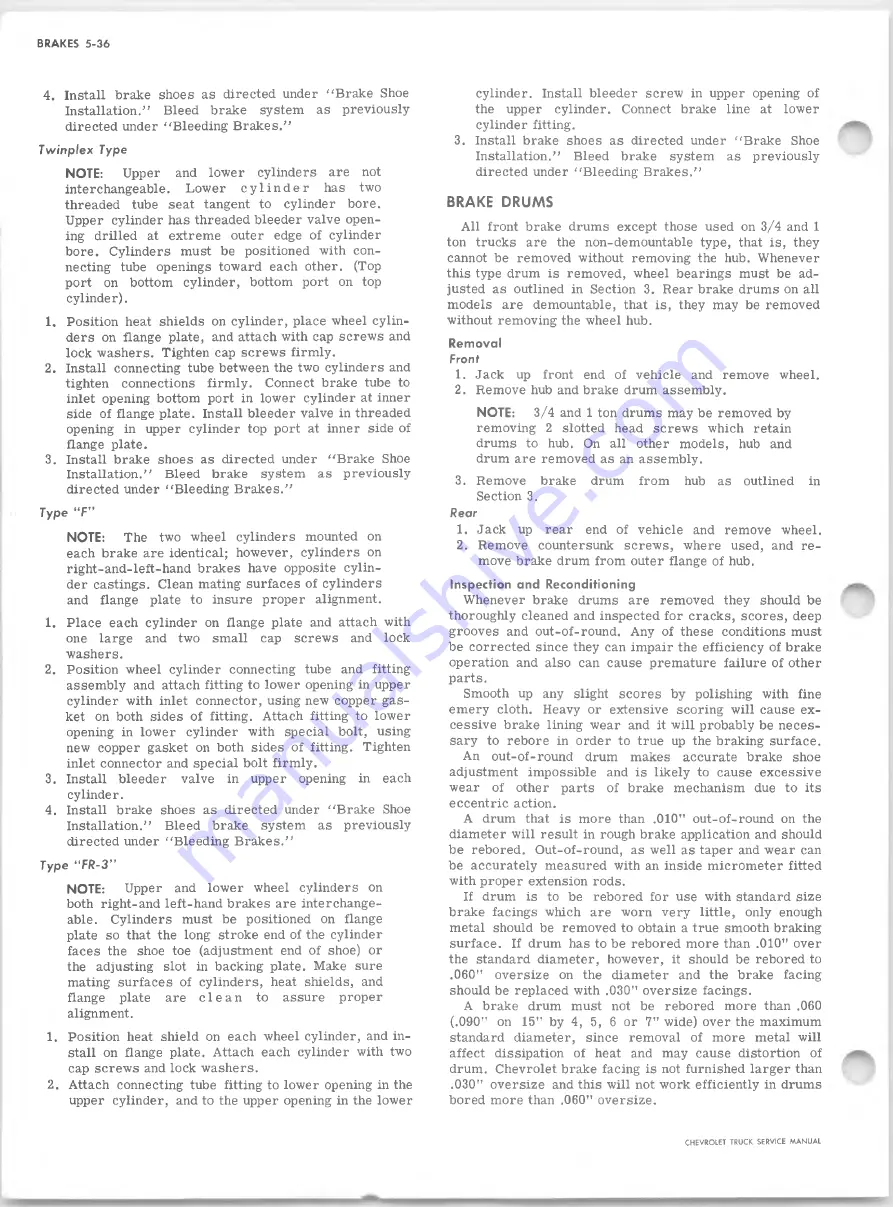
BRAKES 5-36
4. Install brake shoes as directed under “ Brake Shoe
Installation/' Bleed brake system as previously
directed under “ Bleeding Brakes.”
T w inp lex Type
NOTE:
Upper and lower cylinders are not
interchangeable.
Lower c y l i n d e r has two
threaded tube seat tangent to cylinder bore.
Upper cylinder has threaded bleeder valve open
ing drilled at extreme outer edge of cylinder
bore. Cylinders must be positioned with con
necting tube openings toward each other. (Top
port on bottom cylinder, bottom port on top
cylinder).
1. Position heat shields on cylinder, place wheel cylin
ders on flange plate, and attach with cap screws and
lock washers. Tighten cap screws firmly.
2. Install connecting tube between the two cylinders and
tighten connections firm ly. Connect brake tube to
inlet opening bottom port in lower cylinder at inner
side of flange plate. Install bleeder valve in threaded
opening in upper cylinder top port at inner side of
flange plate.
3. Install brake shoes as directed under “ Brake Shoe
Installation." Bleed brake system as previously
directed under “ Bleeding Brakes."
Type “ F ”
NOTE:
The two wheel cylinders mounted on
each brake are identical; however, cylinders on
right-and-left-hand brakes have opposite cylin
der castings. Clean mating surfaces of cylinders
and flange plate to insure proper alignment.
