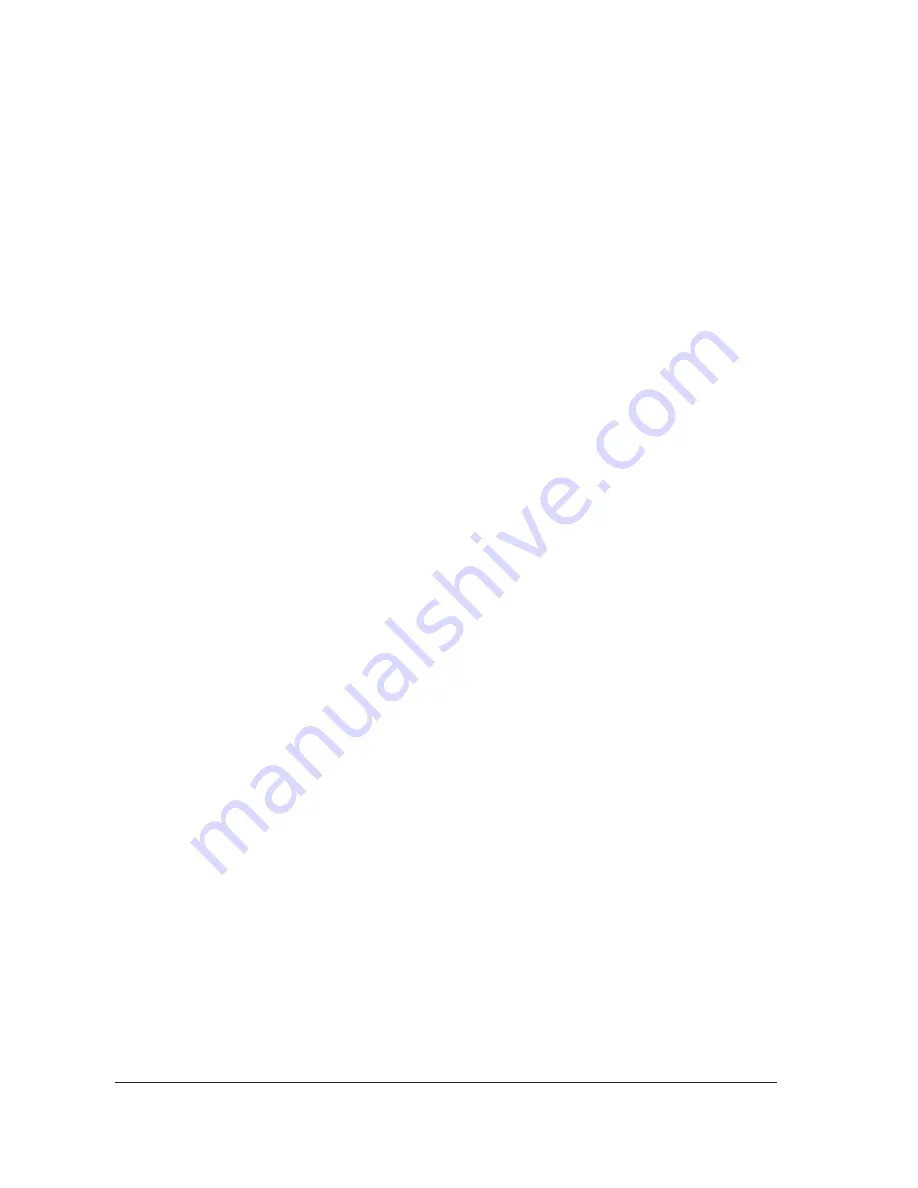
1.2
Overview
1.2.1
The iL system
The iL system operates at pressures between atmospheric and ultimate vacuum with no
lubricating or sealing fluid in the pumping chamber(s). This ensures a clean pumping system
without back-migration of oil into the system being evacuated.
The iL70 system has an LCDP70 dry pump; the iL600 system has an LCDP70 dry pump, with an
LCMB600 mechanical booster pump fitted to the inlet of the LCDP pump. Throughout the
remainder of this manual, the LCDP70 pump is referred to as the LCDP pump and the LCMB600
pump is referred to as the LCMB pump.
Both the LCDP and LCMB pumps have enclosed, water-cooled motors. The iL system is
therefore suitable for applications in clean environments where fan cooling is unacceptable.
Two versions of iL system are available, sensor-configured iL systems and standard iL systems:
•
Sensor-configured iL systems have: a gas system which introduces purge gas into the LCDP
shaft-seals; temperature sensors; other accessories (as described in the remainder of this
manual). Sensor-configured iL systems are suitable for use on light duty processes.
•
Standard iL systems have no gas system, temperature sensors or other accessories. Standard
iL systems are suitable for use on clean duty processes.
The iL system is designed to operate as a sealed unit, chemicals passing through the pump being
contained within the internal volume and separated from the external environment by a
mechanical barrier. This barrier is made up of a number of components of different materials,
(see Section 2.8), chosen to be resistant to attack by chemicals usually found in clean applications.
Pumping a chemical that will aggressively attack any of these barrier materials may, over time,
result in the internal contents of the pump becoming exposed to the external environment ,
which may constitute a safety hazard. If in doubt contact BOC Edwards who will advise you as
to the suitability of this pump for any particular application.
It is also a feature of this pump design that the process gases are contained within the gearbox. If
hazardous materials are being pumped special precautions must therefore be taken before the
gearbox volume is accessed, details of this are given in Section 6. For this reason it is important to
refer to this section before adding oil or opening the gearbox to atmosphere.
On sensor configured iL systems the purge gas acts as a barrier to protect the gearbox from
process gas contamination. However, high pressure in exhaust pipe, exceeding that stated in
section 2, could lead to gearbox contamination which will reduce the service life of product.
You can manually control the iL system through a Pump Display Module accessory: see
Section 1.11. Alternatively, you can use your process tool or other control equipment to control
the operation of the iL system through an Interface Module accessory (refer to Section 8.4.5), or
through an iL Communications Module accessory (see Section 8.4.9), or you can use the iL Single
Pumpset Monitor accessory to control the operation of the iL system (refer to Section 8.4.6). The
remainder of this manual describes the use of the Pump Display Module to operate the iL
1-2
iL Dry Pumping Systems
(Continued on page 1-4)
Содержание iL600
Страница 18: ...iL Dry Pumping Systems 1 9 Figure 1 3 Schematic diagram of the electrical system...
Страница 21: ...1 12 iL Dry Pumping Systems Figure 1 4 Services and electrical connections on the rear of the iL system...
Страница 23: ...1 14 iL Dry Pumping Systems Figure 1 5 Electrical components shown without enclosure for clarity...
Страница 71: ...3 28 iL Dry Pumping Systems...