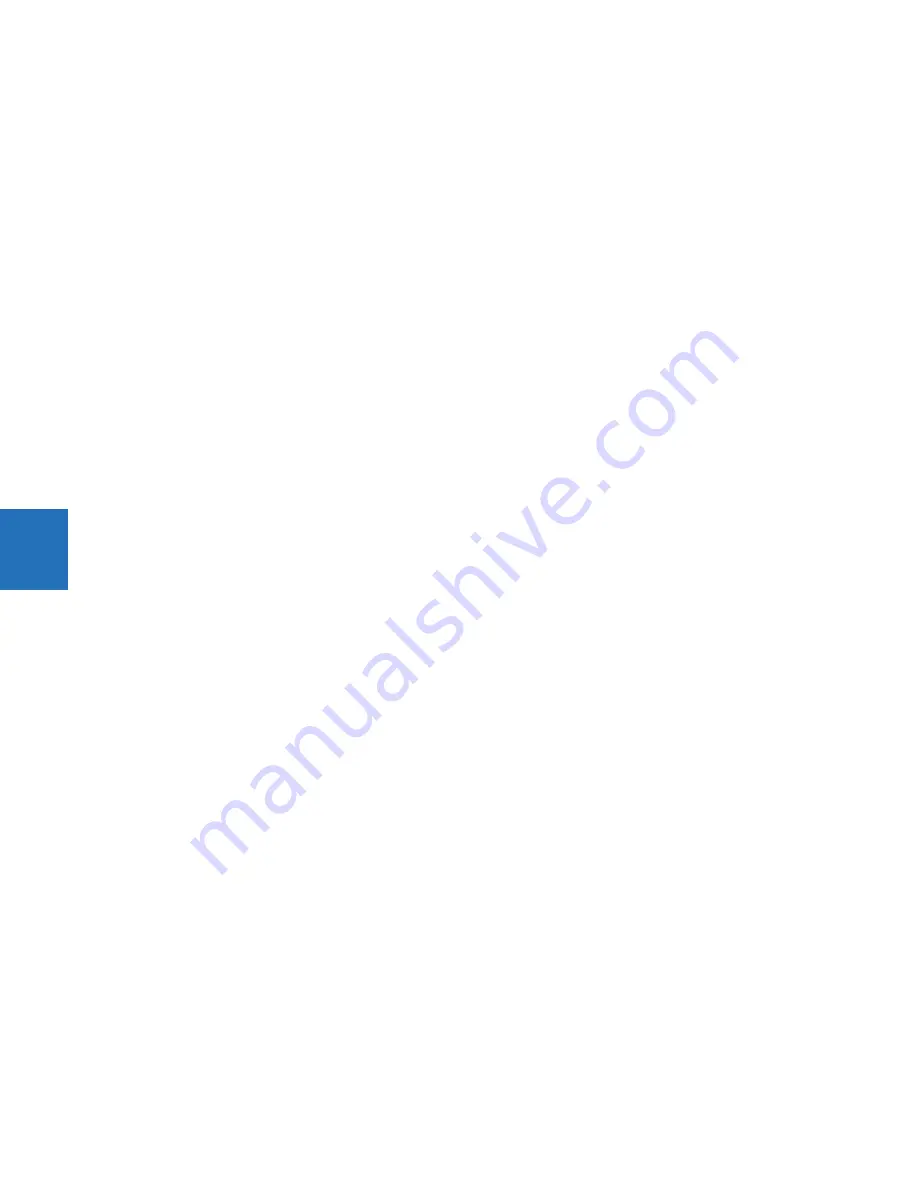
5-114
L60 LINE PHASE COMPARISON SYSTEM – INSTRUCTION MANUAL
PRODUCT SETUP
CHAPTER 5: SETTINGS
5
•
Line or feeder ID via the name of a configured signal source
•
Active setting group at the time of trigger
•
Pre-fault current and voltage phasors (two cycles before either a 50DD disturbance associated with fault report
source or the trigger operate). Once a disturbance is detected, pre-fault phasors hold for three seconds waiting for the
fault report trigger. If trigger does not occur within this time, the values are cleared to prepare for the next disturbance.
•
Fault current and voltage phasors (one cycle after the trigger)
•
Elements operated at the time of triggering
•
Events — Nine before trigger and seven after trigger (only available via the relay web page)
•
Fault duration times for each breaker (created by the breaker arcing current feature)
The captured data also includes the fault type, the distance to the fault location, distance to the fault location, fault loop
impedance, as well as the reclose shot number (when applicable). To include fault duration times in the fault report, enable
and configure the breaker arcing current feature for each of the breakers. Fault duration is reported on a per-phase basis.
