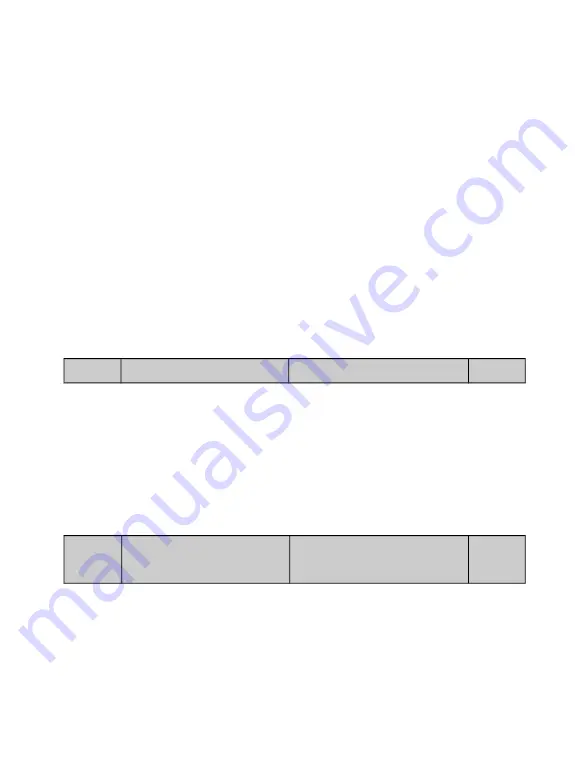
203
proportional gain and integral time of the speed regulator.
To achieve a faster system response, increase the proportional gain and reduce the integral
time. Be aware that this may lead to system oscillation.
The recommended adjustment method is as follows:
If the factory setting cannot meet the requirements, make proper adjustment. Increase the
proportional gain first to ensure that the system does not oscillate, and then reduce the
integral time to ensure that the system has quick response and small overshoot.
NOTE:
Improper PI parameter setting may cause too large speed
overshoot, and overvoltage fault may even occur when the
overshoot drops.
P9.07
Vector control slip gain
Setting Range: 50%
~
200%
100%
For SFVC, it is used to adjust speed stability accuracy of the motor. When the motor with
load runs at a very low speed, increase the value of this parameter; when the motor with
load runs at a very large speed, decrease the value of this parameter.
For CLVC, it is used to adjust the output current of the AC drive
with same load.
P9.08
Time constant of speed
loop filter
Setting Range: 0.000s
~
0.100s
0.000s
In the vector control mode, the output of the speed loop regulator is torque current
reference. This parameter is used to filter the torque references. It need not be adjusted
generally and can be increased in the case of large speed fluctuation. In the case of motor
oscillation, decrease the value of this parameter properly.
Содержание DGI900
Страница 1: ...User Manual DGI900 ...
Страница 181: ...181 ...