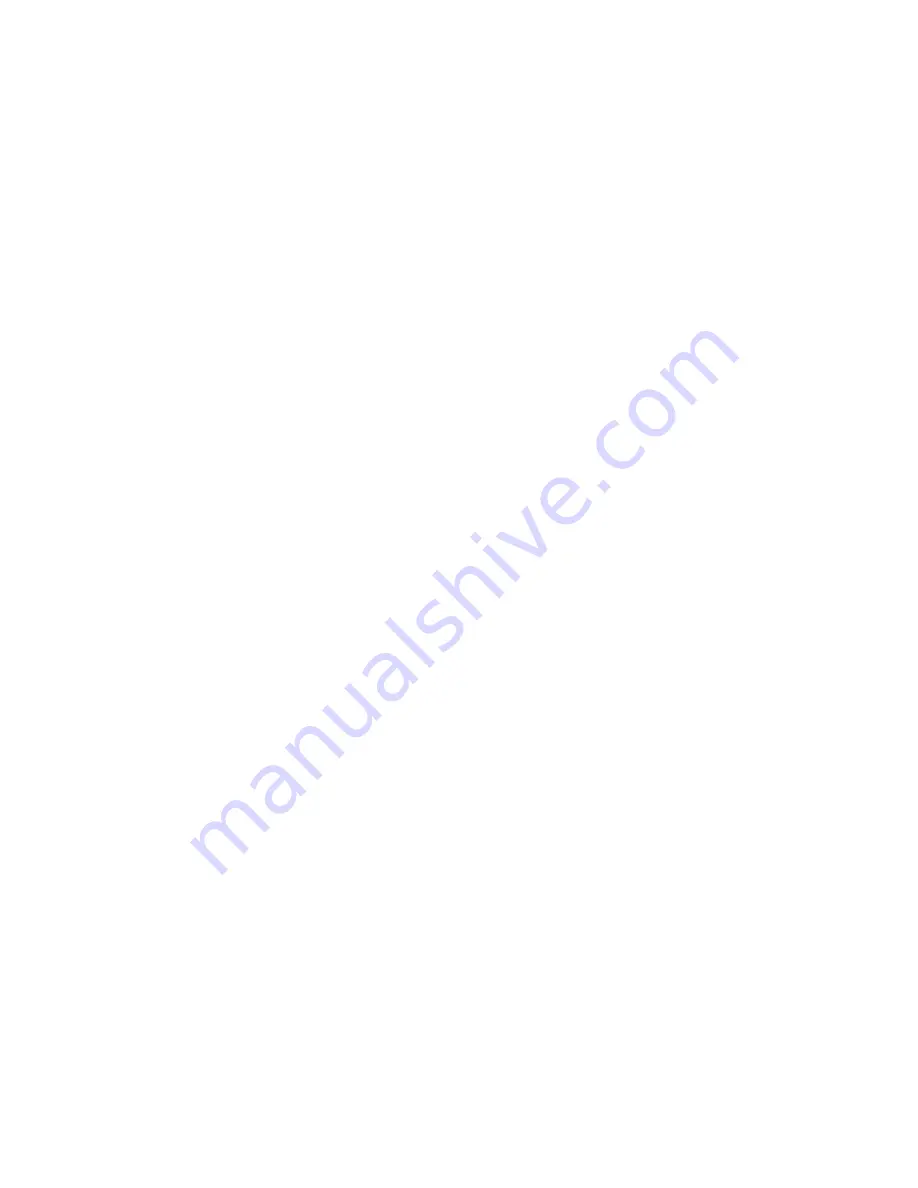
Heat Manager Pro User Manual V1.5 Page 56
3.3
PID
S
ETTINGS
(
TEMPERATURE CONTROL RESPONSE
)
With these settings the behavior of the temperature control system with respect to a difference
between desired and actual temperature can be adjusted.
Use these settings with caution, since they influence the response of the system to a
deviation, setting values too high or too low can result in too large temperature
deviations and or damage to the workpiece and or equipment. It is also possible that a
dangerous situation can occur because of a too high temperature, so use these values
with caution. The default values have been found to work ok in most cases, but there are
possible situations that the ratio of installed heating power/mass of workpiece are
deviating a lot from where these settings were obtained, then a re-adjustment is
necessary.
ONLY CHANGE THESE SETTINGS WHEN YOU HAVE EXPERIENCE WITH SETTING PID
CONTROLLER PARAMETERS FOR TEMPERATURE CONTROL PROCESSES.
USE THE AT (AUTOTUNING) SETTING WITH CAUTION, SINCE THE PID CONTROLLER
WILL TRY TO AUTOMATICALLY DETERMINE THE PID SETTINGS. IN ORDER TO DO SO,
THE OUTPUT CONTROL PERCENTAGE WILL BE SET TO 100% AND 0% A FEW TIMES, IN
ORDER TO MEASURE THE TEMPERATURE RESPONSE. THIS CAN RESULT IN A TOO
HIGH TEMPERATURE AND/OR STRESS ON THE WORKPIECE.
USE A “DUMMY” WORKPIECE WITH APPROX. THE SAME MASS IN CASE OF DOUBT.
The PID settings can be set for each separate segment of the process. Segment 8 is the
segment that is used for channels that are not a programmer. A programmer that is not in
stopped state is also set to segment 8.
Note: refer to the appendix on PID temperature control for more explanation on the
setting of PID parameters.