1. Place each cylinder on flange plate and attach with
one large and two small cap screws and lock
washers.
2. Position wheel cylinder connecting tube and fitting
assembly and attach fitting to lower opening in upper
cylinder with inlet connector, using new copper gas
ket on both sides of fitting. Attach fitting to lower
opening in lower cylinder with special bolt, using
new copper gasket on both sides of fitting. Tighten
inlet connector and special bolt firmly.
3. Install bleeder valve in upper opening in each
cylinder.
4. Install brake shoes as directed under “ Brake Shoe
Installation." Bleed brake system as previously
directed under “ Bleeding Brakes."
Type “ F R - 3 ”
NOTE:
Upper and lower wheel cylinders on
both right-and left-hand brakes are interchange
able. Cylinders must be positioned on flange
plate so that the long stroke end of the cylinder
faces the shoe toe (adjustment end of shoe) or
the adjusting slot in backing plate. Make sure
mating surfaces of cylinders, heat shields, and
flange plate are c l e a n to assure proper
alignment.
1. Position heat shield on each wheel cylinder, and in
stall on flange plate. Attach each cylinder with two
cap screws and lock washers.
2. Attach connecting tube fitting to lower opening in the
upper cylinder, and to the upper opening in the lower
cylinder. Install bleeder screw in upper opening of
the upper cylinder. Connect brake line at lower
cylinder fitting.
3. Install brake shoes as directed under “ Brake Shoe
Installation." Bleed brake system as previously
directed under “ Bleeding Brakes."
BRAKE DRUMS
A ll front brake drums except those used on 3/4 and 1
ton trucks are the non-demountable type, that is, they
cannot be removed without removing the hub. Whenever
this type drum is removed, wheel bearings must be ad
justed as outlined in Section 3. Rear brake drums on all
models are demountable, that is, they may be removed
without removing the wheel hub.
Rem oval
Front
1. Jack up front end of vehicle and remove wheel.
2. Remove hub and brake drum assembly.
NOTE:
3/4 and 1 ton drums may be removed by
removing 2 slotted head screws which retain
drums to hub. On all other models, hub and
drum are removed as an assembly.
3. Remove brake drum from hub as outlined in
Section 3.
Rear
1. Jack up rear end of vehicle and remove wheel.
2. Remove countersunk screws, where used, and re
move brake drum from outer flange of hub.
Inspection and Reconditioning
Whenever brake drums are removed they should be
thoroughly cleaned and inspected for cracks, scores, deep
grooves and out-of-round. Any of these conditions must
be corrected since they can impair the efficiency of brake
operation and also can cause premature failure of other
parts.
Smooth up any slight scores by polishing with fine
emery cloth. Heavy or extensive scoring will cause ex
cessive brake lining wear and it will probably be neces
sary to rebore in order to true up the braking surface.
An out-of-round drum makes accurate brake shoe
adjustment impossible and is likely to cause excessive
wear of other parts of brake mechanism due to its
eccentric action.
A drum that is more than .010” out-of-round on the
diameter will result in rough brake application and should
be rebored. Out-of-round, as well as taper and wear can
be accurately measured with an inside micrometer fitted
with proper extension rods.
If drum is to be rebored for use with standard size
brake facings which are worn very little, only enough
metal should be removed to obtain a true smooth braking
surface. If drum has to be rebored more than .010” over
the standard diameter, however, it should be rebored to
.060” oversize on the diameter and the brake facing
should be replaced with .030" oversize facings.
A brake drum must not be rebored more than .060
(.090" on 15" by 4, 5, 6 or 7" wide) over the maximum
standard diameter, since removal of more metal will
affect dissipation of heat and may cause distortion of
drum. Chevrolet brake facing is not furnished larger than
.030" oversize and this will not work efficiently in drums
bored more than .060" oversize.
CHEVROLET TRUCK SERVICE MANUAL
Содержание 10 Series 1968
Страница 1: ...ST 1 3 3 SB...
Страница 3: ...w w...
Страница 52: ...HEATER AND AIR CONDITIONING 1A 21 Fig 32 Charging Schematic CHEVROLET TRUCK SERVICE MANUAL...
Страница 67: ......
Страница 128: ...BODY IB 61 Fig 135 A uxiliary Seat CHEVROLET TRUCK SERVICE MANUAL...
Страница 132: ...Fig 4 1 0 3 0 Series Truck Frame...
Страница 133: ...Fig 5 4 0 6 0 Single A xle Truck Frame E x c Tilt Cab...
Страница 135: ...Fig 7 4 0 6 0 Series Tilt Cab Truck Frames...
Страница 138: ...CHEVROLET TRUCK SERVICE MANUAL Fig 8 Underbody Reference Points and Dimensions Chevy Van G10 and G20 J FRAME 2 9...
Страница 139: ...w...
