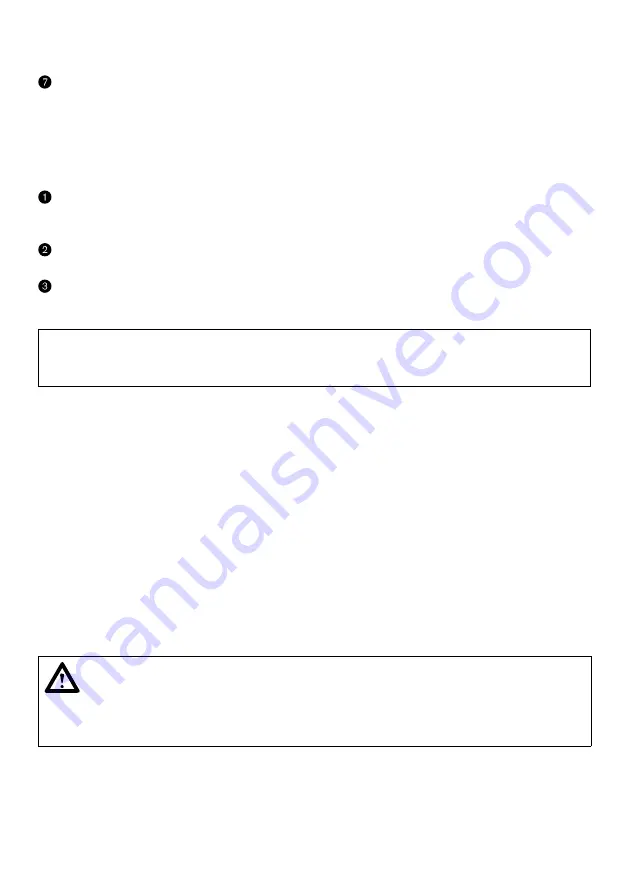
Ottobock | 19
3R60-PRO, 3R60-PRO=ST, 3R60-PRO=KD, 3R60-PRO=HD
4. Finally, tighten the screw with 25 Nm and insert the cover cap. It is very important to insert the
cover cap in the correct position.
Connect socket and knee using a corresponding adapter (e. g. 4R111, 4R41, 4R55, 4R51
Socket Adapter).
4.1.2 Static alignment optimization using 743L100 L.A.S.A.R. Posture
(the following steps refer to Fig. 13)
The bench alignment can be substantially improved using L.A.S.A.R. Posture. In order to ensure
an appropriate stability and at the same time an easy swing phase initiation, proceed as follows:
To make the load line visible, the transfemoral amputee stands on the L.A.S.A.R. Posture with
the prosthetic side on the force plate and with the other leg on the height compensation panel.
The prosthesis side should be sufficiently loaded (> 35 % of the body weight).
Now adapt the alignment by only adjusting the plantar flexion of the foot. The load line (laser
line) should be approx. 10 mm anterior to the lower front knee axis (see Fig. 13).
After step 2, dynamic optimization can take place between parallel bars (see Section 5).
4.2 Combination possibilities
Information
When fabricating a prosthesis for the lower limbs, all of the prosthetic components used have to
meet the requirements in regard to the patient’s body weight and activity level.
4.3 Adjustments and final assembly
4.3.1 Socket fabrication 3R60-PRO=KD
4.3.1.1 Lamination prior to trial fitting
Take a piece of 623T3 Perlon Stockinette twice the length of the plaster model and pull half of it
over the isolated socket. Twist the other half of the stockinette on the distal end and reflect it over
the socket. In order to absorb strong forces in the area of the modular knee joint, the socket must be
gradually reinforced with 616G13 Fiberglass Stockinette. To do this, pull over the first layer to 2/3 of
the socket length, tie it off and then reflect it up to half of the socket length. Put 2 layers of 616G12
Carbon-Fiber Cloth on the distal area so as to provide an underlying base with a projecting brim of
3 cm around the 4G70 Adapter, which will be mounted later in the procedure. Pull on two layers of
623T3 Perlon Stockinette. The socket lamination is performed in two stages. In the first stage the
socket is laminated up to 2/3 of its length with 617H19 Orthocryl Lamination Resin. In the second
stage the proximal part of the socket is laminated with 617H17 Orthocryl Flexible Resin. Once the
first casting has hardened, pull on 2 more layers of 623T3 Perlon Stockinette before laminating the
proximal part of the socket with 617H17 Orthocryl Flexible Resin.
Attention!
The lamination anchor acts as a flexion stop in the area of the EBS
PRO
pivoting mount
(Fig. 10). To provide this stop function, and in order to avoid damage to the knee joint,
an even contact surface in the area of the EBS
PRO
pivoting mount must be present after
final lamination.
4.3.1.2 Applying the lamination anchor
The correctly fitted lamination anchor must be prepared before it is glued to the socket. To do this, fill
the coupling opening with 636K8 Plastaband. Clamp the socket and joint into the alignment apparatus.
Содержание 3R60-PRO HD
Страница 3: ...2 3b 3a A B 5 4 F 6 ICR ICR ICR F F ICR ICR D E...
Страница 4: ...4 Ottobock 3R60 PRO 3R60 PRO ST 3R60 PRO KD 3R60 PRO HD 7 7 9 8 10 10 mm 25 Nm 11b 11a...
Страница 141: ...Ottobock 141 3R60 PRO 3R60 PRO ST 3R60 PRO KD 3R60 PRO HD 9 4 4 EBSPRO 3S107 Ottobock 519L5 4 5 A...
Страница 142: ...142 Ottobock 3R60 PRO 3R60 PRO ST 3R60 PRO KD 3R60 PRO HD Ottobock ISO 10328 5 5 1 5 2 CE 93 42 VII...
Страница 151: ...Ottobock 151 3R60 PRO 3R60 PRO ST 3R60 PRO KD 3R60 PRO HD 4 4 3R60 EBS PRO 3S107 519L5 4 5...
Страница 152: ...152 Ottobock 3R60 PRO 3R60 PRO ST 3R60 PRO KD 3R60 PRO HD ISO 10328 5 5 1 5 2 93 42 IX I VII...
Страница 160: ...160 Ottobock 3R60 PRO 3R60 PRO ST 3R60 PRO KD 3R60 PRO HD 4 4 3S107 519L5 4 5...
Страница 168: ...168 Ottobock 3R60 PRO 3R60 PRO ST 3R60 PRO KD 3R60 PRO HD ISO 10328 3 3 5 5 5 1 5 2 CE 93 42 EWG IX I VII...