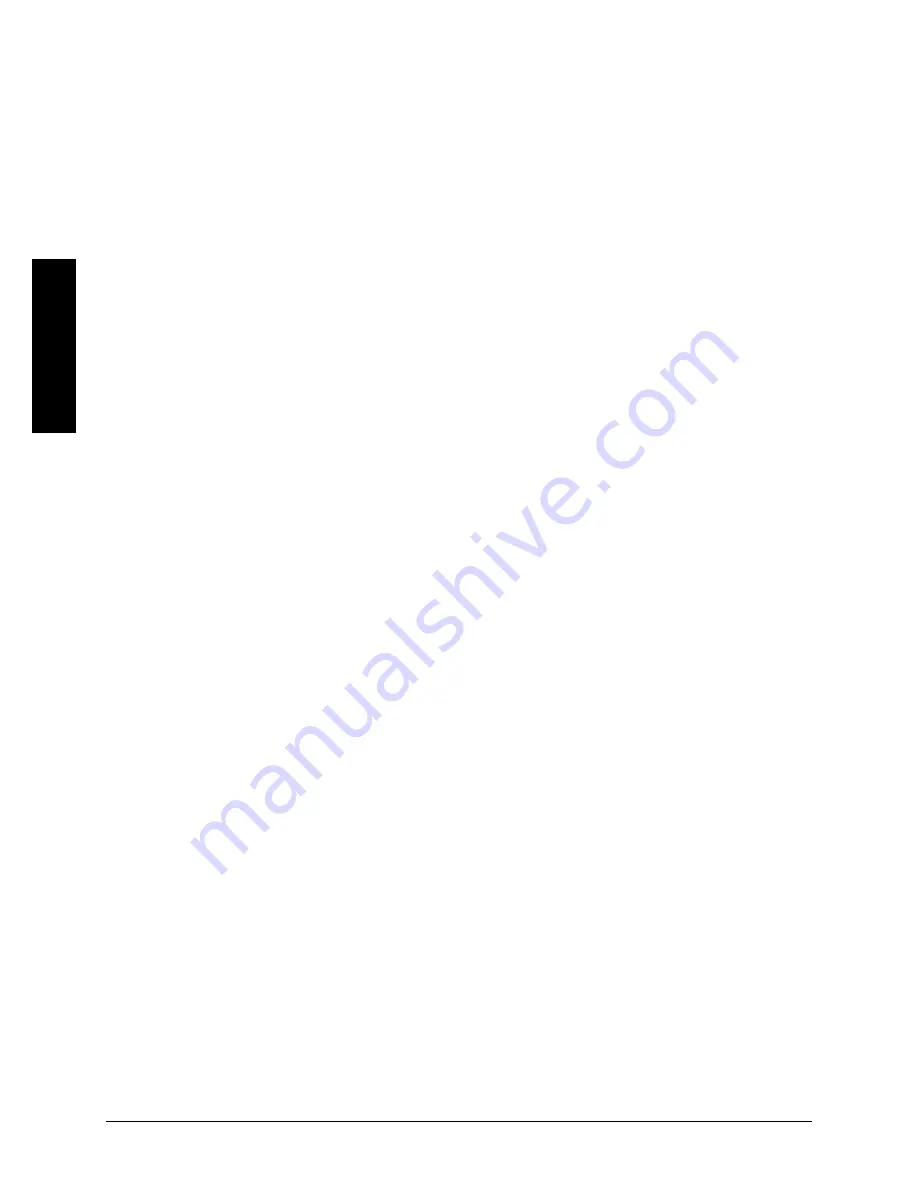
Page 100
Accumass BW500
PL-565
P
ID Control
Feed Forward Control,
F
On the BW500, the
F
term is used to adjust the control output based on a setpoint
change. The use of this term can make the system reach the new setpoint faster. If
the term is not used, the system responds using the
P
,
I
and
D
terms only. The
difference between the new setpoint and the process variable is the error and the
control algorithm responds to eliminate this new error.
When the
F
term is used and a new setpoint is entered, a proportion of the difference
between the new setpoint and the process variable is automatically added on to the
control output. This shifts the process variable closer to the new setpoint faster than
using the
P,
I
and
D
terms alone. This is done on a one time basis.
•
allowable input range:
0.000 to 1.000
•
typical operating range:
0.250 to 0.550
•
default value:
0.300
The PID control function of the BW500 can be configured to operate in several
modes.
•
controller output: direct acting
•
feedback: rate, load or external
•
control: local or remote (ratio) setpoint
PID Setup and Tuning
Proper tuning of the control PID terms is essential to system operation and optimum
performance from the feeder. The recommended procedures for tuning the PID
control terms at initial start-up are described in this section.
Initial Start-Up
Although the default values of the P,
I
, D and F terms will suit the majority of
applications, shearing weigh feeders in particular, some tuning will be necessary
nonetheless.
There are several techniques and procedures for tuning conventional PID controllers,
some work better depending upon the application. We recommend using "closed-
loop cycling" for the BW500 integrator/controller for feed rate control. This technique
focuses on tuning the P term first while disabling the
I
and D terms. This is followed
by adding and tuning the
I
term, then the D term. To outline this procedure:
1.
With the P term set to its default value of 0.400, disable the
I
, D and F terms by
setting them to 0.000.
2.
Enter a feed rate setpoint that is 30% of the designed maximum flow rate.
3.
Having applied the test weights or chain provided, start the feeder and observe the
time it takes the feeder to reach setpoint, also observe the oscillation around setpoint.
4.
Adjust the P term accordingly for consistent oscillation and error. Progressively
decrease the P term value if there is too much oscillation and error. Likewise,
Содержание ACCUMASS BW500
Страница 1: ...ACCUMASS BW500 Instruction Manual PL 565 January 2001 CCUMASS BW500 33455650 Rev 1 2...
Страница 6: ...Page 6 Accumass BW500 PL 565...
Страница 12: ...Page 12 Accumass BW500 PL 565 Specifications...
Страница 28: ...Page 28 Accumass BW500 PL 565 Installation...
Страница 88: ...Page 88 Accumass BW500 PL 565 Parameters...
Страница 94: ...Page 94 Accumass BW500 PL 565 Operation...
Страница 106: ...Page 106 Accumass BW500 PL 565 PID Control...
Страница 110: ...Page 110 Accumass BW500 PL 565 Batching...
Страница 112: ...Page 112 Accumass BW500 PL 565 Certification...
Страница 140: ...Page 140 Accumass BW500 PL 565 Appendices...