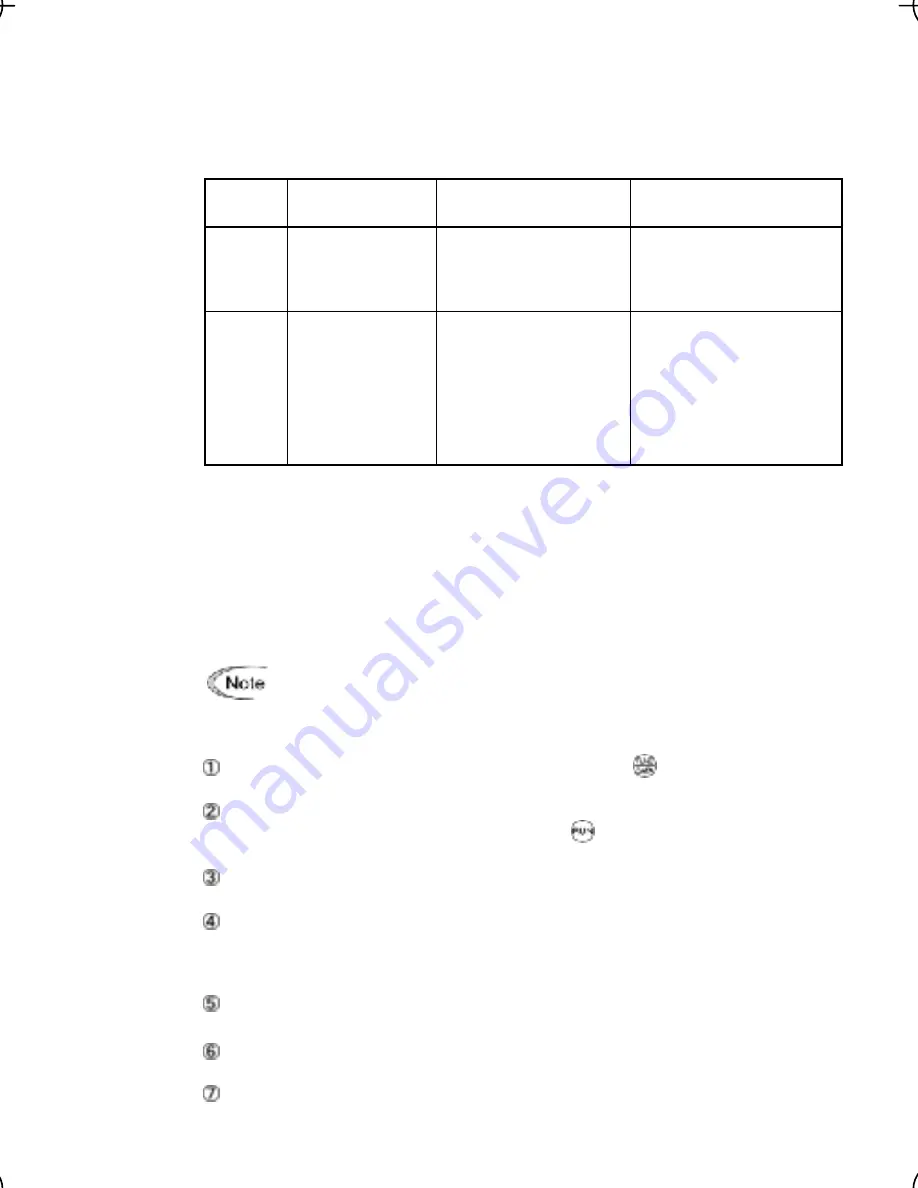
4-3
2) Selection of tuning process
Check the situation of the machine system and choose between "Tuning while the motor is
stopped (P04 or A18 = 1)" and "Tuning while the motor is running (P04 or A18 = 2)." In the
case of "Tuning while the motor is running (P04 or A18 = 2)," also adjust the acceleration
and deceleration times (F07 and F08) and set the rotation direction properly so that it
matches the actual rotation direction of the machine system.
Data for
P04, A18
Motor parameters
subject to tuning:
Action
Choose the process when:
1
Primary resistance
(%R1)
Leakage reactance
(%X)
Measure %R1 and %X
while the motor is stopped.
The motor cannot be rotated,
or more than 50% of the rated
load would be applied on the
motor if rotated.
2
Primary resistance
(%R1)
Leakage reactance
(%X)
No-load current
Rated slip frequency
Measure %R1 and %X
while the motor is stopped,
later no-load current while
the motor is running. (At
50% of the base frequency)
Lastly, measure rated slip
frequency while the motor
is stopped.
Even if the motor is rotated, it
is safe and the load applied
on the motor would be no
more than 50% of the rating.
(If you do the tuning with no
load, you will get the highest
precision.)
Upon completion of the tuning, each motor parameter will be automatically saved into the
applicable function code.
3) Preparation of machine system
Perform appropriate preparations on the motor and its load, such as disengaging the
coupling and deactivating the safety device.
Switch to the motor 1 or motor 2, which the tuning is to be performed on.
Tuning results by P04 will be applies to P codes for the motor 1, and the tuning results by
A18 will be applies to A codes for the motor 2.
Assigning the command "Switch to motor 2
SWM2
"
to any of the terminal [Y1],
[Y2], or [30A/B/C] will automatically switch the output status of
SWM2
depending
on the motor selected for the tuning.
4) Perform tuning
Set function code P04 or A18 to "1" or "2" and press the
key. (The blinking of
1
or
2
on the LED monitor will slow down.)
Enter a run command for the rotation direction you have chosen. The factory default
setting is "forward rotation upon pressing the
key on the keypad." To switch to
reverse rotation, change the setting of function code F02.
The display of
1
or
2
stays lit, and tuning takes place while the motor is stopped.
(Maximum tuning time: approximately 40 (s).)
If the function code P04 or A18 = 2, the motor is accelerated to approximately 50% of
the base frequency and then tuning takes place. Upon completion of measurements,
the motor will decelerate and stop.
(Estimated tuning time: Acceleration time + 20 (s) + Deceleration time)
Tuning will continue after the motor is stopped.
(Maximum tuning time: approximately 10 (s).)
If the terminal signal
FWD
or
REV
is selected as the run command (F02 = 1),
end
will appear upon completion of the measurements.
The run command is turned OFF and the tuning completes, with the next function code
p05
or
a20
displayed on the keypad (the run command given through the keypad or
the communications link is automatically turned OFF).