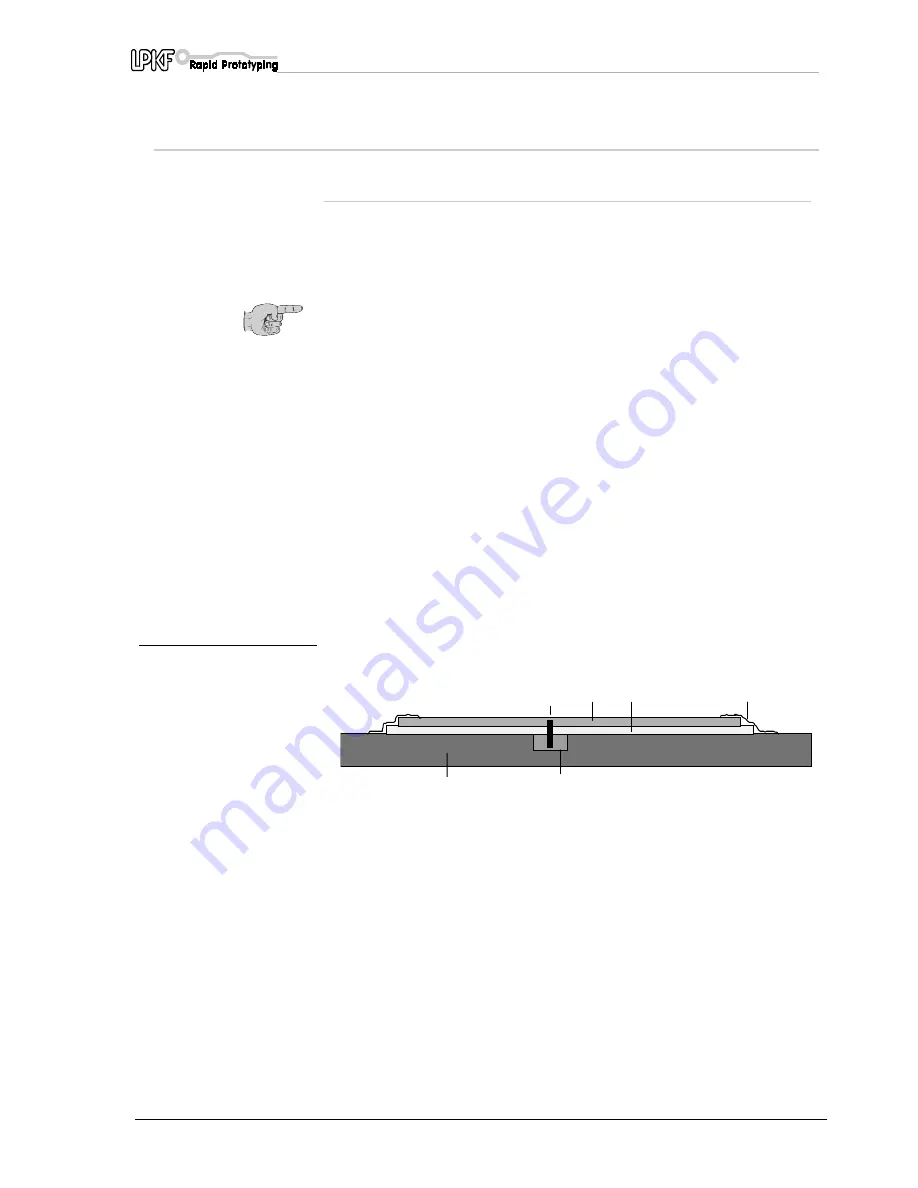
Procedures for milling and drilling
ProtoMat C30/C30-S
37
10.0 Procedures for milling and drilling
10.1 Securing the board
Make 3,0 mm or 3,05 mm diameter congruent registration holes in the
base material and drilling backing in the X axis.
This can also be done with any bench drill. Note that the diameter
decreases during galvanic through-hole plating.
Note: The drilling backing should be drilled to a larger diameter,
such as 5 mm to allow for inaccuracies in the registration holes.
› Move the plotter head to the Pause position.
› Insert alignment pins in the front and rear registration hole strips.
It is essential that you make sure the front registration hole strip in
the machine groove is pushed against the reference pin at the front.
› Position the drilled base material and drilling backing over the
alignment pins. The format of the base material should be selected
so that the registration hole strip does not need to be moved more
than 10 mm. Moving the registration hole strip more than 10 mm
reduces the accuracy of the registration hole system.
› Now additionally secure the base material in this position on all four
sides with adhesive tape (we recommend Tesakrepp 5250).
This prevent the corners of the board bending up.
fig. 20: Securing the board
The alignment pins hold the board in position. They also act as a
reference when double-sided base are rotated.
This is particularly important for contour milling.
It is important that no adhesive tape, drilling or milling swarf is left
between the individual layers to ensure that the base material lies
absolutely flat. Small particles under the base material have an adverse
affect on the uniformity of the milling depth.
1
- Machine bed (aluminium base plate)
4
- 2 mm thick drilling backing
2
- 3 mm diameter alignment pins
5
- Adhesive tape
3
- Base material approximately 1.6 mm thick
6
- Registration hole strip
1
2
3
4
5
6
Содержание ProtoMat C 30-S
Страница 72: ...Index 72 ProtoMat C30 C30 S...