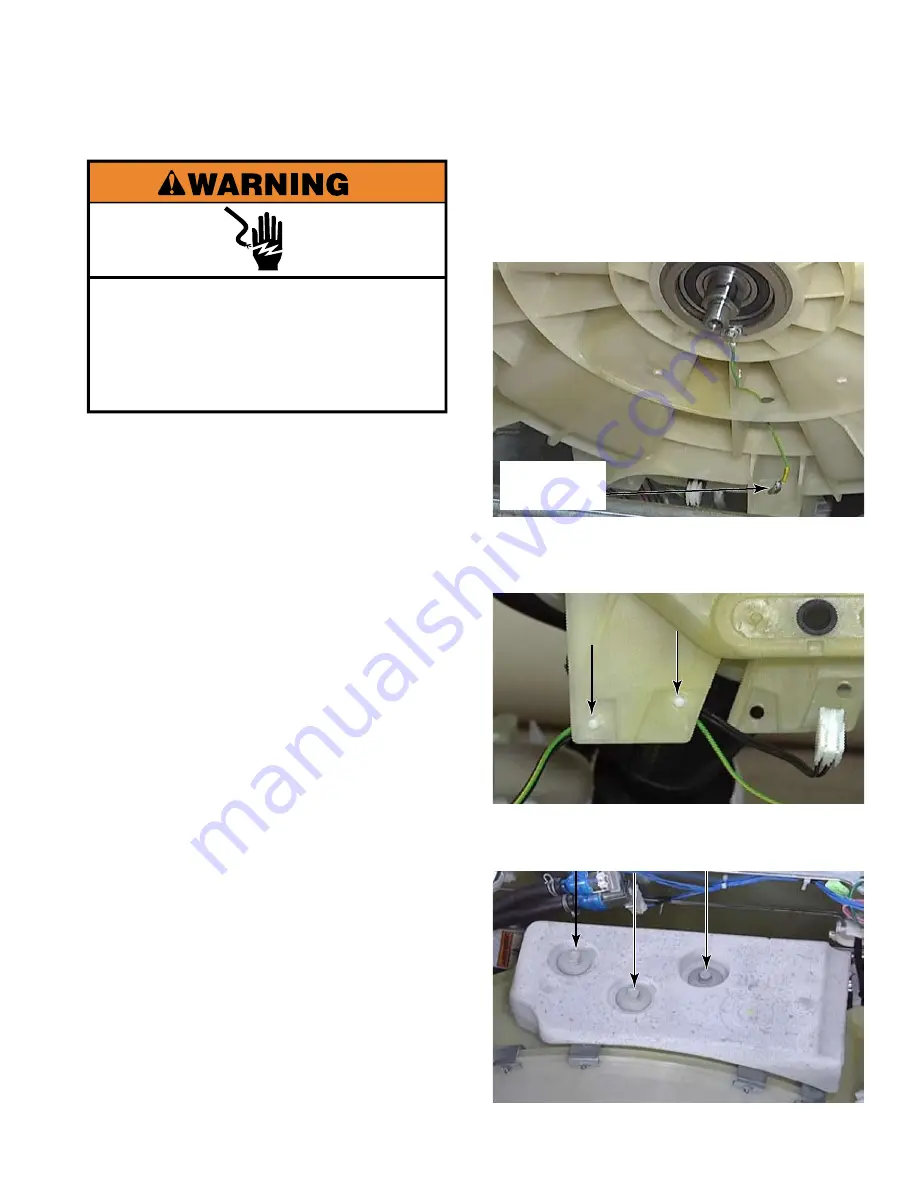
4-47
Disconnect the ground wire to the hub
at the spade connection about 12 inches
from the hub. Follow the ground wire from
the hub to the connector to locate the
disconnecting point.
Remove the wire retainers by pressing the
Christmas tree clips out of the holes in the
bottom of the outer tub.
Remove three 1/2” bolts that secure top
rear weight to outer tub, and remove weight.
12.
13.
14.
Electrical Shock Hazard
Disconnect power before servicing.
Replace all parts and panels before
operating.
Failure to do so can result in death or
electrical shock.
Unplug washer or disconnect power.
Turn off the water supply to the washer.
Remove the chemical dispenser assembly
(See page 4-14).
Remove the washer front support bracket
(See page 4-46).
Remove the bellow (See page 4-44).
Disconnect the tub to pump hose from
pump (See page 4-30).
Remove the rear panel (See page 4-36).
Remove the basket pulley (See page 4-38).
Disconnect the vent tube (See page 4-39).
Remove the wiring connector from the
temperature sensor (See page 4-40).
Remove the motor (See page 4-41).
1.
2.
3.
4.
5.
6.
7.
8.
9.
10.
11.
reMOve TuB anD SPin BaSkeT aSSeMBly
Ground Wire
Disconnect
Содержание MLE20PDAYW0
Страница 14: ...1 6 NOTES ...
Страница 21: ...2 7 Stacked Washer Gas Dryer Grounding ...
Страница 40: ...2 26 NOTES ...
Страница 56: ...3 16 NOTES ...
Страница 144: ...4 88 NOTES ...
Страница 198: ...6 32 NOTES ...
Страница 203: ...7 5 NOTES ...
Страница 204: ......