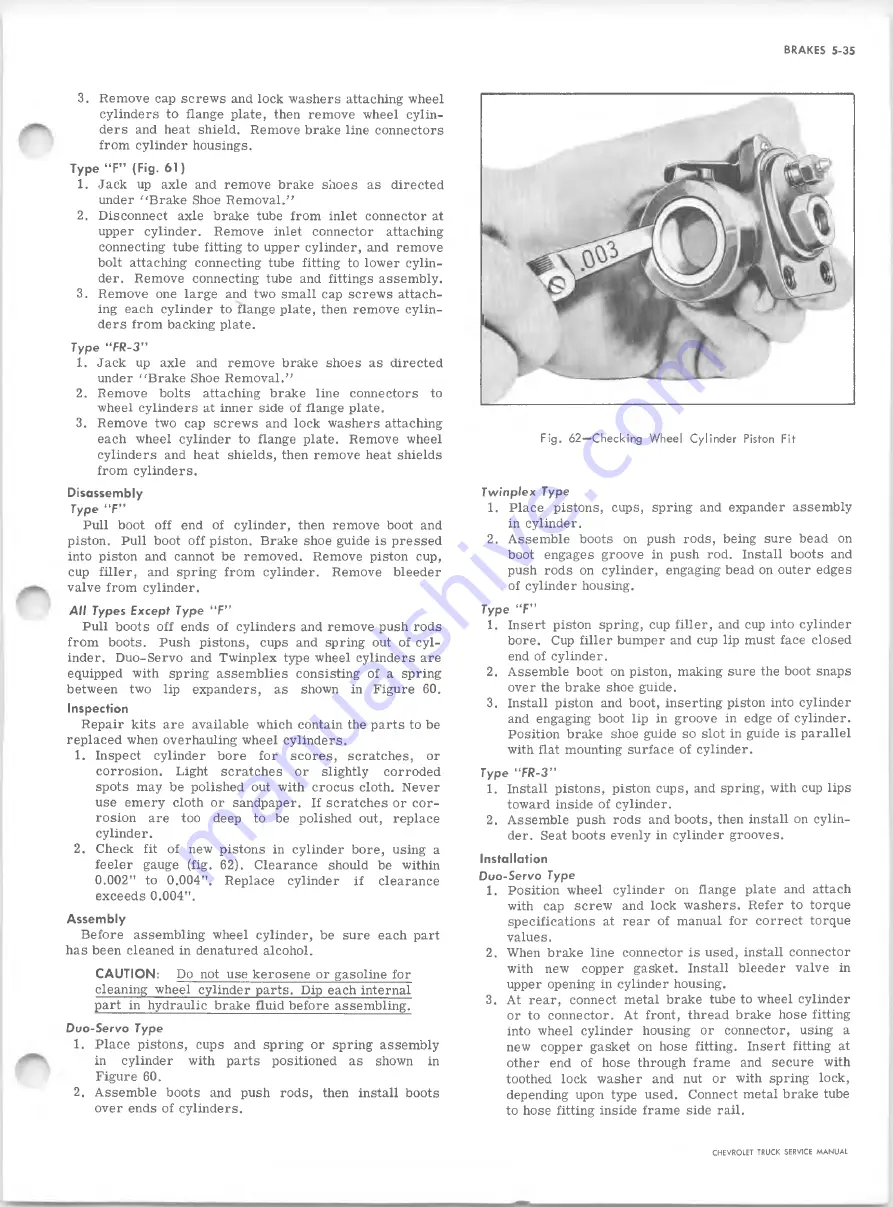
BRAKES 5-35
3. Remove cap screws and lock washers attaching wheel
cylinders to flange plate, then remove wheel cylin
ders and heat shield. Remove brake line connectors
from cylinder housings.
Type “ F” (Fig. 61)
1. Jack up axle and remove brake shoes as directed
under “ Brake Shoe Removal."
2. Disconnect axle brake tube from inlet connector at
upper cylinder. Remove inlet connector attaching
connecting tube fitting to upper cylinder, and remove
bolt attaching connecting tube fitting to lower cylin
der. Remove connecting tube and fittings assembly.
3. Remove one large and two small cap screws attach
ing each cylinder to flange plate, then remove cylin
ders from backing plate.
Type “ F R - 3 ”
1. Jack up axle and remove brake shoes as directed
under “ Brake Shoe Rem oval."
2. Remove bolts attaching brake line connectors to
wheel cylinders at inner side of flange plate.
3. Remove two cap screws and lock washers attaching
each wheel cylinder to flange plate. Remove wheel
cylinders and heat shields, then remove heat shields
from cylinders.
