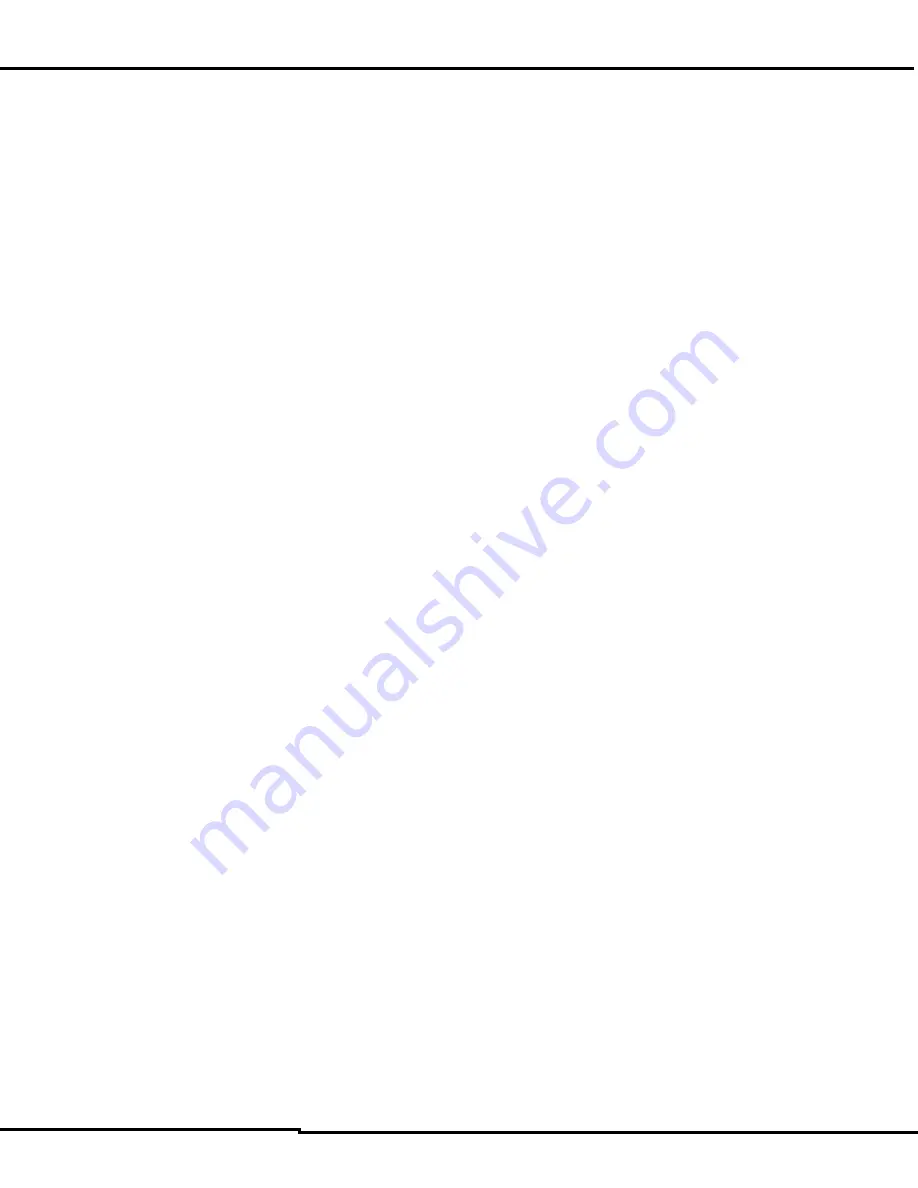
KNIGHT D-SERIES SERVO HOIST OPERATION MANUAL
SECTION 5
SOFTWARE
73
(Refer to Figure 5-51)
Row #3) The ‘TEST MODE ACCEL (IPS
2
)’ display shows the acceleration setpoint for the hoist while
in Test Mode.
The ‘TEST MODE DECEL (IPS
2
)’ display shows the deceleration setpoint for the hoist while
in Test Mode.
NOTE: The higher the number placed into the ‘ACCEL’ or ‘DECEL’ input text box,
the quicker the hoist will come to a stop. The lower the number, the more distance
the hoist will take to slow down so it will start slowing down sooner.
Row #4) The ‘TEST MODE DELAY (MS)’ value should equal or exceed the time it takes for the servo
to move from the upper limit to the lower limit during the test cycle. If using the settings on
the screen shown, the delay should be set to a minimum of 5000ms or a five second delay.
Row #5) The ‘TEST CYCLE COUNT TARGET’ display shows the number of test cycles the hoist will
perform. The hoist will automatically stop cycling when it reaches this number of cycles.
Row #6) The hoist’s test mode starting conditions are displayed here as indicators.
Row #7) The ‘START’ and ‘STOP’ buttons are used to begin and end the test cycle.
Row #8) The ‘TEST MODE INACTIVE’ indicator will change to ‘TEST MODE ACTIVE’ when the hoist
is moving in test mode.
Row #9) The current number of test mode cycles will be displayed here.
The progress bar will keep track of the cycle count.
The “RESET COUNTER” button will reset the number of test counts.
Button)
Press the ‘BACK TO INDEX’ button to return to the MOTION INDEX screen.