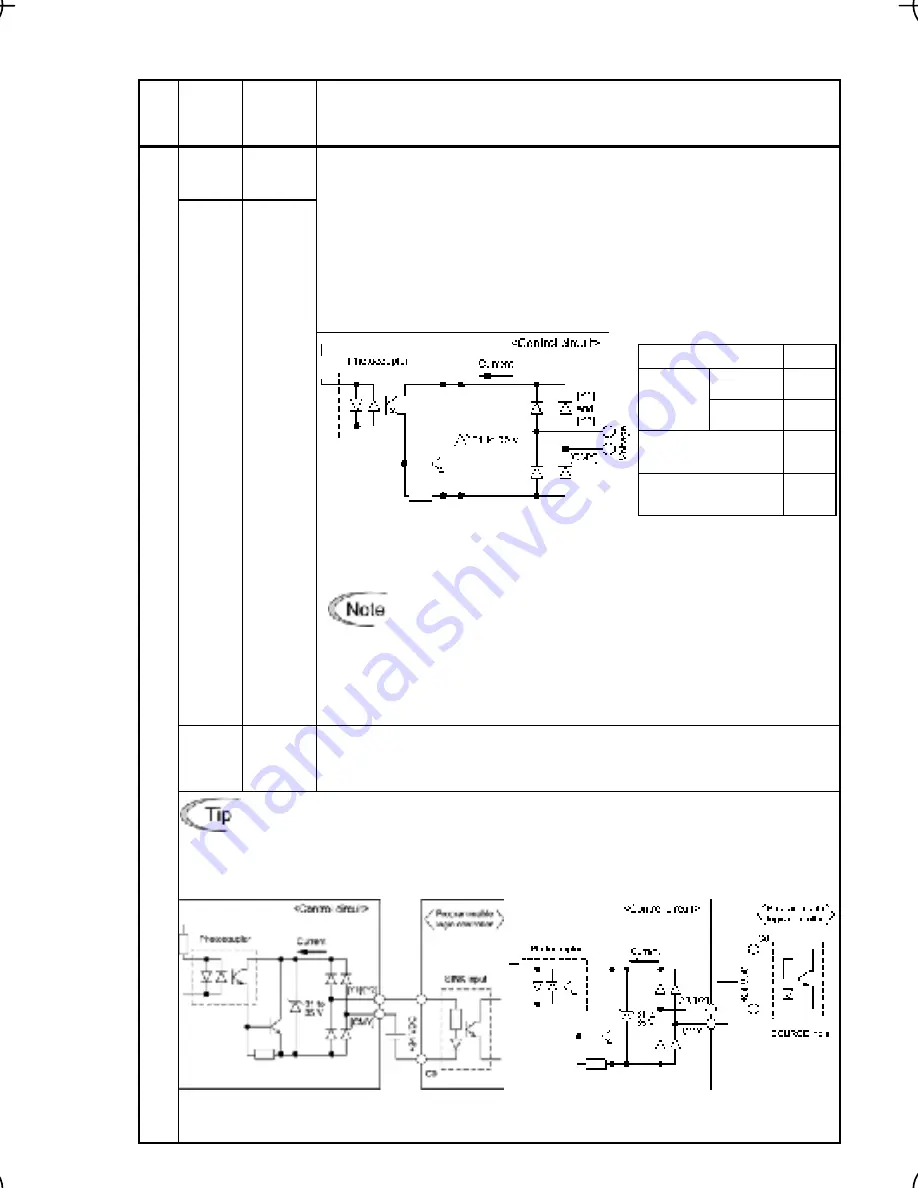
2-20
Table 2.9 Continued
Classifi- cation
Sym
bol
Name Functions
[Y1]
Transistor
output 1
(1) Various signals such as inverter running, speed/freq. arrival and
overload early warning can be assigned to any terminals, [Y1] and [Y2]
by setting function code E20 and E21. Refer to Chapter 5, Section 5.2
"Overview of Function Codes" for details.
(2) Switches the logic value (1/0) for ON/OFF of the terminals between [Y1],
[Y2], and [CMY]. If the logic value for ON between [Y1], [Y2], and [CMY]
is 1 in the normal logic system, for example, OFF is 1 in the negative
logic system and vice versa.
(Transistor output circuit specification)
Figure 2.18 Transistor Output Circuit
Item Max.
ON level
3 V
Operation
voltage
OFF level 27 V
Maximum motor
current at ON
50 mA
Leakage current
at OFF
0.1 mA
Figure 2.19 shows examples of connection between the control circuit and a
PLC.
[Y2]
Transistor
output 2
• When a transistor output drives a control relay, connect a
surge-absorbing diode across relay’s coil terminals.
• When any equipment or device connected to the transistor
output needs to be supplied with DC power, feed the power
(+24 VDC: allowable range: +22 to +27 VDC, 50 mA max.)
through the [PLC] terminal. Short-circuit between the
terminals [CMY] and [CM] in this case.
[CMY] Transistor
output
common
Common terminal for transistor output signal terminals
This terminal is electrically isolated from terminals, [CM]s and [11]s.
Connecting Programmable Logic Controller (PLC) to Terminal [Y1] or [Y2]
Figure 2.19 shows two examples of circuit connection between the transistor output of the
inverter’s control circuit and a PLC. In example (a), the input circuit of the PLC serves as a
SINK for the control circuit output, whereas in example (b), it serves as a SOURCE for the
output.
(a) PLC serving as SINK
(b) PLC serving as SOURCE
T
ransistor
outp
ut
Figure 2.19 Connecting PLC to Control Circuit