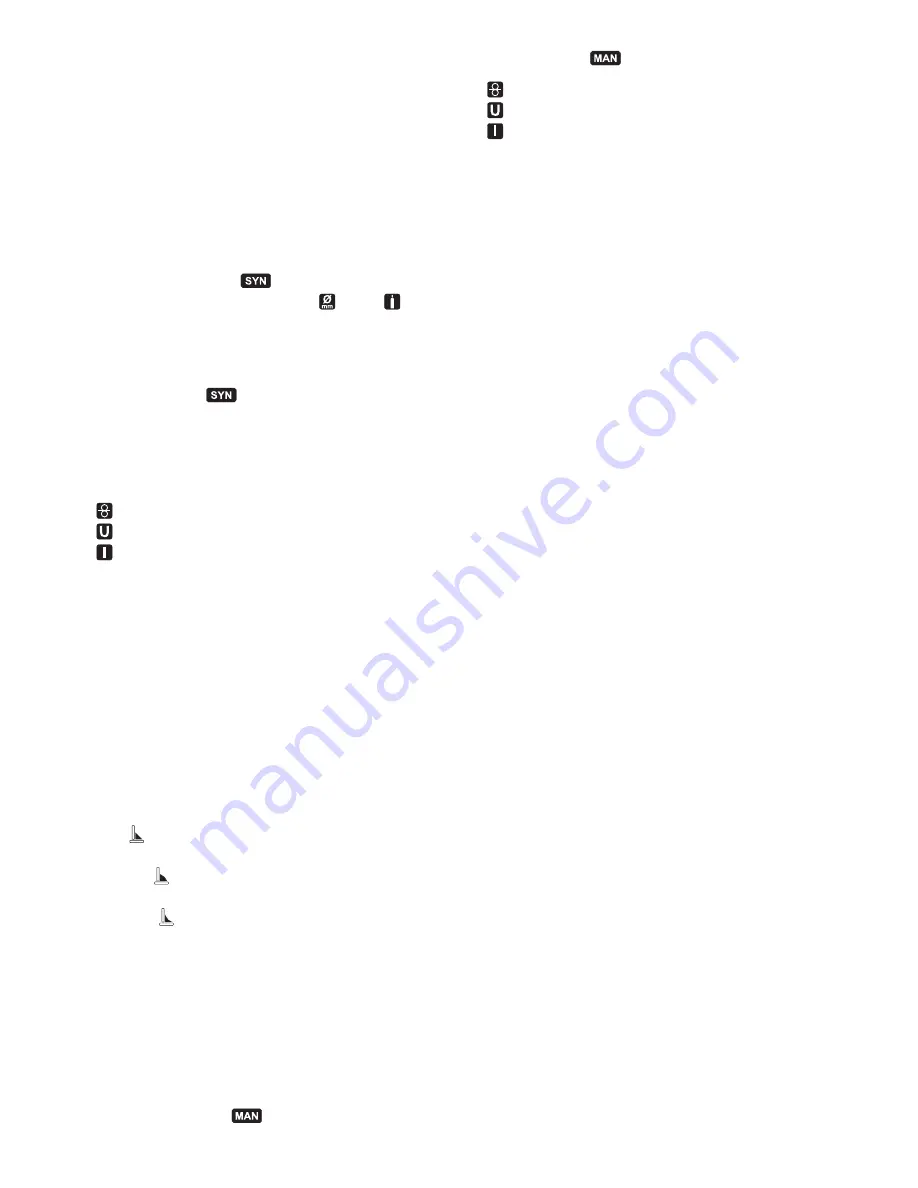
- 8 -
6. MIG-MAG WELDING PROCESS DESCRIPTION
6.1 SHORT ARC
The wire melts and the weld bead detaches because the wire tip in the weld pool short-
circuits (up to 200 times per second). The free length of the wire (stick-out) is normally
between 5 and 12 mm.
Carbon steel and low-alloys
- Usable wire diameter:
0.6 - 0.8 - 1.0 mm (1.2 mm version 270A only)
- Usable gas:
CO
2
or Ar/CO
2
mixes
Stainless steel
- Usable wire diameter:
0.8 - 1.0 mm (1.2 mm version 270A only)
- Usable gas:
Ar/O
2
or Ar/CO
2
(1-2%) mixes
Aluminium and CuSi/CuAl
- Usable wire diameter:
0.8 - 1.0 mm (1.2 mm version 270A only)
- Usable gas:
Ar
Core wire (versions 180A and 200A only)
- Usable wire diameter:
0.8 - 0.9 - 1.2 mm
- Usable gas:
None
6.2 PROTECTIVE GAS
The protective gas flow rate must be 8-14 l/min.
