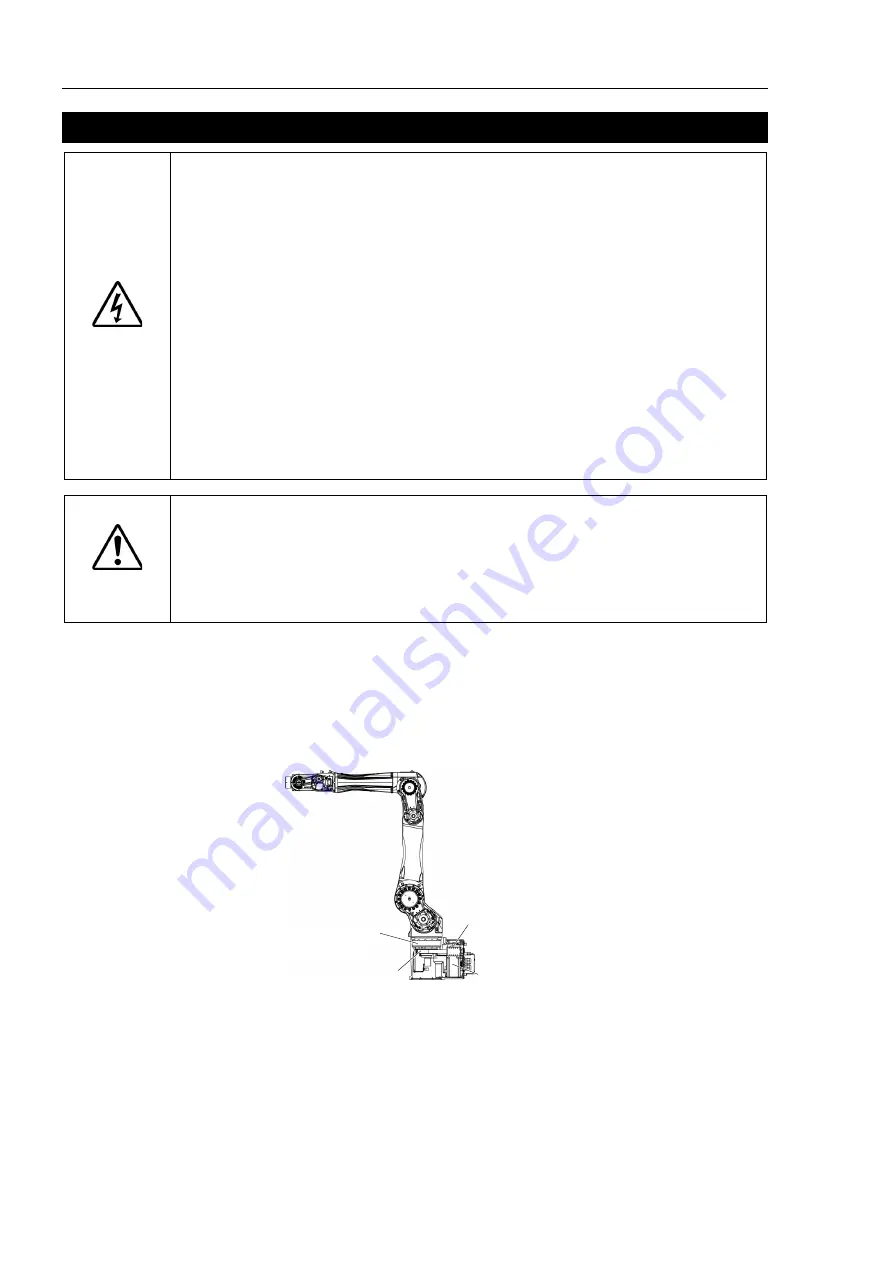
Maintenance 5. Joint #1
176
C8 Rev.13
5. Joint #1
WARNING
■
Before performing any replacement procedure, turn OFF the Controller and
related equipment, and then disconnect the power plug from the power source.
Performing any replacement procedure with the power ON is extremely hazardous
and may result in electric shock and/or malfunction of the robot system.
■
Do not connect or disconnect the motor connectors while the power to the robot
system is turned ON. Connecting or disconnecting the motor connectors with the
power ON is extremely hazardous and may result in serious bodily injury as the
Manipulator may move abnormally, and also may result in electric shock and/or
malfunction of the robot system.
■
Be sure to connect the AC power cable to a power receptacle. DO NOT connect
it directly to a factory power source. To shut off power to the robot system,
disconnect the power plug from the power source. Performing any work while
connecting the AC power cable to a factory power source is extremely hazardous
and may result in electric shock and/or malfunction of the robot system.
CAUTION
■
Be careful not to apply excessive shock to the motor shaft during replacement
procedures. The shock may shorten the life of the motors and encoder and/or
damage them.
■
Never disassemble the motor and encoder. Disassembled motor and encoder
will cause a positional gap and cannot be used again.
After parts have been replaced (motors, reduction gear units, timing belts, etc.), the
Manipulator cannot perform positioning properly because a gap exists between the origin
stored in each motor encoder and its corresponding origin stored in the Controller.
After replacing the parts, it is necessary to match these origins.
The process of aligning the two origins is called “Calibration”.
Refer to
Maintenance 16. Calibration
and follow the steps to perform calibration.
Joint #1 Electromagnetic brake
Joint #1 Motor
Joint #1 Timing belt
Joint #1 Reduction gear unit
(Figure: C8-A1401* (C8XL))
Maintenance procedures differ depending on the installation type of the M/C cable.
5.1 M/C Cable Backward (Joint #1)
5.2 M/C Cable Downward (Joint #1)
Содержание C8 Series
Страница 1: ...Rev 13 EM208R4413F 6 Axis Robots C8 series MANIPULATOR MANUAL ...
Страница 2: ...Manipulator manual C8 series Rev 13 ...
Страница 8: ...vi C8 Rev 13 ...
Страница 14: ...Table of Contents xii C8 Rev 13 ...
Страница 16: ......
Страница 31: ...Setup Operation 2 Specifications C8 Rev 13 17 2 4 Outer Dimensions Unit mm 2 4 1 C8 A701 C8 ...
Страница 32: ...Setup Operation 2 Specifications 18 C8 Rev 13 2 4 2 C8 A901 C8L ...
Страница 33: ...Setup Operation 2 Specifications C8 Rev 13 19 2 4 3 C8 A1401 C8XL ...
Страница 49: ...Setup Operation 3 Environment and Installation C8 Rev 13 35 C8 A901 C8L ...
Страница 97: ...Maintenance This volume contains maintenance procedures with safety precautions for C8 series Manipulators ...
Страница 98: ......
Страница 183: ...Maintenance 4 Cable Unit C8 Rev 13 169 4 2 Connector Pin Assignment 4 2 1 Signal Cable ...
Страница 184: ...Maintenance 4 Cable Unit 170 C8 Rev 13 ...
Страница 185: ...Maintenance 4 Cable Unit C8 Rev 13 171 ...
Страница 186: ...Maintenance 4 Cable Unit 172 C8 Rev 13 4 2 2 Power Cable C8 A701 C8 C8 A901 C8L ...
Страница 187: ...Maintenance 4 Cable Unit C8 Rev 13 173 C8 A1401 C8XL ...
Страница 188: ...Maintenance 4 Cable Unit 174 C8 Rev 13 C8 A701 C8 C8 A901 C8L C8 A1401 C8XL ...