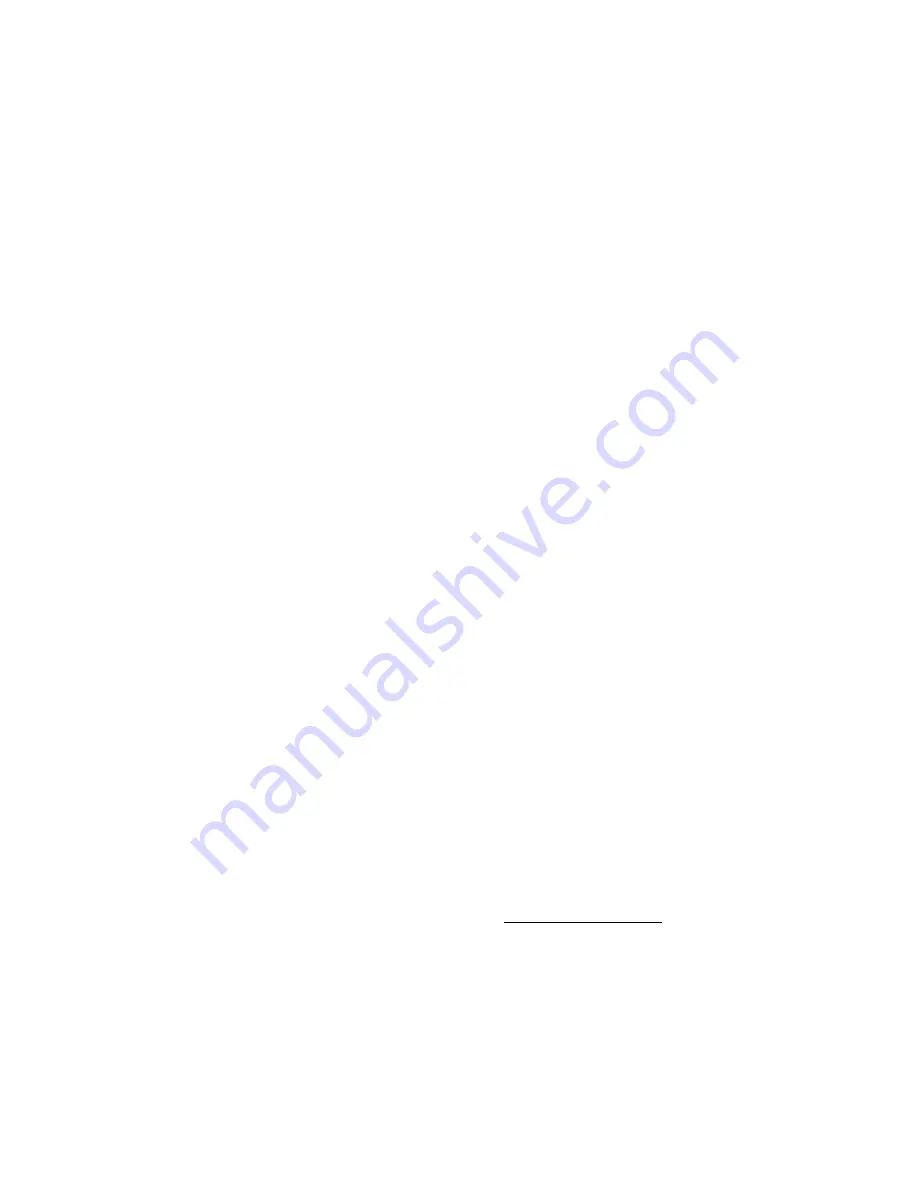
31
THIRD PARTY CONTROL
Thermostat —
The method of control would be through
the thermostat inputs:
Y1 = first stage cooling
Y1 and Y2 = first and second stage cooling
W1 = first stage heating
W1 and W2 = first and second stage heating
G = supply fan
Alarm Output —
The alarm output TB4-7 and 8, will pro-
vide relay closure whenever the unit is under an alert or alarm
condition.