7. MIG-MAG OPERATION MODE
7.1 Operation in SYNERGIC mode
When the parameters such as material, wire diameter
, gas type
have been
defined by the user, the welding machine sets itself automatically in the best operation
conditions established by the different synergy curves that are saved. The user only
has to select the material thickness to begin welding (OneTouch Technology).
7.1.1 LCD display in SYNERGIC mode (Fig. H)
N.B.: All the values that are shown and that can be selected depend on the type of
welding selected previously.
1- Synergy operation mode
;
2- Material to be welded. Types available: Fe (steel), SS (stainless steel), Al
(aluminium), CuSi/CuAl (galvanized plate - brazing), Flux (cored wire - NO GAS
welding);
3- Diameter of the wire to be used. Values available: 0.6 - 0.8 - 0.9 - 1 - 1.2 mm;
4- Recommended protective gas. Types available: Ar/CO
2
, CO
2
, Ar, Ar/O
2
;
5- Thickness of the material to be welded. Values available from 0 to 5 mm;
6- Graphic indicator of the material thickness
7- Graphic indicator of the welding seam shape;
8- Welding values;
wire feed speed;
welding voltage;
welding current;
9- ATC (Advanced Thermal Control).
7.1.2 Setting the parameters
To access the parameter adjustment menu press the knob (Fig. C-2) for at least 1
second then release it:
a) material selection (Fig. H-2 material flashing)
- rotate the knob (Fig. C-2) to select the required material and confirm by pressing
and releasing the same knob;
b) wire diameter selection (Fig. H-3 wire diameter flashing)
- rotate the knob (Fig. C-2) to select the required material and confirm by pressing
and releasing the same knob;
c) gas selection (Fig. H-4 gas type flashing)
- rotate the knob (Fig. C-2) or directly select the proposed gas and confirm by
pressing and releasing the knob; this allows exiting from the parameter settings
menu and the display on the monitor of the pre-set values.
After having defined with the knob (Fig. C-1) the material thickness (Fig. H-5) the user
can start welding.
7.1.3 Adjusting the welding seam shape
The shape of the welding seam can be adjusted using the knob (Fig. C-2) which
adjusts the arc length, therefore establishing the higher or lower temperature for
welding.
The adjustment scale ranges from -9 ÷ 0 ÷ +9; in most cases the optimal basic setting
is given (the value is shown on the LCD display to the left of the graphic signal showing
the welding seam and disappears after a set time) when the knob is in the intermediate
position (0
).
Using the knob (Fig. C-2) the graphic indication on the display of the welding seam
changes, showing a more convex, flatter or more concave result.
Convex shape.
It means that there is a low thermal supply therefore welding is
“cold”, with little penetration; rotate the knob clockwise for greater thermal supply to
weld with higher fusion.
Concave shape.
It means there is a high thermal supply therefore welding is too
“hot”, with excessive penetration; rotate the knob counter-clockwise for lower fusion.
7.1.4 ATC Mode (Advanced Thermal Control)
This is enabled automatically when the thickness selected is less or equal to 1.5 mm.
Description: the particular instantaneous control of the welding arc and the ultra rapid
correcting of parameters minimize current spikes, something that is characteristic of
Short Arc transfer procedures, to the advantage of a low thermal load on the piece
to be welded. The result, on the one hand, is reduced deformation of materials and,
on the other, a fluid and accurate transfer of the weld material and the creation of a
welding seam that is easy to model.
Advantages:
- easy welding of thin materials;
- decreased deformation of material;
- stable arc even when working with low currents;
- rapid and accurate spot welding;
- easier coupling of spaced sheets.
7.2 Operation in MANUAL mode
The user can personalise all the welding parameters.
7.2.1 LCD display in SYNERGIC mode (Fig. I)
1- Manual operation mode
;
2- Welding values;
wire feed speed;
welding voltage;
welding current;
7.2.2 Setting the parameters
In manual mode, the wire feeding speed and the welding voltage are adjusted
separately. The knob (Fig. C-1) adjusts the wire speed, the knob (Fig. C-2) adjusts
the welding voltage (which determines the welding power and influences the seam
shape). The welding current is shown on the display (Fig. I-2) only during welding.
8. CONTROLLING THE TORCH PUSH-BUTTON
8.1 Torch push-button control mode
3 different torch push-button control modes can be set, which remain valid with both
synergic and manual operation:
Spot welding mode (Fig. L-5)
Use for MIG/MAG spot welding with control of welding duration (when at OFF
excluded; 0.1÷5 seconds).
