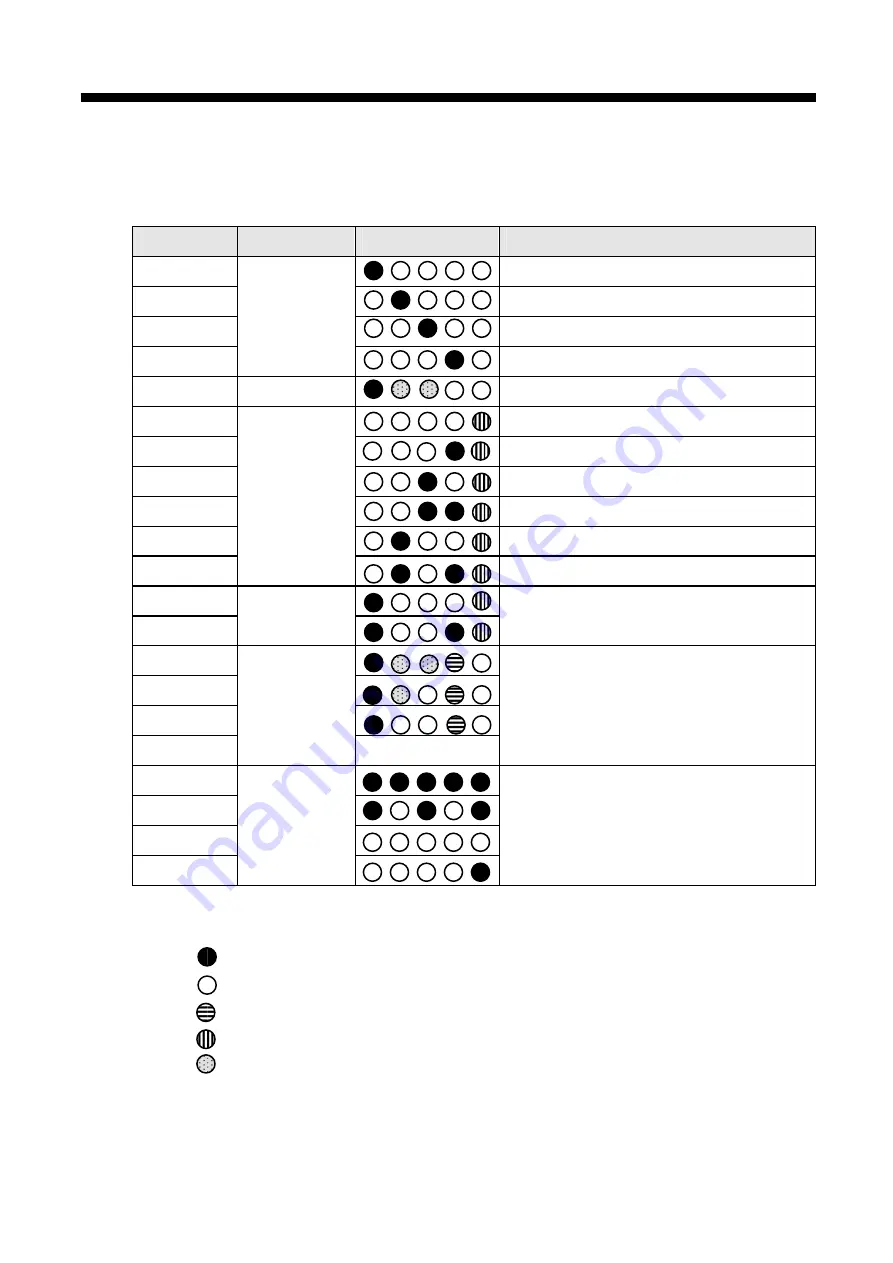
Chapter 7. Diagnosis Function
7-6
[Table 7.1.3] LED indication specification of slave group
Classification
Error type
LED status
Error contents
RSM_00
Checking inner memory 1 of module
RSM_01
Checking inner memory 2 of module
RSM_02
Checking
communication
RSM_03
Power on
Checking special module common RAM
RSM_04
Normal
Module communication is normal
RSM_05
Inner memory 1 error
RSM_06
Inner memory 2 error
RSM_07
Communication
error
RSM_08
Write/Read special module error
RSM_09
Write/Read I/O module error
RSM_10
Hardware error
Module equipment error, fuse error
RSM_11
RSM_12
System
operation error
System error during operation
RSM_13
RSM_14
RSM_15
RSM_16
Abnormal
①
Cable shout/open
②
Not suitable for cable length
③
Hardware error
④
Network configuration status error
RSM_17
RSM_18
RSM_19
RSM_20
Error that
can
’
t be
recovered
Hardware error of communication module
※
LED location is RUN, TOKEN, TX/RX, FAULT, SYS FAULT from left.
On
Off
Flicker with 1 second period
Non-periodical flicker or off
Non-periodical flicker
Содержание G0L-GWRA
Страница 115: ...Appendix A 14 A3 5 G0L GWRA Applied type G0L GWRA ...