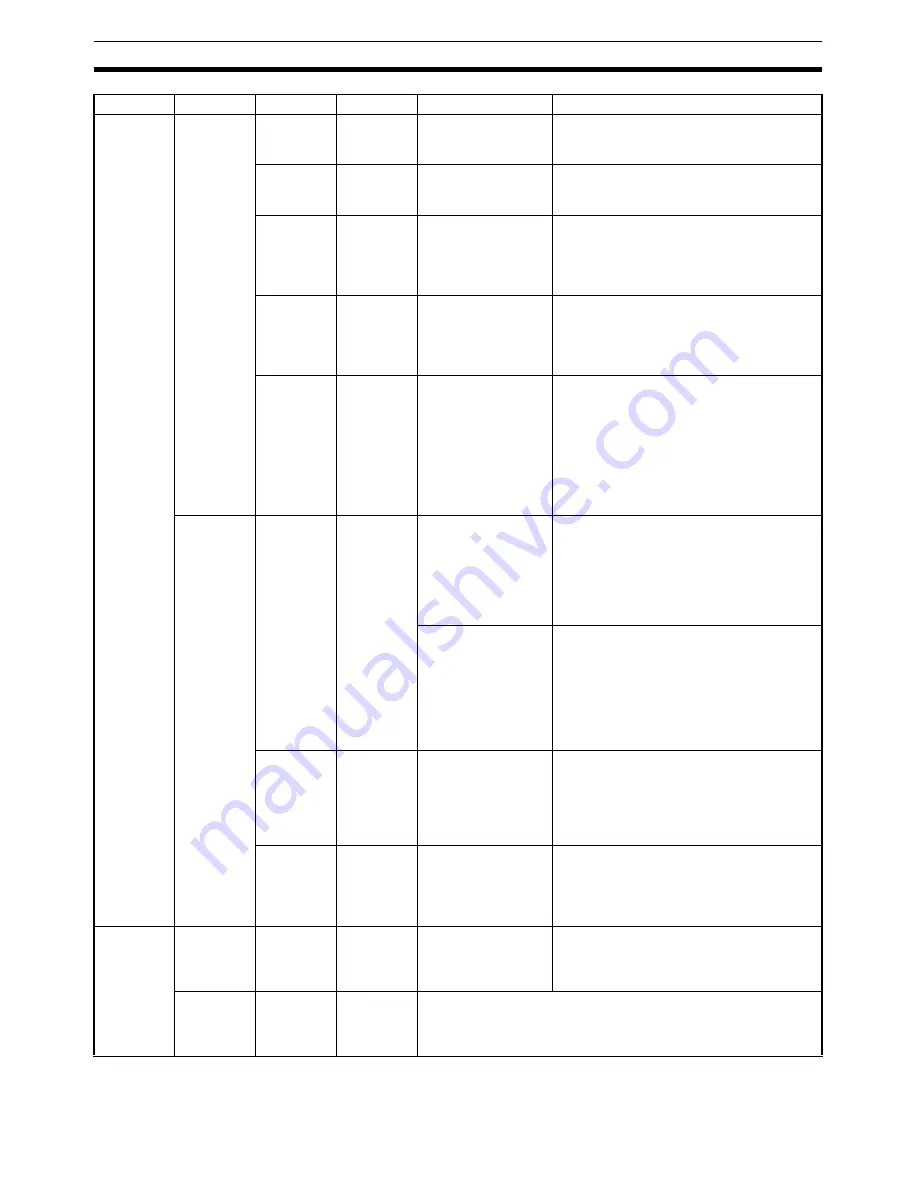
98
Error Codes
Section 11-2
MECHA-
TROLINK
slave sta-
tion device
errors
External
sensor
input
Forward
Rotation
limit input
3000
A forward rotation
limit input signal was
detected.
Execute ERROR RESET, and then perform
movement in the reverse rotation direction.
