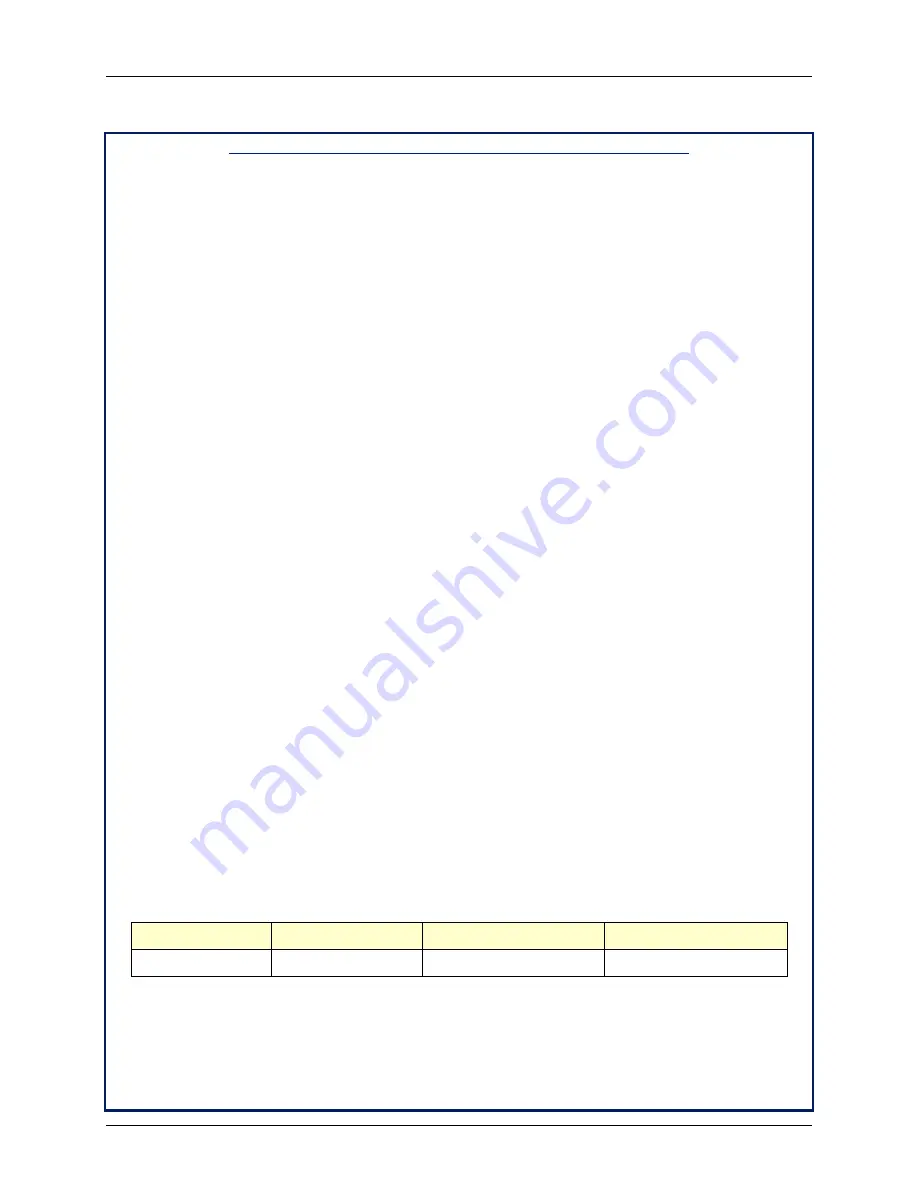
Benchmark 2500 - 3000 Boilers
CHAPTER 4 – INITIAL START-UP
Page
60
of
207
AERCO International, Inc.
•
100 Oritani Dr.
•
Blauvelt, NY 10913
OMM-0094_0F
09/30/2015
Ph.: 800-526-0288
GF-137
4.3.2 Benchmark 3000 Combustion Calibration
BMK 3000 Natural Gas Combustion Calibration
1. Open the water supply and return valves to the unit and ensure that the system pumps
are running.
2. Open the natural gas supply valve to the unit.
3. Set the control panel ON/OFF switch to the
OFF
position
4. Turn on external ac power to the unit. The display will show loss of power and the time
and date.
5. Set the unit to the manual mode by pressing the
AUTO/MAN
key. A flashing
manual
valve position
message will be displayed with the present position in %
.
Also, the
MANUAL
LED will light.
6. Adjust the air/fuel valve position to 0% by pressing the
▼ arrow key.
7. Ensure that the leak detection ball valve downstream of the SSOV is open.
8. Set
the
ON/OFF
switch
to
the
ON
position
.
9. Change the valve position to
30%
using the ▲ arrow key. The unit should begin its start
sequence and fire.
10. Next, verify that the gas pressure downstream of the SSOV is set to
2.3 ± 0.2” W.C. (572
± 50 Pa)
. If gas pressure adjustment is required, remove the brass hex nut on the SSOV
actuator to access the gas pressure adjustment screw (Figure 4-3). Make gas pressure
adjustments using a flat-tip screwdriver to obtain a gas pressure within the range of
2.3 ±
0.2” W.C. (572 ± 50 Pa)
.
11.
Using the ▲ arrow key, increase the valve open position to 100%. Verify that the gas
pressure on the downstream side of the SSOV settles within the range of
2.1 ± 0.2” W.C.
(523 ± 50 Pa)
. Readjust the gas pressure if necessary.
12. With the valve position at 100%, insert the combustion analyzer probe into the flue probe
opening and allow enough time for the combustion analyzer reading to stabilize.
13. Compare the oxygen readings on the combustion analyzer to the on-board O
2
sensor
value displayed in the
Operating
menu of the C-More Control Panel. If the values differ by
more than ±1.5% and your combustion analyzer is correctly calibrated, the on-board O
2
sensor may be defective and need to be replaced.
14. Compare the measured oxygen level to the oxygen range shown below. Also, ensure that
the nitrogen oxide (NOx) and carbon monoxide (CO) readings do not exceed the values
shown. If you are not in a “NOx-limited” area and/or do not have a NOx measurement in
your analyzer, set the oxygen (O
2
) at 5.1% ± 0.5%.
Table 4-5:
Combustion Calibration Readings – 100% valve Position
Valve Position
Oxygen (O
2
) %
Nitrogen Oxide (NOx)
Carbon Monoxide (CO)
100%
4.5% - 5.6%
≤
20 ppm
<100 ppm
15. If the oxygen level is not within the required tolerance, the gas pressure on the
downstream side of the SSOV must be adjusted using the gas pressure adjustment
screw on the SSOV (Figure 4-4). Slowly rotate the gas pressure adjustment
(approximately 1/4-turn increments). Allow the combustion analyzer to stabilize following
each adjustment. Clockwise rotation reduces the oxygen level, while counterclockwise
rotation increases the oxygen level.