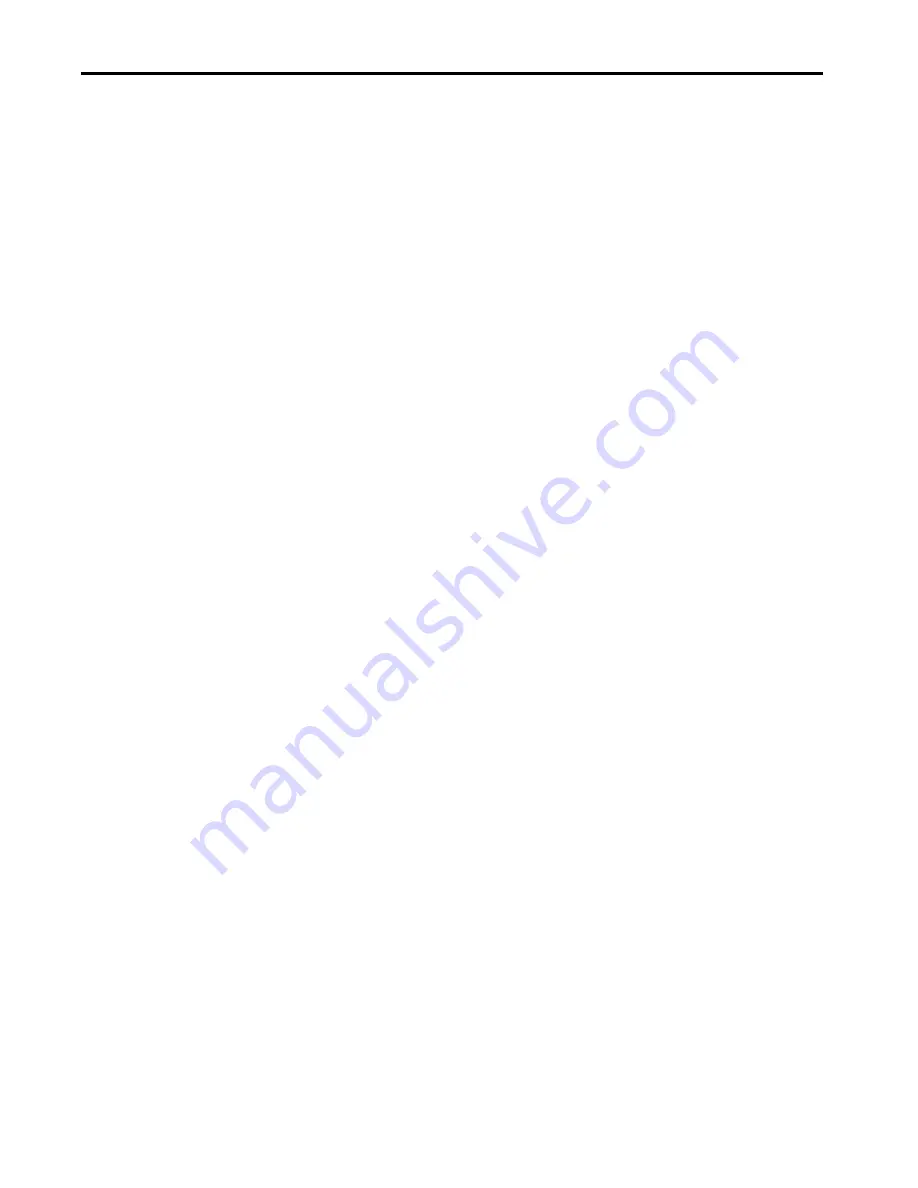
292
Rockwell Automation Publication 1444-UM001D-EN-P - June 2018
Chapter 10
Operate the Module
Calibration
The dynamic measurement module includes no adjustable components so does
not require periodic calibration.
To make sure that the measurement accuracy is within specification, the digital
signal processor (DSP) of the module self-calibrates at each power-up. The
calibration function generates a set of coefficients that are applied to
measurements.
After each calibration, these coefficients are checked against design limits.
Coefficients that exceed their design limits indicate a hardware fault. If the
check fails, a solid red DSP status indicator indicates a calibration failure. Also,
bit 15, “Any calibration failure”, is set in the DSP status value of the input status
assembly.
If calibration fails, the module operates for approximately 1 minute and then
forces the DSP to restart, and recalibrate. This cycle repeats until calibration
passes.
Accuracy
The accuracy of a measurement is dependent on factors that are associated with
hardware, firmware design, and configuration. The sensitivity and accuracy of
the sensor, and the characteristics of the measured signal also affect accuracy.
Signal and Sensor
The sensor, the characteristics of the signal, and the environment have far more
of an impact on measurement accuracy than the instrument. Factors include
signal level relative to the sensors range, signal frequency relative to the
calibration frequency, the environmental conditions relative to the sensor
design conditions, and the advertised accuracy of the sensor to begin with.
Eddy Current Probes
(ECPs) are accurate within a scale factor error, typically ±5 or ±10%, when
measurements are made within a specific range to target, the “Linear Range”.
When using an ECP, make sure that the sensor that is selected is designed such
that the expected / typical range to target is as near the center of the linear
range of the probe as possible.
Содержание 1444-AOFX00-04RB
Страница 10: ...10 Rockwell Automation Publication 1444 UM001D EN P June 2018 Table of Contents Notes...
Страница 12: ...12 Rockwell Automation Publication 1444 UM001D EN P June 2018 Preface Notes...
Страница 198: ...198 Rockwell Automation Publication 1444 UM001D EN P June 2018 Chapter 5 Configure the Tachometer Expansion Module Notes...
Страница 210: ...210 Rockwell Automation Publication 1444 UM001D EN P June 2018 Chapter 7 Configure Relays Notes...
Страница 230: ...230 Rockwell Automation Publication 1444 UM001D EN P June 2018 Chapter 8 Configure Alarms Notes...
Страница 240: ...240 Rockwell Automation Publication 1444 UM001D EN P June 2018 Chapter 9 Trend and Transient Capture Notes...
Страница 316: ...316 Rockwell Automation Publication 1444 UM001D EN P June 2018 Chapter 10 Operate the Module Notes...
Страница 549: ......