Reverse
Rotation
limit input
3001
A reverse rotation
limit input signal was
detected.
Execute ERROR RESET, and then perform
movement in the forward rotation direction.
Forward
software
limit
3002
The forward software
limit was reached or
exceeded during
axis movement.
Check the position command value and
executing ERROR RESET, and then exe-
cute a movement command to move the
axis to a correct position within the software
limit range.
Reverse
software
limit
3003
The reverse software
limit was reached or
exceeded during
axis movement.
Check the position command value and
executing ERROR RESET, and then exe-
cute a movement command to move the
axis to a correct position within the software
limit range.
Emergency
stop input
3004
Emergency stop
input signal in exter-
nal control inputs
was detected during
Servo lock, or Servo
lock was executed
during inputting the
emergency stop sig-
nal.
After clearing the emergency stop input,
execute the axis error reset and restart
operation from Servo lock status. (This error
will not occur when executing the Emer-
gency Stop command in Axis Operating
Memory.)
Origin
search
error
No origin
proximity or
origin input
signal
3020
The origin proximity
input signal could not
be detected within
the range of both
limit input signals
during an origin
search.
Check the origin proximity input signal wir-
ing and the signal's allocation setting in the
Servo Parameters. Check that the dog
width of the origin proximity input signal is
no shorter than the communications cycle.
After detecting the
origin proximity input
signal during an ori-
gin search operation,
a limit input signal
was detected before
detecting the origin
input signal.
Check that the origin input signal selection
in the Position Control Unit's Axis Parame-
ters is correct. When the external latch sig-
nal is selected as the origin input signal,
check the external latch signal wiring and
the allocation setting in the Servo Parame-
ters.
Limit input
already ON
3021
The limit input signal
in the origin search
direction has already
been input during a
single-direction ori-
gin search.
Check the limit input signal wiring for the
corresponding direction and check the limit
input signal's allocation setting in the Servo
Parameters.
Limit input
signal ON
in both
directions
3022
Origin search can-
not be executed due
to limit input signals
being input in both
directions.
Check the limit input signal wiring in both
directions and check the limit input signal
allocation settings in the Servo Parameters.
MECHA-
TROLINK
slave sta-
tion device
errors
Servo Drive
error
Servo Drive
main circuit
OFF error
3080
The main circuit
power of the Servo
Drive has been
turned OFF.
Check the power supply voltage being sup-
plied to the Servo Drive's main circuit power
supply and make sure the correct power is
being supplied.
MECHA-
TROLINK
device
alarm
---
4000 +
Alarm code
for each
device
The error processing depends on the device.
Category
Error name Error code
Probable cause
Clearing method
Содержание CX-MOTION-NCF - V1.8
Страница 2: ...CXONE AL C V3 CXONE AL D V3 CX Motion NCF Ver 1 8 Operation Manual Revised October 2008...
Страница 3: ...iv...
Страница 5: ...vi...
Страница 21: ...xxii Application Precautions 5...
Страница 33: ...12 Connecting to PLC Section 2 2...
Страница 36: ...15 Screen Name Section 3 1 Edit Parameter Windows...
Страница 37: ...16 Screen Name Section 3 1 Monitor Windows Axis Monitor Window Unit Monitor Window...
Страница 63: ...42 Editing Servo Parameters Section 5 2...
Страница 68: ...47 Print Section 6 5 Print Samples An example of printed Unit Parameters is shown below...
Страница 89: ...68 Writing to Flash Memory Section 7 6...
Страница 95: ...74 Axis Monitor Section 8 2 2 Click the OK Button to start communications i e establish connection...
Страница 103: ...82 Axis Monitor Section 8 2...
Страница 104: ...83 SECTION 9 Test Run Operation This section describes the test run operations for each axis 9 1 Test Run 84...
Страница 109: ...88 Test Run Section 9 1...
Страница 133: ...112 Index...
Страница 137: ...116 Revision History...