Disassem bly
Type “ F ”
Pull boot off end of cylinder, then remove boot and
piston. Pull boot off piston. Brake shoe guide is pressed
into piston and cannot be removed. Remove piston cup,
cup filler, and spring from cylinder. Remove bleeder
valve from cylinder.
A ll Types Except Type “ F ”
Pull boots off ends of cylinders and remove push rods
from boots. Push pistons, cups and spring out of cyl
inder. Duo-Servo and Twinplex type wheel cylinders are
equipped with spring assemblies consisting of a spring
between two lip expanders, as shown in Figure 60.
Inspection
Repair kits are available which contain the parts to be
replaced when overhauling wheel cylinders.
1. Inspect cylinder bore for scores, scratches, or
corrosion. Light scratches or slightly corroded
spots may be polished out with crocus cloth. Never
use emery cloth or sandpaper. If scratches or cor
rosion are too deep to be polished out, replace
cylinder.
2. Check fit of new pistons in cylinder bore, using a
feeler gauge (fig. 62). Clearance should be within
0.002" to 0.004". Replace cylinder if clearance
exceeds 0.004".
Assem bly
Before assembling wheel cylinder, be sure each part
has been cleaned in denatured alcohol.
CA U TIO N :
Do not use kerosene or gasoline for
cleaning wheel cylinder parts. Dip each internal
part in hydraulic brake fluid before assembling.
D u o -Se rvo Type
1. Place pistons, cups and spring or spring assembly
in cylinder with parts positioned as shown in
Figure 60.
2. Assemble boots and push rods, then install boots
over ends of cylinders.
F ig . 62—Ch eckin g Wheel C y lin d e r Piston Fit
T w inp lex Type
1. Place pistons, cups, spring and expander assembly
in cylinder.
2. Assemble boots on push rods, being sure bead on
boot engages groove in push rod. Install boots and
push rods on cylinder, engaging bead on outer edges
of cylinder housing.
Type “ F ”
1. Insert piston spring, cup filler, and cup into cylinder
bore. Cup fille r bumper and cup lip must face closed
end of cylinder.
2. Assemble boot on piston, making sure the boot snaps
over the brake shoe guide.
3. Install piston and boot, inserting piston into cylinder
and engaging boot lip in groove in edge of cylinder.
Position brake shoe guide so slot in guide is parallel
with flat mounting surface of cylinder.
Type “ F R - 3 ”
1. Install pistons, piston cups, and spring, with cup lips
toward inside of cylinder.
2. Assemble push rods and boots, then install on cylin
der. Seat boots evenly in cylinder grooves.
Installation
D uo -Servo Type
1. Position wheel cylinder on flange plate and attach
with cap screw and lock washers. Refer to torque
specifications at rear of manual for correct torque
values.
2. When brake line connector is used, install connector
with new copper gasket. Install bleeder valve in
upper opening in cylinder housing.
3. At rear, connect metal brake tube to wheel cylinder
or to connector. At front, thread brake hose fitting
into wheel cylinder housing or connector, using a
new copper gasket on hose fitting. Insert fitting at
other end of hose through frame and secure with
toothed lock washer and nut or with spring lock,
depending upon type used. Connect metal brake tube
to hose fitting inside frame side rail.
CHEVROLET TRUCK SERVICE MANUAL
Содержание 10 Series 1968
Страница 1: ...ST 1 3 3 SB...
Страница 3: ...w w...
Страница 52: ...HEATER AND AIR CONDITIONING 1A 21 Fig 32 Charging Schematic CHEVROLET TRUCK SERVICE MANUAL...
Страница 67: ......
Страница 128: ...BODY IB 61 Fig 135 A uxiliary Seat CHEVROLET TRUCK SERVICE MANUAL...
Страница 132: ...Fig 4 1 0 3 0 Series Truck Frame...
Страница 133: ...Fig 5 4 0 6 0 Single A xle Truck Frame E x c Tilt Cab...
Страница 135: ...Fig 7 4 0 6 0 Series Tilt Cab Truck Frames...
Страница 138: ...CHEVROLET TRUCK SERVICE MANUAL Fig 8 Underbody Reference Points and Dimensions Chevy Van G10 and G20 J FRAME 2 9...
Страница 139: ...w...
Страница 169: ...fit w...
Страница 223: ...REAR SUSPENSION AND DRIVE LINE 4 54 Fig 101 Forward Rear Axle Assembly Exploded View CHEVROLET TRUCK SERVICE MANUAL...
Страница 233: ...I...
