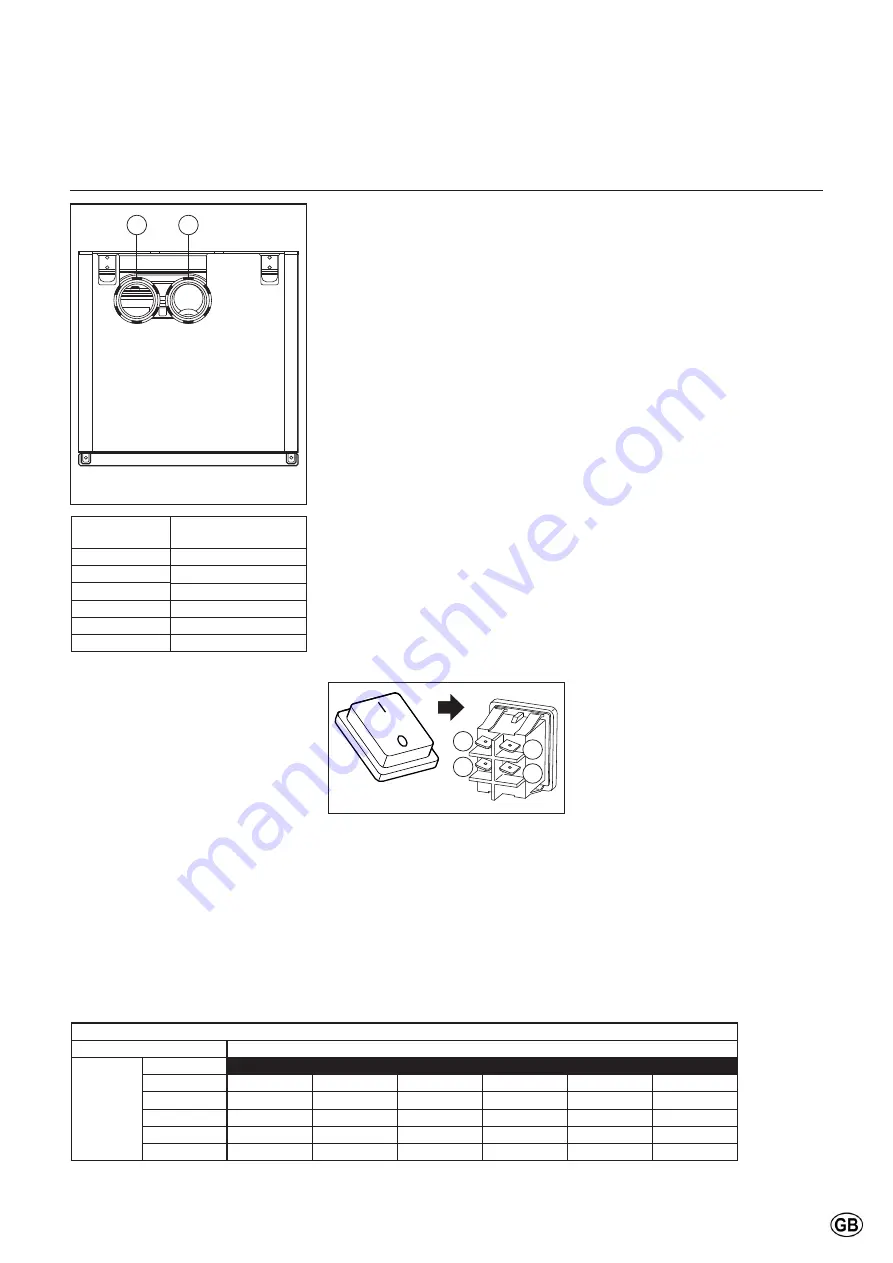
33
Parallel boiler connection
The boiler comes as standard with a
parallel connection for the flue gas
outlet and air supply system.
For the air supply opening (1) diameter
and the flue gas outlet connection (2),
see table below.
The air supply channel can be
connected to it, or, if it is installed as an
“open device” (Drainage category B),
an air filter is recommended.
Concentric boiler connection
The boilers 75-105-125-150 can be
converted into a concentric connection
using the parallel/concentric adapter
100/150 (optional) and carrying out the
following tasks:
- Open and remove the front panel
and the top panel (follow the
instruction on page 42.
- Lift the parallel connection.
- Disconnect the main switch 230V
connection and remove it.
- Replace the parallel connection
with parallel concentric adapter.
- Connect and fit the main switch
230V according to previous
configuration.
The air supply opening has a diameter
of ø150mm.
The flue gas outlet connection has a
diameter of ø100mm.
The flue gas outlet-/air supply system
is then connected to the concentric
connection component.
Installation
Connections
Air- / flue gas ducts for individual boilers
The ATAG XL F-boilers can be used
both in an “open” and in “room sealed”
system.
Open system
The required combustion air is taken
from the immediate environment
(boiler room). For this purpose, please
comply with the applicable boiler room
ventilation regulations.
When using boiler category B23 or
B33 as an ‘open boiler’, the protection
degree of the boiler will be IPX0D
instead of IPX4D.
An air filter or a grid is recommended
on the air intake of the boiler (available
as an accessory on pages 15-17.
Room sealed system
The required combustion air is sucked
in from the outside through a duct.
This improves installation possibilities
within a building. In general, outside air
is cleaner than air from the boiler room.
When the boiler is working, it
produces a white plume of water
vapour. This plume is harmless but
may cause some inconvenience,
particularly in the case of wall
terminal. As a result, roof terminals
are preferred.
In a room sealed installation, roof
terminals should be at the same
height preventing flue gas from
being sucked in by an other boiler
(recirculation). Outlets in recesses
and near erected walls may also
bring about flue gas recirculation.
Recirculation has to be prevented at
all times.
For installation in UK please refer to
installation guidance in BS6644 and
IGE UP10.
Boiler type
Air duct - flue gas
diameter
XL75F
100 - 100
XL105F
100 - 100
XL125F
100 - 100
XL150F
100 - 100
XL180F
130 - 130
XL210F
130 - 130
2
4
1
3
2
1
Fan settings correction
By setting parameter (21-2-4) it is
possible to compensate for a higher
flue gas pressure difference. It is
required to have a pressure drop
calculation of the applied flue gas
system.
According the calculated pressure
drop, the correct value for parameter
(21-2-4) has to be chosen from the
table below.
For setting parameters see the
applicable chapter.
Flue Gas System pressure drop
Parameter (21-2-4)
XL75
XL105
XL125
XL150
XL180
XL210
0 - 600
156
243
143
200
215
265
700
204
295
177
230
280
321
800
224
350
207
275
313
370
900
250
405
240
300
375
-
1000
278
457
260
304
375
-