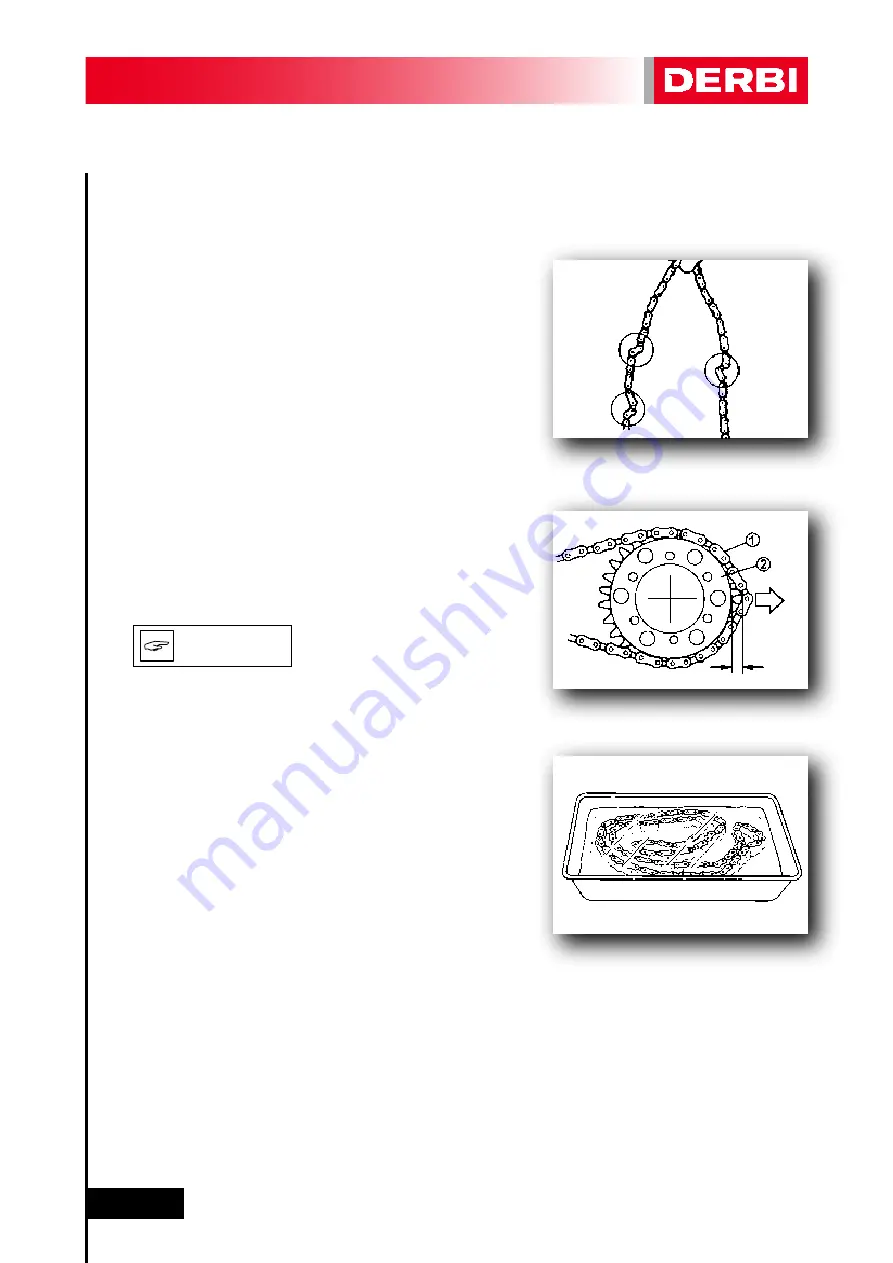
3 - MAINTENANCE
53
TRANSMISSION CHAIN
1. Inspect:
- The chain for rigidity.
Rigidity => Clean and lubricate or renew.
2. Inspect:
- Transmission chain(1).
- Rear sprocket (2).
- Sprocket.
More than ½ tooth of wear => Renew the chain.
IT IS RECOMMENDED TO RENEW
THE COMPLETE TRANSMISSION
KIT AND NOT JUST THE CHAIN.
3. Clean:
- The transmission chain.
- Place the chain in a container with petrol, and brush it to
remove as much of the dirt as possible.
- Then dry and lubricate it.
Lubricant for the transmission chain:
Spray grease for chains.
N.B.
Содержание GPR 125 Racing
Страница 1: ...WORKSHOP MANUAL GPR 125 4 stroke ...
Страница 30: ...2 PDI Pre delivery inspection 30 2 PDI Pre delivery inspection PDI Pre delivery inspection 31 2 1 ...
Страница 169: ...6 COOLING SYSTEM 169 6 1 DIAGRAM OF THE SYSTEM ...
Страница 170: ...6 COOLING SYSTEM 170 ...
Страница 179: ...7 LUBRICATION SYSTEM 179 7 1 DIAGRAM OF THE SYSTEM ...
Страница 180: ...7 LUBRICATION SYSTEM 180 ...
Страница 192: ...8 CHASSIS 192 FITTING FRONT SUSPENSION ...
Страница 202: ...9 BRAKING SYSTEM 202 9 BRAKING SYSTEM FRONT BRAKE REAR BRAKE 203 211 9 1 9 2 ...
Страница 247: ...Rev 0 2009 ...