Страница 169: ...fit w...
Страница 223: ...REAR SUSPENSION AND DRIVE LINE 4 54 Fig 101 Forward Rear Axle Assembly Exploded View CHEVROLET TRUCK SERVICE MANUAL...
Страница 233: ...I...
Страница 248: ...BRAKES 5 15 TD 50 60 Fig 26 Parking Brake Cables T Models CHEVROLET TRUCK SERVICE MANUAL...
Страница 299: ...BRAKES 5 56 Fig 88 Frame Mounted Vacuum Single Diaphragm Power Brake Installation CHEVROLET TRUCK SERVICE MANUAL I...
Страница 331: ...BRAKES 5 88 Fig 126 Stopmaster Brake Components Automatic Adjuster with Fail Safe CHEVROLET TRUCK SERVICE MANUAL...
Страница 347: ......
Страница 389: ......
Страница 393: ......
Страница 398: ...ENGINE FUEL 6M 5 Fig 7 C Throttle Linkage GS100 200 Fig 8C Throttle Linkage GE100 200 CHEVROLET TRUCK SERVICE MANUAL...
Страница 409: ...ENGINE FUEL 6M 16 Fig 12A CM KM 250 CM350 Fig 13A CM KM 250 CM350 CHEVROLET TRUCK SERVICE MANUAL...
Страница 410: ...ENGINE FUEL 6M 17 Fig 14A PE200 300 TE400 500 600 Fig 15A PT200 300 CHEVROLET TRUCK SERVICE MANUAL...
Страница 411: ...ENGINE FUEL 6M 18 Fig 18A V 8 Typical CHEVROLET TRUCK SERVICE MANUAL...
Страница 412: ...ENGINE FUEL 6M 20 ENGINE FUEL 6M 19 Fig 21 A CE100 200 With Heat Stove CHEVROLET TRUCK SERVICE MANUAL...
Страница 413: ...ENGINE FUEL 6M 20 Fig 2 2 A C S K A 1 00 200 CS300 With Heat Stove CHEVROLET TRUCK SERVICE MANUAL...
Страница 414: ...ENGINE FUEL 6M 21 Fig 25A CS PS SS400 CS M S SS500 CS600 TSOOO With Heat Stove CHEVROLET TRUCK SERVICE MANUAL...
Страница 470: ...CLUTCHES AND TRANSMISSIONS 7 7 Fig 14 Clutch Linkage Exploded View CHEVROLET TRUCK SERVICE MANUAL...
Страница 525: ......
Страница 549: ...STEERING 9 16 KA 10 20 CE ME SE 50 CE SE 60 Fig 29 Typical Power Steering Hose Routing CHEVROLET TRUCK SERVICE MANUAL...
Страница 551: ......
Страница 583: ...CHASSIS SHEET METAL 11 12 Fig 20 Designation and Name Plate CHEVROLET TRUCK SERVICE MANUAL...
Страница 585: ...CHASSIS SHEET METAL 11 14 SPECIAL TOOLS Fig 24 J 5544 1 Hood Spring Remover CHEVROLET TRUCK SERVICE MANUAL...
Страница 587: ...ELECTRICAL BODY AND CHASSIS 12 2 Fig 1 Fuse Panel CHEVROLET TRUCK SERVICE MANUAL...
Страница 591: ...ELECTRICAL BODY AND CHASSIS 12 6 CA SA MA 50 60 CHEVY VAN Fig 9 Front Lighting Assemblies CHEVROLET TRUCK SERVICE MANUAL...
Страница 596: ...ELECTRICAL BODY AND CHASSIS 12 11 Fig 15 Electrical Components Conv Cab CHEVROLET TRUCK SERVICE MANUAL...
Страница 611: ...r ELECTRICAL BODY AND CHASSIS 12 26 9 CHEVROLET TRUCK SERVICE MANUAL...
Страница 622: ...ELECTRICAL BODY A N D CHASSIS 12 37 IGNITION SWITCH Fig 44 Engine Compartment PA20 30 CHEVROLET TRUCK SERVICE MANUAL...
Страница 623: ...ELECTRICAL BODY A N D CHASSIS 12 38 Fig 45 Engine Compartment PS40 CHEVROLET TRUCK SERVICE MANUAL...
Страница 633: ...ELECTRICAi BODY A N D CHASSIS 12 48 Fig 55 Engine Compartment SE50 60 02 62 CHEVROLET TRUCK SERVICE MANUAL...
Страница 634: ...YJ ELECTRICAL CHASi V 49 4 Fig 56 Engine Compartment C D C G CD60 CHEVROLET TRUCK SERVICE MANUAL...
Страница 663: ......
Страница 686: ...w...
Страница 698: ...SPECIFICATIONS 12 ENGINE TORQUES CHEVROLET TRUCK SERVICE MANUAL...
Страница 713: ...9...