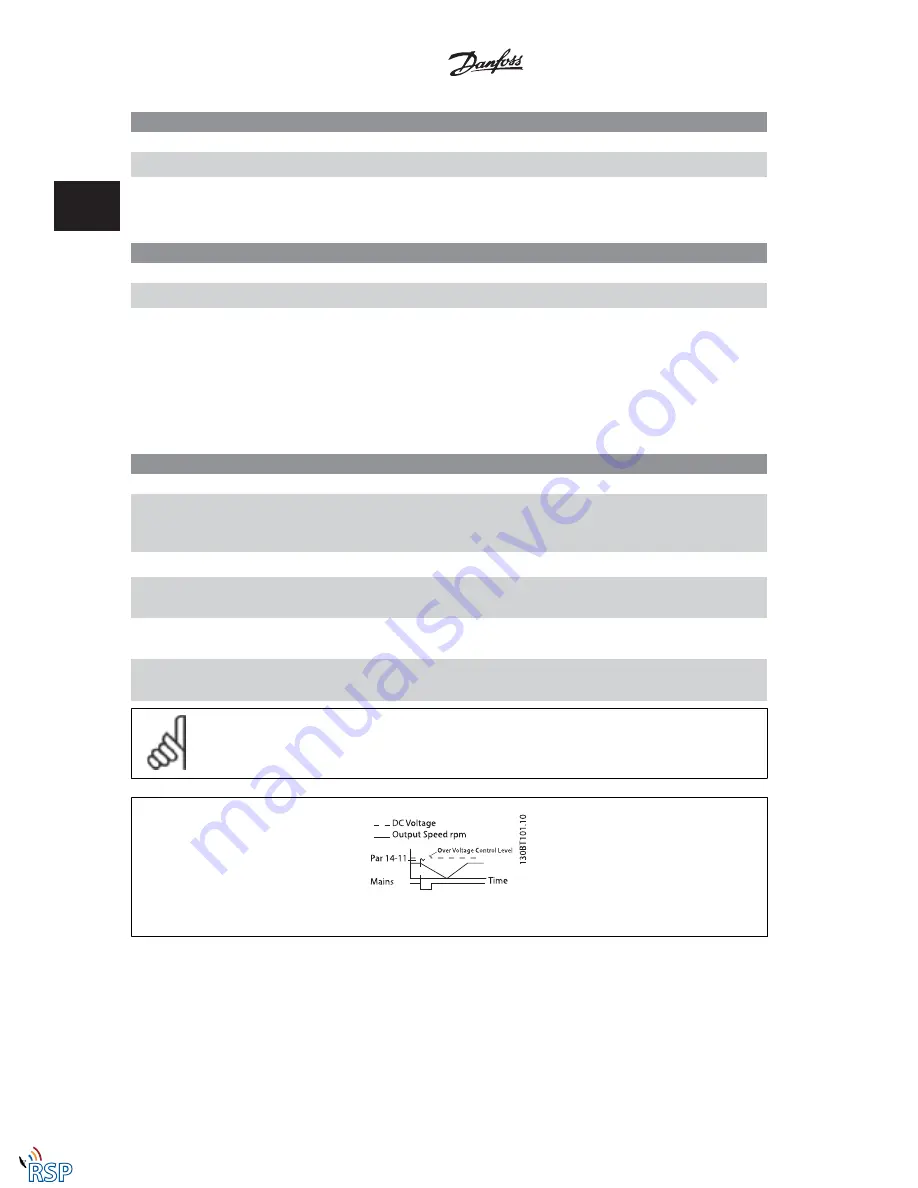
14-03 Overmodulation
Option:
Function:
[0]
Off
Selects no over-modulation of the output voltage in order to avoid torque ripple on the motor shaft.
[1] *
On
The over-modulation function generates an extra voltage of up-to 8% of U
max
output voltage without
over-modulation, which results in an extra torque of 10-12% in the middle of the over-syncronous
range (from 0% at nominal speed rising to approximately 12% at double nominal speed).
14-04 PWM Random
Option:
Function:
[0] *
Off
No change of the acoustic motor switching noise.
[1]
On
Transforms the acoustic motor switching noise from a clear ringing tone to a less noticeable ‘white’
noise. This is achieved by slightly and randomly altering the synchronism of the pulse width modu-
lated output phases.
2.13.3 14-1* Mains On/Off
Parameters for configuring mains failure monitoring and handling.
14-10 Mains Failure
Option:
Function:
Select the function at which the frequency converter must act, when the threshold set in
par. 14-11
Mains Voltage at Mains Fault
has been reached or a
Mains Failure Inverse
command is
activated via one of the digital inputs (par. 5-1*).
[0] *
No function
The energy left in the capacitor bank will be used to "drive" the motor, but will be discharged.
[1]
Ctrl. ramp-down
The frequency converter will perform a controlled ramp-down. par. 2-10
Brake Function
must be
set to
Off
[0].
[3]
Coasting
The inverter will turn off and the capacitor bank will back up the control card then ensuring a faster
restart when mains reconnected (at short power zags).
[4]
Kinetic back-up
The frequency converter will ride through by controlling speed for generative operation of the motor
utilizing the moment of inertia of the system as long as sufficient energy is present.
NB!
For best performance of controlled ramp-down and kinetic back-up par. 1-03
Torque Characteristics
should be set to
Compressor
[0]
or
Variable Torque
[1] (no automatic energy optimization should be active).
Illustration 2.2: Controlled Ramp-down - short mains failure. Ramping down to stop followed by ramping up to reference.
2 Parameter Description
VLT
p
Automation VT Drive FC322
Programming Guide
158
MG.20.W1.22 - VLT
p
is a registered Danfoss trademark
2
Remote Site Products - 1-888-532-2706 - www.remotesiteproducts.com
http://www.remotesiteproducts.com/p-20772-Danfoss-131X8135-VLT-Automation-VT-Drive-VFD-FC322-230V-5-HP.aspx