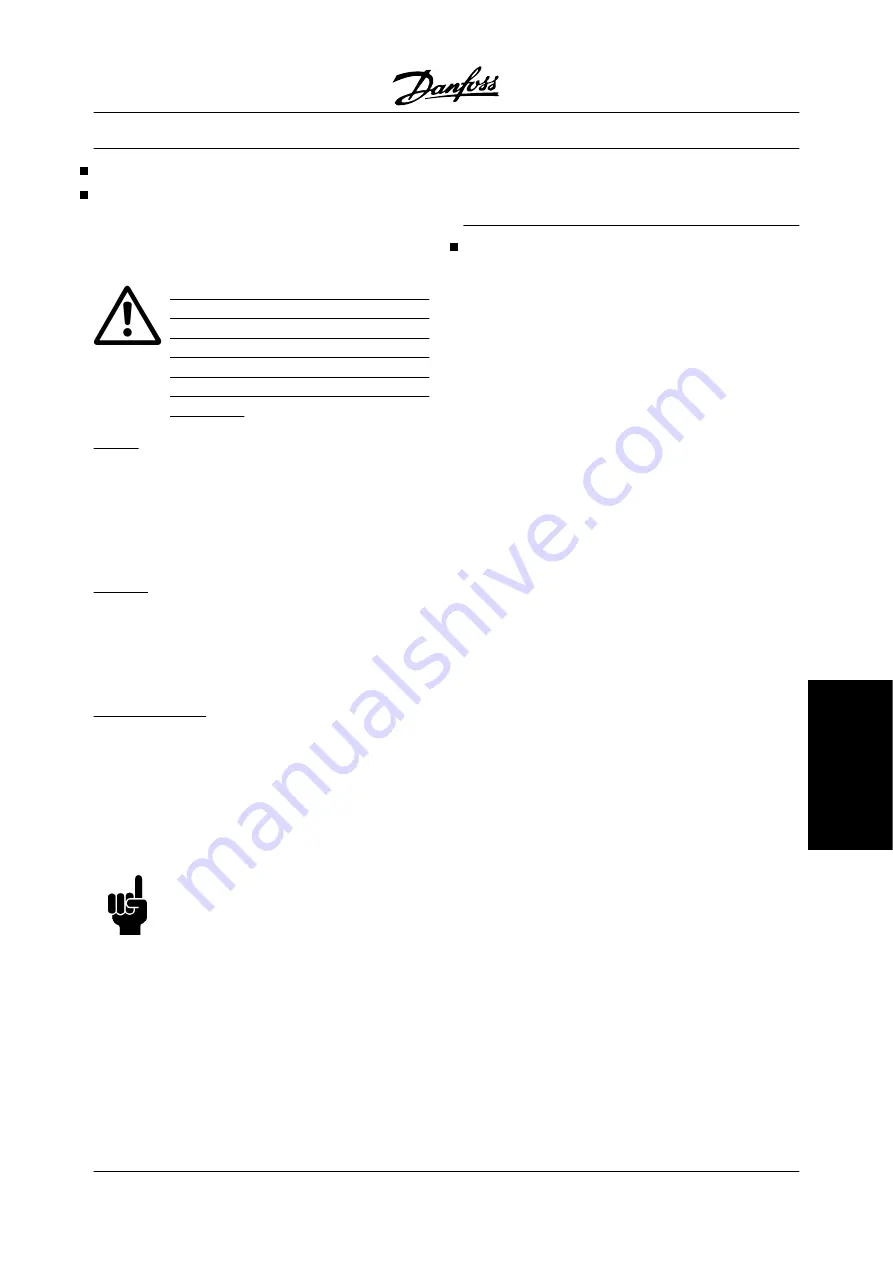
Special conditions
Extreme environments
An adjustable frequency drive contains a number of
mechanical and electronic components which are vul-
nerable to environmental impact.
Do not install the adjustable frequency
drive in environments where liquids, par-
ticles or gases in the air would damage the
electronics of the drive. Take all necessa-
ry measures to protect the drive. There is
a risk of fault trips and reduced service life
of the drive.
Liquids carried through the air can condense in the
adjustable frequency drive. Liquids may facilitate gal-
vanic corrosion of components and metal parts.
Steam, oil and brine may also cause corrosion of com-
ponents and metal parts. In these areas, it is recom-
mended to install units in cabinets. As a minimum,
cabinets should meet NEMA 12.
Particles in the air, such as dust, may lead to mechan-
ical, electrical and thermal faults in the adjustable fre-
quency drive. A typical indicator of too many particles
in the air is dust around the fan. In very dusty areas,
mounting the drive in a cabinet is recommended. As a
minimum, cabinets should meet NEMA 12.
Aggressive gases, such as sulfur, nitrogen and chlor-
ine compounds, together with high humidity and tem-
perature, facilitate possible chemical processes on the
components of the adjustable frequency drive. These
chemical processes quickly damage the electronics. In
these areas, mounting in a cabinet with fresh-air cir-
culation is recommended, thereby ensuring that ag-
gressive gases are kept away from the drive.
NOTE
Installation of adjustable frequency drives
in extreme environments increases the
risk of down-time, and considerable re-
duction of the service life of the drive.
Before the adjustable frequency drive is installed,
check whether there are liquids, particles or gases in
the air. Examine existing installations in the same en-
vironment. Typical indicators of harmful airborne liq-
uids are water or oil on metal parts or corrosion. Too
many dust particles are typically observed on top of
cabinets. Indication of aggressive gases in the air are
black copper rails and cable ends on existing electrical
installations.
Galvanic Isolation (PELV)
PELV (Protective Extra Low Voltage) insulation is ach-
ieved by inserting galvanic isolators between the con-
trol circuits and circuits that are connected to the line
power potential. The VLT is designed to meet the re-
quirements for protective separation by means of hav-
ing the necessary creepage and clearance distances.
These requirements are described in standard EN 50
178. It is also a requirement that the installation is car-
ried out in accordance with local/national regulations
regarding PELV.
All control terminals, terminals for serial communica-
tion and relay terminals are safely separated from the
line power potential, which is to say that they comply
with the PELV requirements. Circuits that are connec-
ted to control terminals 12, 18, 19, 20, 27, 29, 33, 42,
46, 50, 53, 55 and 60 are galvanically connected to
one another. Serial communication connected to serial
communication bus is galvanically insulated from the
control terminals, although this is only a functional in-
sulation.
The relay contacts on terminals 1-3 are insulated from
the other control circuits with reinforced/double isola-
tion, i.e., PELV is observed for these, even though
there is line power potential at the relay terminals.
The circuit elements described below form the safe
electric separation. They fulfill the requirements for re-
inforced/double insulation and associated testing pur-
suant to EN 50 178.
1.
Transformer and optical separation in voltage
supply.
2.
Optical insulation between the basic motor
control and the control card.
3.
Insulation between the control card and the
power part.
4.
Relay contacts and terminals relating to other
circuits on the control card.
PELV insulation of the control card is guaranteed un-
der the following conditions:
-
TT network with maximum 300 Vrms be-
tween phase and ground.
VLT
®
2800 Series
MG.27.A2.22 - VLT
®
is a registered Danfoss trademark
103
All a
bou
t
VLT 2
800