Страница 248: ...BRAKES 5 15 TD 50 60 Fig 26 Parking Brake Cables T Models CHEVROLET TRUCK SERVICE MANUAL...
Страница 299: ...BRAKES 5 56 Fig 88 Frame Mounted Vacuum Single Diaphragm Power Brake Installation CHEVROLET TRUCK SERVICE MANUAL I...
Страница 331: ...BRAKES 5 88 Fig 126 Stopmaster Brake Components Automatic Adjuster with Fail Safe CHEVROLET TRUCK SERVICE MANUAL...
Страница 347: ......
Страница 389: ......
Страница 393: ......
Страница 398: ...ENGINE FUEL 6M 5 Fig 7 C Throttle Linkage GS100 200 Fig 8C Throttle Linkage GE100 200 CHEVROLET TRUCK SERVICE MANUAL...
Страница 409: ...ENGINE FUEL 6M 16 Fig 12A CM KM 250 CM350 Fig 13A CM KM 250 CM350 CHEVROLET TRUCK SERVICE MANUAL...
Страница 410: ...ENGINE FUEL 6M 17 Fig 14A PE200 300 TE400 500 600 Fig 15A PT200 300 CHEVROLET TRUCK SERVICE MANUAL...
Страница 411: ...ENGINE FUEL 6M 18 Fig 18A V 8 Typical CHEVROLET TRUCK SERVICE MANUAL...
Страница 412: ...ENGINE FUEL 6M 20 ENGINE FUEL 6M 19 Fig 21 A CE100 200 With Heat Stove CHEVROLET TRUCK SERVICE MANUAL...
Страница 413: ...ENGINE FUEL 6M 20 Fig 2 2 A C S K A 1 00 200 CS300 With Heat Stove CHEVROLET TRUCK SERVICE MANUAL...
Страница 414: ...ENGINE FUEL 6M 21 Fig 25A CS PS SS400 CS M S SS500 CS600 TSOOO With Heat Stove CHEVROLET TRUCK SERVICE MANUAL...
Страница 470: ...CLUTCHES AND TRANSMISSIONS 7 7 Fig 14 Clutch Linkage Exploded View CHEVROLET TRUCK SERVICE MANUAL...
Страница 525: ......
Страница 549: ...STEERING 9 16 KA 10 20 CE ME SE 50 CE SE 60 Fig 29 Typical Power Steering Hose Routing CHEVROLET TRUCK SERVICE MANUAL...
Страница 551: ......
Страница 583: ...CHASSIS SHEET METAL 11 12 Fig 20 Designation and Name Plate CHEVROLET TRUCK SERVICE MANUAL...
Страница 585: ...CHASSIS SHEET METAL 11 14 SPECIAL TOOLS Fig 24 J 5544 1 Hood Spring Remover CHEVROLET TRUCK SERVICE MANUAL...
Страница 587: ...ELECTRICAL BODY AND CHASSIS 12 2 Fig 1 Fuse Panel CHEVROLET TRUCK SERVICE MANUAL...
Страница 591: ...ELECTRICAL BODY AND CHASSIS 12 6 CA SA MA 50 60 CHEVY VAN Fig 9 Front Lighting Assemblies CHEVROLET TRUCK SERVICE MANUAL...
Страница 596: ...ELECTRICAL BODY AND CHASSIS 12 11 Fig 15 Electrical Components Conv Cab CHEVROLET TRUCK SERVICE MANUAL...
Страница 611: ...r ELECTRICAL BODY AND CHASSIS 12 26 9 CHEVROLET TRUCK SERVICE MANUAL...
Страница 622: ...ELECTRICAL BODY A N D CHASSIS 12 37 IGNITION SWITCH Fig 44 Engine Compartment PA20 30 CHEVROLET TRUCK SERVICE MANUAL...
Страница 623: ...ELECTRICAL BODY A N D CHASSIS 12 38 Fig 45 Engine Compartment PS40 CHEVROLET TRUCK SERVICE MANUAL...
Страница 633: ...ELECTRICAi BODY A N D CHASSIS 12 48 Fig 55 Engine Compartment SE50 60 02 62 CHEVROLET TRUCK SERVICE MANUAL...
Страница 634: ...YJ ELECTRICAL CHASi V 49 4 Fig 56 Engine Compartment C D C G CD60 CHEVROLET TRUCK SERVICE MANUAL...
Страница 663: ......
Страница 686: ...w...
Страница 698: ...SPECIFICATIONS 12 ENGINE TORQUES CHEVROLET TRUCK SERVICE MANUAL...
Страница 713: ...9...