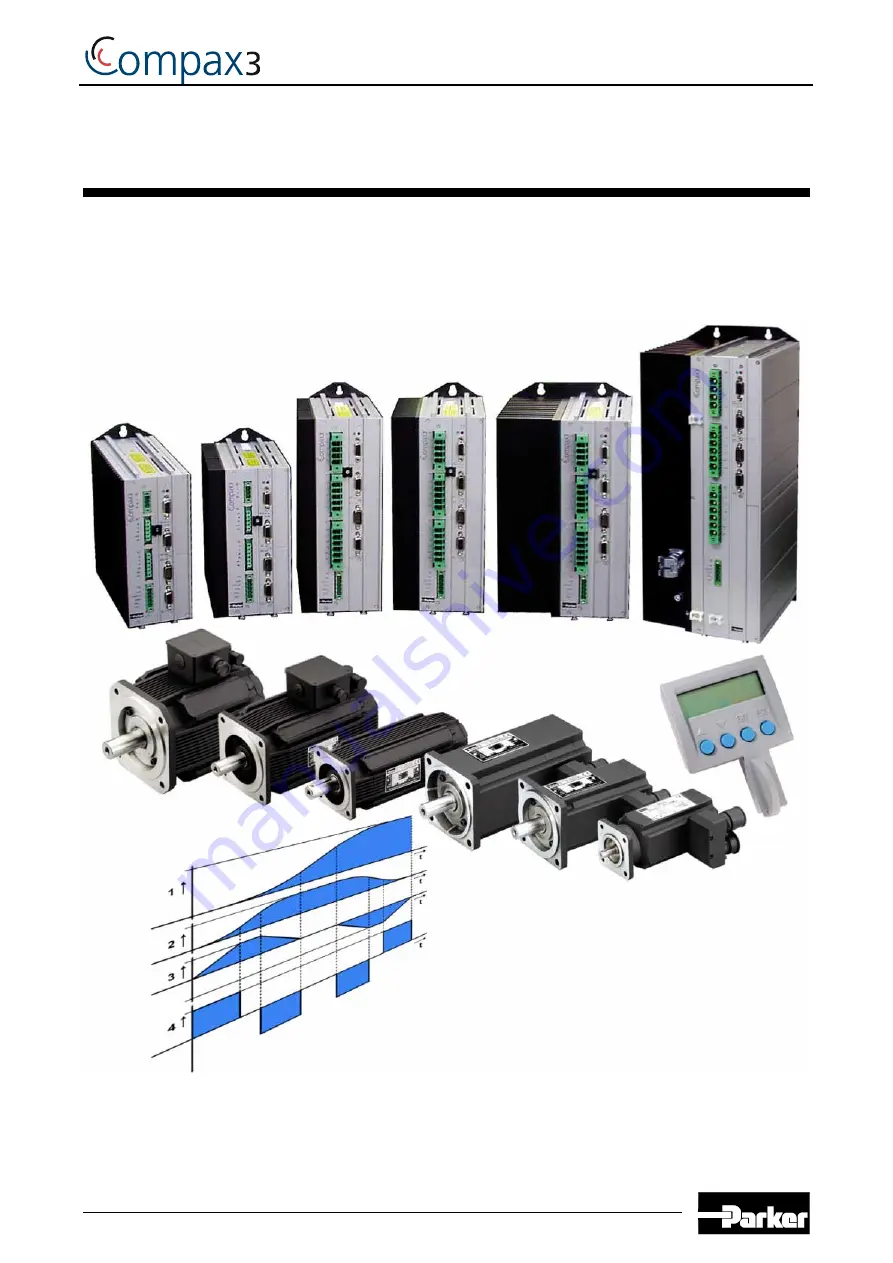
Electromechanical Automation
We reserve the right to make technical changes.
10.03.04 09:06
I11 T11 192-120101 N6 - March 2004
The data correspond to the technical state at the time of printing.
Operating instructions Compax3 I11 T11
Positioning via digital I/Os
I11 T11 192-120101 N6 - March 2004
Release 1/2004 (as from firmware V2.03)