Remote Switch —
The remote switch may be configured
for three different functions. Under
Configuration
UNIT,
set
RM.CF
to one of the following:
0 = no remote switch
1 = occupied/unoccupied switch
2 = start/stop switch
3 = occupancy override switch
With
RM.CF
set to 1, no time schedules are followed and
the unit follows the remote switch only in determining the state
of occupancy.
With
RM.CF
set to 2, the remote switch can be used to shut
down and disable the unit, while still honoring time guards on
compressors. Time schedules, internal or external, may be run
simultaneously with this configuration.
With
RM.CF
set to 3, the remote input may override an
unoccupied state and force the control to go into occupied
mode. As with the start/stop configuration, an internal or exter-
nal time schedule may continue to control occupancy when the
switch is not in effect.
Under
Configuration
SW.LG
RMI.L
, the remote occu-
pancy switch can be set to either a normally open or normally
closed switch input. Normal is defined as either unoccupied, start
or “not currently overridden,” respective to the
RM.CF
configuration.
VFD Control —
On VFD equipped supply fans, supply
duct static pressure control may be left under unit control or be
externally controlled. To control a VFD externally with a 4 to
20 mA signal, set
SP.RS
to 4, under the
Configuration
SP
menu. This will set the reset to VFD control. When
SP.RS
= 4,
the static pressure reset function acts to provide direct VFD
speed control where 4 mA = 0% speed and 20 mA = 100%
(
SP.MN
and
SP.MX
will override). Note that
SP.CF
must be
set to 1 (VFD Control) prior to configuring
SP.RS
= 4. Failure
to do so could result in damage to ductwork due to overpressur-
ization. In effect, this represents a speed control signal “pass
through” under normal operating circumstances. The
Com-
fort
Link controller overrides the third party signal for critical
operation situations, most notably smoke and fire control. Wire
the input to the controls expansion module (CEM) using TB-11
and 12. An optional CEM board is required.
See Appendix C and the VFD literature supplied with the unit
for VFD configurations and field wiring connections to the VFD.
Supply Air Reset —
With the installation of the CEM,
the
Comfort
Link controller is capable of accepting a 4 to
20 mA signal, to reset the supply-air temperature up to a maxi-
mum of 20 F. See VFD Control section above.
Demand Limit Control —
The term “demand limit
control” refers to the restriction of the machine’s mechanical
cooling capacity to control the amount of power that a machine
may use.
Demand limiting using mechanical control is possible via two
means:
Two discrete inputs tied to demand limit set point percentages.
OR
A 4 to 20 mA input that can reduce or limit
capacity linearly to
a set point percentage.
In either case, it will be necessary to install a controls ex-
pansion module (CEM).
DEMAND LIMIT DISCRETE INPUTS — First, set
DM.L.S
in
Configuration
DMD.L
to 1 (2 switches).
When
Inputs
GEN.I
DL.S1
(Demand Switch no. 1) is
OFF, the control will not set any limit to the capacity, and
when ON, the control sets a capacity limit to the
Configura-
tion
DMD.L
D.L.S1
set point.
Likewise, when
Inputs
GEN.I
DL.S2
(Demand Switch
no. 2) is OFF, the control will not set any limit to the capacity,
and when ON, the control sets a capacity limit to the
Configu-
ration
DMD.L
D.L.S2
set point.
If both switches are ON,
Inputs
GEN.I
DL.S2
is used
as the limiter of capacity.
Under
Configuration
SW.LG
,
set the logic state appropri-
ately for the action desired. Set the
DL1.L
and
DL2.L
configu-
rations. They can be set normally open or normally closed. For
example, if
DL1.L
is set to OPEN, the user will need to close
the switch to cause the control to limit capacity to the demand
limit 1 set point. Likewise, if
DL1.L
is set to CLSE (closed),
the user will need to open the switch to cause the control to
limit capacity to the demand limit 1 set point.
DEMAND LIMIT 4 TO 20 mA INPUT — Under
Configu-
ration
DMD.L
,
set configuration
DM.L.S
to 2 (2 = 4 to
20 mA control). Under the same menu, set
D.L.20
to a value
from 0 to 100% to set the demand limit range. For example,
with
D.L.20
set to 50, a 4 mA signal will result in no limit to
the capacity and 20 mA signal will result in a 50% reduction in
capacity.
