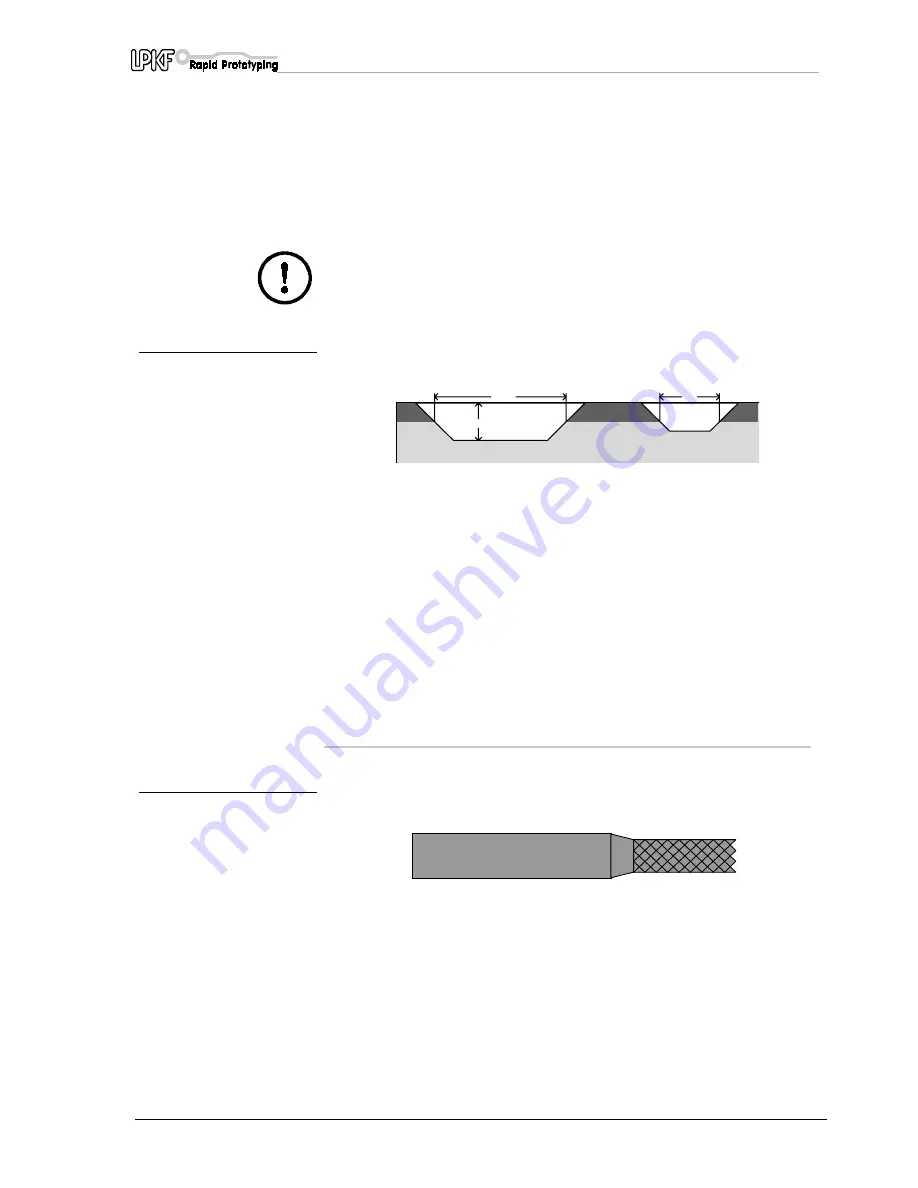
Procedures for milling and drilling
ProtoMat C30/C30-S
41
As a rule, the milling depth must be set as wide (deep) as possible. The
tool wears more quickly if only the extreme milling cutter tip (<0.2 mm
isolation) is used than with deeper milling.The LPKF micromilling cutters
can be used to create even finer isolation channels but their service life
will be only approximately 20% of that of the LPKF universal milling
cutters mentioned above.
Caution! Do not confuse micromilling cutters and universal milling
cutters. It is only possible to distinguish the two under a
microscope.
fig. 25: Milling passes using the
LPKF universal, and micro
cutters
See the section entitled “Practical tips” for more information.
The board must be cleaned after machining. This can be done either in a
brush machine or, alternatively, with a manual board cleaner (LPKF
accessories).
In either case, the board must be rinsed thoroughly with water to remove
any copper dust produced by brushing. After rinsing, the board must be
dried thoroughly (hair drier) and then protected against oxidation by a
soldering varnish.
10.7 Contour milling in base material
fig. 26: Contour milling cutters
The traverse speed has to be reduced for contour milling. This may differ
from material to material. Use only contour milling cutters (38 mm long)
designed specifically for this purpose: 1 or 2 mm diameter if possible.
The 1 mm contour milling cutter should only be used for internal cut-outs
(smaller internal radius). It breaks relatively easily so set the feed rate to
the minimum setting.
The 2 mm contour milling cutter is far more robust and is to be
recommended for milling external contours.
ca. 0.2mm
ca. 0.075mm
Cu
ca. 0.1mm
FR4
Содержание ProtoMat C 30-S
Страница 72: ...Index 72 ProtoMat C30 C30 S...