2T mode (Fig. L-6)
Welding begins when the torch push-button is pressed and ends when the push-
button is released.
4T mode (Fig. L-6)
Welding begins when the torch push-button is pressed and released, and ends only
when the torch push-button is pressed and released a second time. This mode is
useful for long welding operations.
8.2 Setting the torch push-button control mode
To access the parameter adjustment menu press the knob (Fig. C-2) for at least 3
second then release it:
a) Spot welding time adjustment (Fig. L-5 flashing).
Rotate the knob (Fig. C-2) to select the required time or select “OFF” to disable the
function; confirm by pressing and releasing the same knob.
If the spot welding time is set at a value of between 0.1-5 sec., the “2T/4T” modes
cannot be selected. In this case pressing the knob causes the exit from the menu.
b) 2T or 4T selection (Fig. L-6 flashing and “2T” or “4T” written on Fig. L-7).
The user can select whether to use the 2T or the 4T mode, but only if the spot
welding time is set at “OFF”. Rotate the knob and select the required mode, then
confirm and exit from the menu by pressing the knob.
9. ADVANCED SETTINGS
9.1 Adjustable advanced parameters
It is possible to customise, in both synergic and manual mode, the following welding
parameters:
Trailing wire ramp (Fig. L-1)
Use to set the trailing wire starting ramp to prevent any initial accumulation in the
welding seam. Adjustable from 20 to 100 (start in % of full capacity speed).
Electronic reactance (Fig. L-2)
Use to set the welding dynamics according to the material and gas used.
For versions 180A and 200A:
- Settings from 0 (low reactance machines) to 5 (high reactance machines).
For version 270A:
- Manual mode: settings from 0 (low reactance machines) to 100 (high reactance
machines).
- Synergic mode: electronic reactance correction compared to preset value (from
-50% to +50%).
Wire burn back (Fig. L-3)
Use to adjust the wire burn-back time when welding stops, optimising the end cutting
process and making it easier to restart welding operations.
For versions 180A and 200A:
- Settings from 0 to 200 (mS).
For version 270A:
- Manual mode: settings from 0 to 200 (mS).
- Synergic mode: correction of the burn-back time compared to preset value (from
-10% to +10%).
Post gas (Fig. L-4)
Use to adjust the protective gas outflow when welding is stopped (Settings 0÷5
seconds). This setting guarantees protection for welding and cooling for the torch.
9.2 Setting of advanced parameters
Press the knobs (Fig. C-1) and (Fig. C-2) for at least 1 second and release to access
the advanced parameter settings menu. Each parameter can be set to the desired
value by rotating/pressing the knob (Fig. C-2) (value displayed in (Fig. L-7)) until you
exit the menu.
10. TIG DC WELDING: PROCESS DESCRIPTION
10.1 GENERAL PRINCIPLES
TIG DC welding is suitable for all types of low-alloy and high carbon steel, and heavy
metals such as copper, nickel, titanium and their alloys. (FIG. M). An electrode with 2%
Cerium (grey band) is normally used for TIG DC welding with electrode at the (-) pole.
The tungsten electrode must be axially sharpened using a grinding wheel, see FIG. N;
make sure the tip is perfectly concentric to prevent arc deviation. The electrode must
be ground along its length. This operation must be repeated periodically according
to the use and wear state of the electrode, or when the electrode itself has been
accidentally contaminated, oxidised or used incorrectly. For the welding to be good,
the exact diameter of the electrode must be used with the exact current, see table
(TAB. 5). The electrode normally projects from the ceramic nozzle by 2-3 mm, but can
reach 8 mm for welding edges.
The weld is created by the edges that melt. Filler metal is not needed when welding
suitably prepared thin material (up to about 1 mm) (FIG. O). A greater thickness
requires rods made from the same material as the basic material and with a suitable
diameter, with edges that have been suitably prepared (FIG. P). For welding to be
successful, the pieces must be carefully cleaned and free from oxide, grease, oil,
solvent, etc.
Содержание GALAXY 300
Страница 142: ... 142 FIG B1 WELDING POLARITY CHART TORCH WORKPIECE MIG MAG GAS TIG MMA 1 2 4 5 3 6 8 7 ...
Страница 144: ... 144 FIG D ...
Страница 145: ... 145 FIG D1 FIG E TAB 5 SUGGESTED VALUES FOR WELDING DATI ORIENTATIVI PER SALDATURA FIG F ...
Страница 146: ... 146 FIG G ...
Страница 147: ... 147 FIG G1 ...