Demand Controlled Ventilation Control —
There are multiple methods for externally controlling the econ-
omizer damper.
IAQ DISCRETE INPUT CONFIGURATION — The IAQ dis-
crete input configuration requires a CEM module (optional) to
be installed and an interface to a switch input at TB5-13 and
14. The state of the input on the display can be found at
Inputs
AIR.Q
IAQ.I.
Before configuring the switch functionality, first determine
how the switch will be read. A closed switch can indicate either
a low IAQ condition or a high IAQ condition. This is set at
Configuration
SW.LG
and
IAQ.L
. The user can set what a
low reading would mean based on the type of switch being
used. Setting
IAQ.L
to OPEN means that when the switch is
open the input will read LOW. When the switch is closed, the
input will read HIGH. Setting
IAQ.L
to CLSE (closed) means
that when the switch is closed the input will read LOW, and
therefore, when the switch is open the switch will read HIGH.
There are two possible configurations for the IAQ discrete
input. Select item
Configuration
IAQ
AQ.CF
IQ.I.C
and configure for either 1 (IAQ Discrete) or 2 (IAQ Discrete
Override).
IQ.I.C
= 1
(IAQ Discrete) — If the user sets
IQ.I.C
to 1 (IAQ
Discrete), and the switch logic (
Configuration
SW.LG
IAQ.L
) is set to OPEN, then an open switch reads low and a
closed switch reads high.
If the switch is open, the economizer will be commanded to
the IAQ Demand Vent Minimum Position.
These settings may be adjusted and are located at
Configura-
tion
IAQ
DCV.C
IAQ.M
.
If the switch is closed, the IAQ reading will be high and the
economizer will be commanded to the Economizer Minimum
Position.
This setting may be adjusted and is located at
Configura-
tion
IAQ
DCV.C
EC.MN
.
Содержание WEATHERMAKER 48/50AJ
Страница 103: ...103 Fig 15 Typical Main Control Box Wiring Schematic 48 50AJ AK AW AY Units cont a48 8355 ...
Страница 104: ...104 Fig 16 Typical Main Control Box Wiring Schematic 48 50A2 A3 A4 A5 Units a48 8355 ...
Страница 105: ...105 TO NEXT PAGE Fig 17 Typical Auxiliary Control Box Wiring Schematic A48 7294 ...
Страница 106: ...106 Fig 17 Typical Auxiliary Control Box Wiring Schematic cont a48 8356 ...
Страница 107: ...107 Fig 18 Typical 2 Stage Gas Heat Wiring Schematic Size 051 and 060 Units Shown a48 8357 ...
Страница 108: ...108 TO NEXT PAGE Fig 19 Typical Staged Gas Heat Wiring Schematic Size 051 and 060 Units Shown A48 7296 ...
Страница 109: ...109 Fig 19 Typical Staged Gas Heat Wiring Schematic Size 051 and 060 Units Shown cont A48 8358 ...
Страница 110: ...110 Fig 20 Typical Electric Heat Control Schematic 50 Series Size 051 and 060 Units Shown a50 8228 ...
Страница 111: ...111 TO NEXT PAGE Fig 21 Typical Power Schematic 48 50AJ AK AW AY051 and 060 Units Shown A48 7298 ...
Страница 112: ...112 FROM PREVIOUS PAGE Fig 21 Typical Power Schematic 48 50AJ AK AW AY051 and 060 Units Shown cont a48 8360 ...
Страница 113: ...113 Fig 22 Typical Power Schematic 48 50A2 A3 A4 A5060 Unit Shown ...
Страница 114: ...114 SW1 SW2 OR DEHUMIDIFY SWITCH Fig 23 Typical Controls Option Wiring Schematic a48 8361 ...
Страница 115: ...115 Fig 24 Typical Small Chassis Component Location Size 020 035 Units a48 8362 ...
Страница 116: ...116 Fig 25 Typical Large Chassis Component Locations Size 036 060 Units A48 7302 ...
Страница 169: ...169 APPENDIX C VFD INFORMATION cont Fig F Internal Enclosure Fan Replacement A48 7716 ...