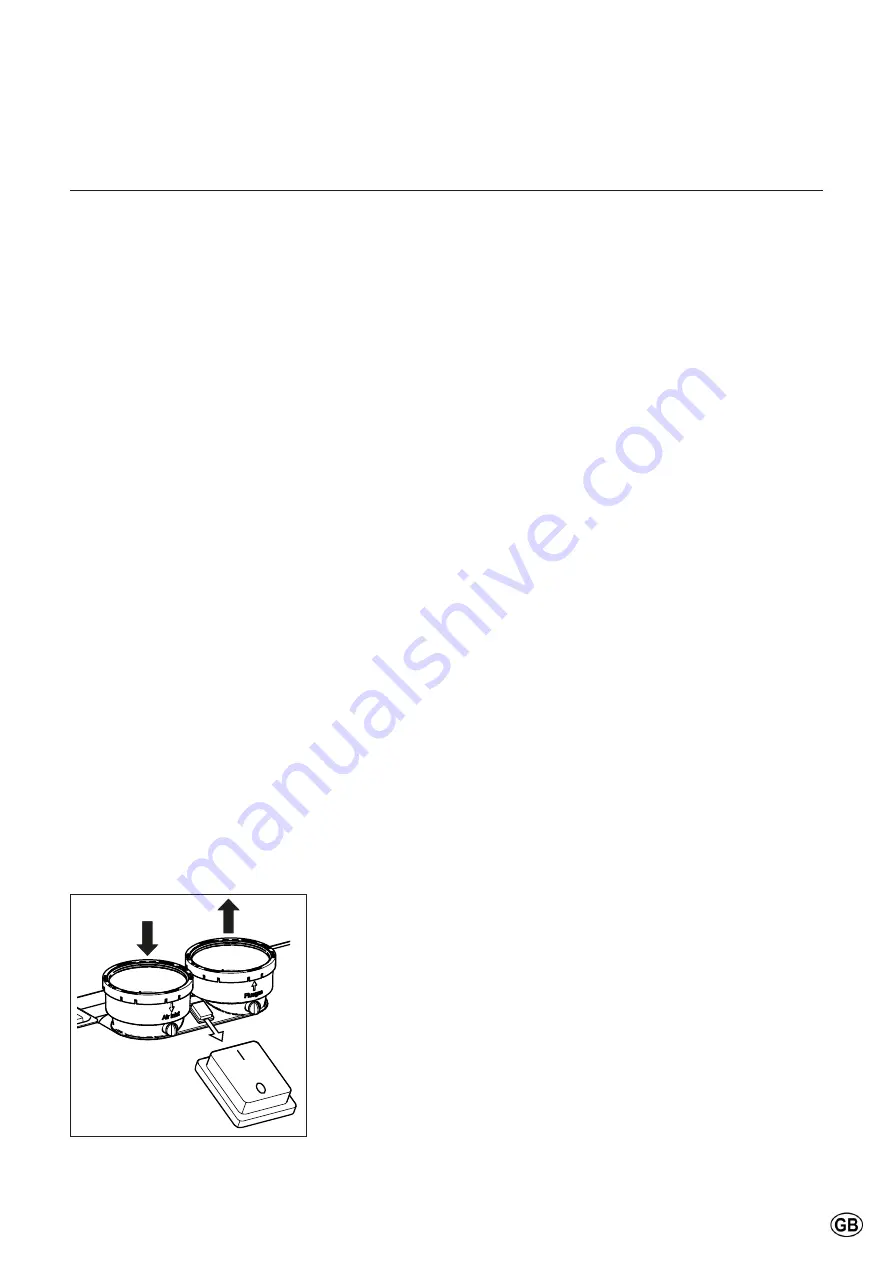
85
Maintenance
Decommissioning and maintenance works
Inspection and maintenance interval
Boiler maintenance is only to be
carried out by qualified staff with
calibrated equipment.
When replacing spare parts only
original ATAG Service parts are to
be used. For this purpose, please
refer to the Service parts list to find
article numbers and exploded views.
Please contact ATAG.
Maintenance intervals
Maintenance has to be carried out at
least after 16,000 operational hours
max. or every 4 years, whatever comes
first.
(To verify with local
service depending by installing
condition).
Depending on the intensive use of
the device, maintenance intervals will
have to be decreased accordingly. For
other situations, maintenance intervals
may also have to be decreased. In
such cases, please contact ATAG for
additional advice.
Inspection and maintenance tasks
have to be carried out in accordance
with the maintenance instructions at
all times. Some tasks are described in
these maintenance instructions. For
complete inspection and maintenance
instructions, see pages 87-93.
When carrying out maintenance
on the boiler, the gas tap has to be
closed and secured against opening.
Maintenance works
- Use the ON/OFF switch (A) to turn
the boiler off;
- Interrupt the power supply to the
boiler, by operating the mains circuit
breaker in the boiler room.
- Interrupt the gas supply to the boiler.
During emptying of the boiler, it is
possible that a part of the heating
water stays behind. Make sure that
any remaining heating water cannot
freeze, in case of a frost hazard.
Decommissioning
It may be necessary to set the boiler
out of service in some situations.
Switch the boiler to
“off”
mode (white
color of power button) pressing the
power button.
This switches off the functions DHW
prog and Pump prog respectively.
ATAG recommends leaving the power
switch switched on to ensure that the
boiler pump(s) and three-way valve
(if fitted) are automatically activated to
prevent them from sticking. The frost
protection remains active. Leave gas
supply open.
If frost, during the period when the
boiler is out of operation, is likely,
then you are advised to remove the
power from the boiler and drain the
boiler(s) and installation. In this
case: close the gas valve.
Maintenance
Please observe the following safety
instructions:
All works on the boiler and
the heating facility (assembly,
maintenance, repairs) may only
be carried out by authorized
technicians, by using suitable
tools and calibrated measuring
instruments. The exchange of
components requires original
ATAG replacement parts.
The main stopcock for gas must be
closed and secured against reopening.
The casing must first be removed,
to be able to carry out maintenance
on the boiler. The panel is secured
by 2 screws on top of the door.
After loosening the screw, the casing
can be removed by pulling and lifting it.
Follow instruction on page 82.
All equipment is preset at the factory.
An O
2
/ CO
2
control measurement must
be carried out during commissioning.
No change should be made on the
zero-point setting. The zero-point
setting must only be checked after
a malfunction, or after an exchange
of the gas valve, the venturi or the
ventilator motor.
The zero-point setting does not
serve for setting up the combustion-
technical characteristic values.
These are made exclusively through
the O
2
/ CO
2
setting.
All gas pipes and screws must be
tested for leakproofness, using
a leak-detecting spray, whenever
maintenance or repair works have
been carried out on the boiler.
In this regard, please observe all of
the individual maintenance steps
documented on page 90 ff., as well
as the overview of inspection and
maintenance procedures provided on
page 92 to 93.
Inspection interval
An inspection must be carried out
at least after every 4,000 boiler
operating hours, however at least
once every year. (To verify with local
service depending by installing
condition).
An inspection consists of a visual
check, of the general condition of the
boiler and the installation.
The objectives of an inspection is an
assessment of the condition of the
equipment, and an evaluation as to
when maintenance works are required.
A visual inspection can lead to a
maintenance procedure.
No tools are required during an
inspection (except for tools for
removing the panel). If necessary, the
corresponding individual maintenance
steps must be carried out, which are
listed as of page 93.
A