The relay allows locating faults, including ground faults, from delta-connected VTs. In this case, the missing zero-sequence
voltage is substituted either by the externally provided neutral voltage (broken delta VT) connected to the auxiliary voltage
channel of a VT bank, or by the zero-sequence voltage approximated as a voltage drop developed by the zero-sequence
current, and user-provided zero-sequence equivalent impedance of the system behind the relay.
The trigger can be any FlexLogic operand, but in most applications it is expected to be the same operand, usually a virtual
output, that is used to drive an output relay to trip a breaker. To prevent the overwriting of fault events, do not use the
disturbance detector to trigger a fault report. A FAULT RPT TRIG event is automatically created when the report is triggered.
If a number of protection elements are ORed to create a fault report trigger, the first operation of any element causing the
OR gate output to become high triggers a fault report. However, If other elements operate during the fault and the first
operated element has not been reset (the OR gate output is still high), the fault report is not triggered again. Considering
the reset time of protection elements, there is very little chance that a fault report can be triggered twice in this manner. As
the fault report must capture a usable amount of pre and post-fault data, it cannot be triggered faster than every 20 ms.
Each fault report is stored as a file; the relay capacity is 15 files. A 16th trigger overwrites the oldest file.
Individual fault report features store their files in the same memory space. The sixteenth report overwrites the first one
regardless of which fault report feature produced the sixteenth and the first records.
The EnerVista software is required to view all captured data. The relay faceplate display can be used to view the date and
time of trigger, the fault type, the distance location of the fault, and the reclose shot number.
The
FAULT REPORT 1 SOURCE
setting selects the source for input currents and voltages and disturbance detection. For the
application of entirely parallel lines, the fault report can be programmed to apply compensation for the zero sequence
mutual coupling between parallel lines when calculating fault resistance and fault loop impedance. If this compensation is
required, the ground current (3I_0) from the parallel line must be connected to the ground input CT of the CT bank
configured under the
FAULT REPORT 1 SOURCE
with the same polarity as the phase current input configured in the same
source.
The
FAULT 1 REPORT TRIG
setting assigns the FlexLogic operand representing the protection element/elements requiring
operational fault location calculations. The distance to fault calculations are initiated by this signal. The
FAULT REPORT 1 Z1
MAG
,
FAULT REPORT 1 Z0 MAG
, and
FAULT REPORT 1 Z0M MAG
impedances are entered in secondary ohms.
For the application of entirely parallel lines, Z0M MAG/ANG is the mutual zero-sequence impedance for the whole line,
required to compensate the calculation of fault resistance and fault loop impedance.
The
FAULT REPORT 1 VT SUBSTITUTION
setting is set to “None” if the relay is fed from wye-connected VTs. If delta-connected
VTs are used, and the relay is supplied with the neutral (3V0) voltage, this setting is set to “V0”. The method is still exact, as
the fault locator combines the line-to-line voltage measurements with the neutral voltage measurement to re-create the
line-to-ground voltages. See the
ACTUAL VALUES
RECORDS
FAULT REPORTS
menu for details. It is required to configure
the delta and neutral voltages under the source indicated as input for the fault report. Also, the relay checks if the auxiliary
signal configured is marked as “Vn” by the user (under VT setup) and inhibits the fault location if the auxiliary signal is
labeled differently.
Содержание L60
Страница 10: ...x L60 LINE PHASE COMPARISON SYSTEM INSTRUCTION MANUAL TABLE OF CONTENTS ...
Страница 14: ...1 4 L60 LINE PHASE COMPARISON SYSTEM INSTRUCTION MANUAL FOR FURTHER ASSISTANCE CHAPTER 1 INTRODUCTION 1 ...
Страница 122: ...3 72 L60 LINE PHASE COMPARISON SYSTEM INSTRUCTION MANUAL CONNECT TO D400 GATEWAY CHAPTER 3 INSTALLATION 3 ...
Страница 590: ...5 382 L60 LINE PHASE COMPARISON SYSTEM INSTRUCTION MANUAL TESTING CHAPTER 5 SETTINGS 5 ...
Страница 632: ...7 12 L60 LINE PHASE COMPARISON SYSTEM INSTRUCTION MANUAL TARGETS MENU CHAPTER 7 COMMANDS AND TARGETS 7 ...
Страница 736: ...A 14 L60 LINE PHASE COMPARISON SYSTEM INSTRUCTION MANUAL FLEXANALOG ITEMS APPENDIX A FLEXANALOG OPERANDS A ...
Страница 744: ...C 6 L60 LINE PHASE COMPARISON SYSTEM INSTRUCTION MANUAL COMMAND LINE INTERFACE APPENDIX C COMMAND LINE INTERFACE C ...
Страница 752: ...iv L60 LINE PHASE COMPARISON SYSTEM INSTRUCTION MANUAL ABBREVIATIONS ...