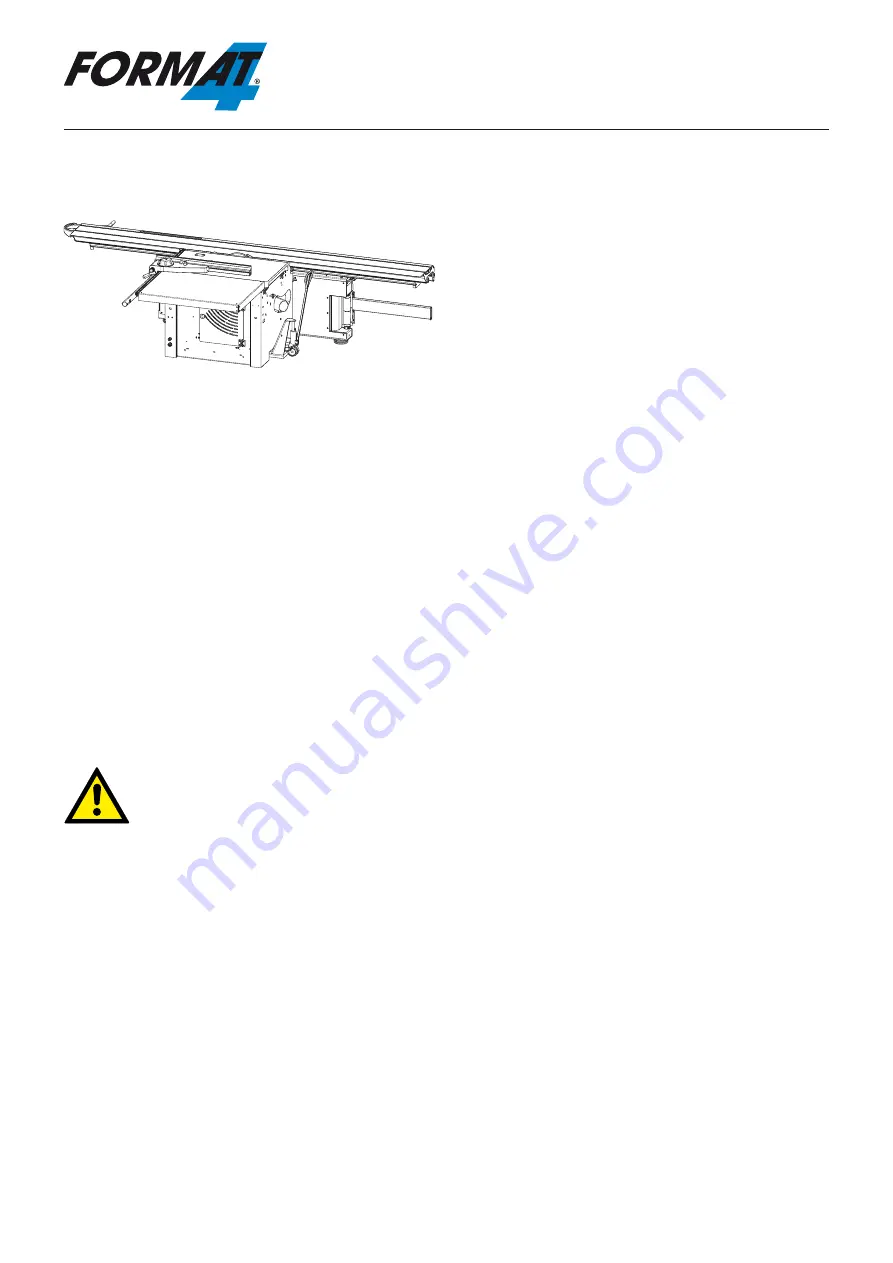
Panel Saw
Kappa 30 / kappa 40
6.2.4.2 Transporting the machine
Fig. 26: Transport with a pallet jack
Push the pallet jack forks into the holes of the machine
frame.
6.3 Transport inspection
Upon arrival, inspect the shipment to ensure that it is
complete and has not suffered any damage.
If any transport damage is visible, do not accept the de-
livery or accept it only with reservation. Record the scope
of the damage on the transport documents/delivery note.
Initiate the complaint process.
For all defects that are not discovered upon delivery, be
sure to report them as soon as they are recognized be-
cause claims for damages must be filed within a certain
period, as granted by law.
6.4 Packaging
If no agreement has been made with the supplier to take
back the packaging materials, help to protect the envi-
ronment by reusing the materials or separating them ac-
cording to type and size for recycling.
Attention! Dispose of the packaging materials in an environmentally friendly way and always in accord-
ance with local waste disposal regulations. If applicable, contract a recycling firm to dispose of the pack-
aging materials.
Attention: Help preserve the environment! Packaging materials are valuable raw materials and in many
cases they can be used again or expediently reprocessed or recycled.
Transport, packaging and storage
32
Содержание kappa 30
Страница 93: ......