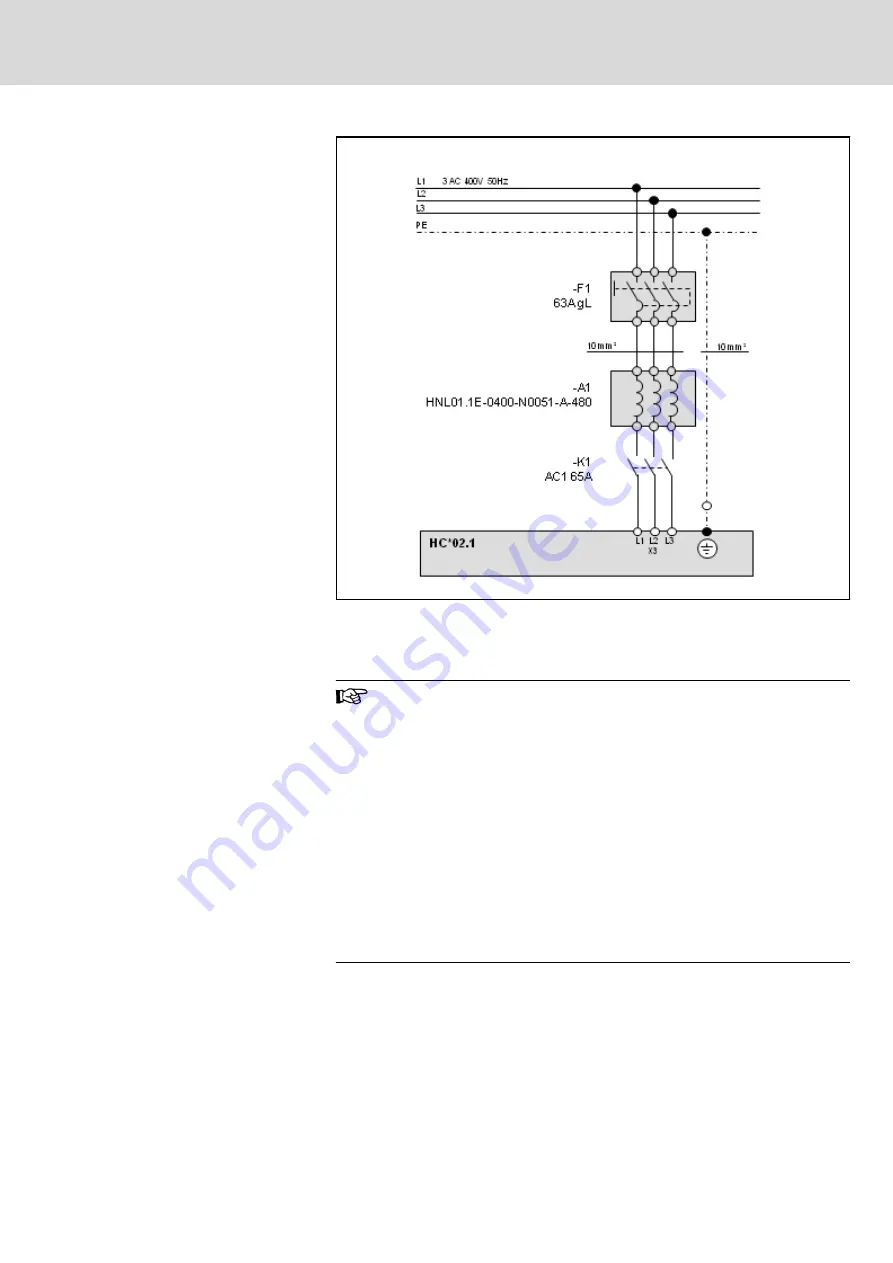
-F1:
Line fuse
-A1:
HNL line reactor
-K1:
Line contactor
Fig. 5-15:
Power supply connection for HCQ/HCT
●
The cross-section required for connection to the power sup‐
ply network is 10 mm².
●
The cross section required for connection of the protective
conductor is also 10 mm². (Also see "Grounding")
●
Strain relief must be provided for the connection terminals
(X3). The necessary HAS02 connecting accessories are
available.
●
The line fuse must be designed with 3 phases, with 63 A gL
for each phase. We recommend that you use a motor pro‐
tecting switch with a tripping current of 65 A.
●
The HNL01.1E0400N0051A480 line reactor must be used to
protect the power supply.
●
The line contactor must be designed for a rated current of
AC1 65 A.
Network types
Direct three-phase connection of the HCQ02 and HCT02 devices is allowed
to the following network types:
●
TN-S, TN-C
Under certain circumstances, the devices can also be connected to the fol‐
lowing network types:
●
TT
DOK-MTXMIC-EASY*******-CO06-EN-P
Bosch Rexroth AG
45/177
IndraMotion MTX micro Easy Setup for Standard Turning and Milling Machines
Selecting and connecting the hardware