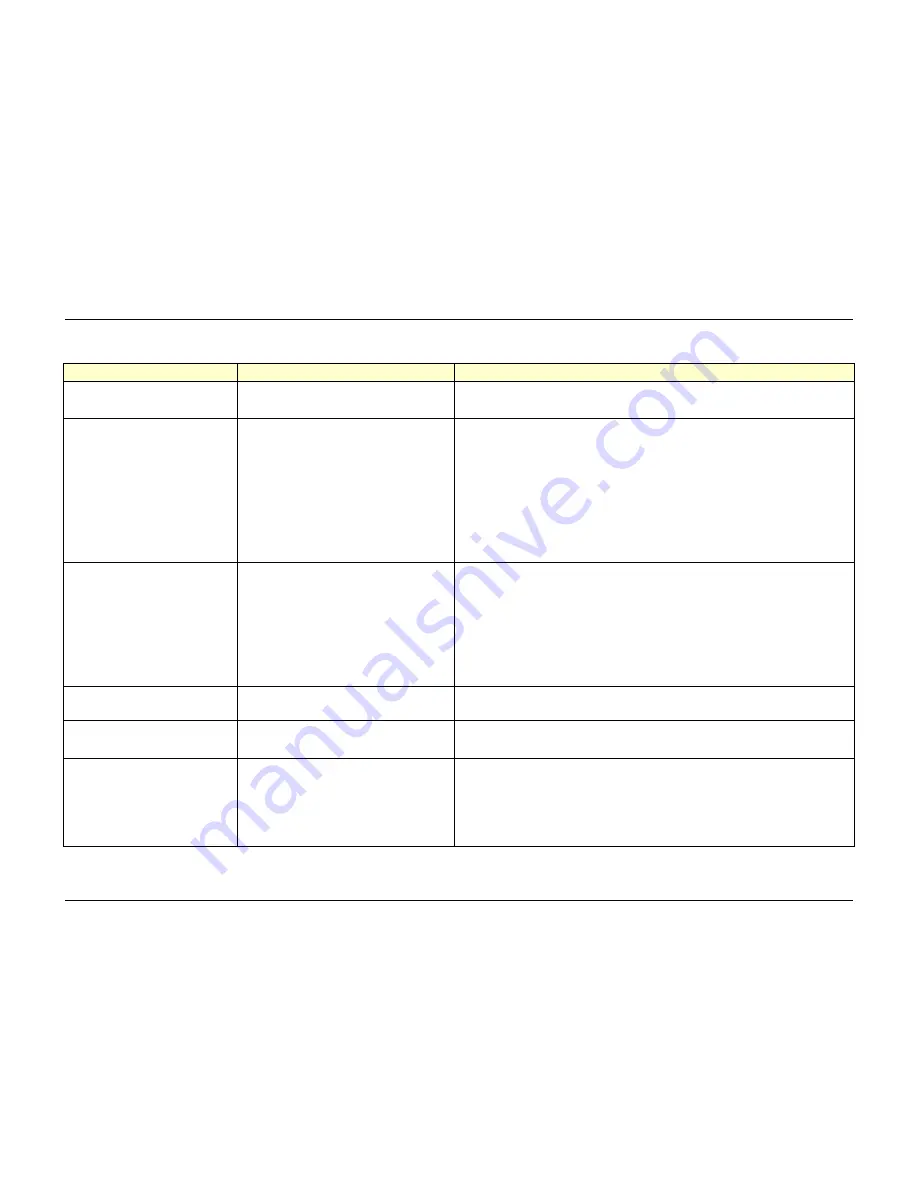
Benchmark 2500 - 3000 Boilers
CHAPTER 8 – TROUBLESHOOTING GUIDE
OMM-0094_0F
AERCO International, Inc.
•
100 Oritani Dr.
•
Blauvelt, NY 10913
Page
115
of
207
GF-137
Ph.: 800-526-0288
09/30/2015
TABLE 8-1: BOILER TROUBLESHOOTING – Continued
FAULT INDICATION
PROBABLE CAUSES
CORRECTIVE ACTION
RECIRC PUMP FAILURE
1.
Internal recirculation pump failed.
1. Replace recirculation pump.
REMOTE SETPT
SIGNAL FAULT
1.
Remote setpoint signal not present:
Not yet installed.
Wrong polarity.
Signal defective at source.
Broken or loose wiring.
2.
Signal is not isolated (floating) if 4
to 20 mA.
3.
Control Box signal type selection
switches not set for correct signal
type (voltage or current).
1.
Check I/O Box to ensure signal is hooked up.
Hook up if not installed.
If installed, check polarity.
Measure signal level.
Check continuity of wiring between source and unit.
2.
Check signal at source to ensure it is isolated.
3.
Check DIP switch on PMC board to ensure it is set correctly for the
type of signal being sent. Check control signal type set in
Configuration
menu.
RESIDUAL
FLAME
1.
Defective Flame Detector.
2.
SSOV not fully closed.
1.
Replace Flame Detector.
2.
Check open/close indicator window of Safety Shut-Off Valve (SSOV)
and ensure that the SSOV is fully closed. If not fully closed, replace
the valve and or actuator.
Close the 2” Gas Shut-Off Valve downstream of SSOV (Figure 2-7).
Install a manometer or gauge at the leak detection port between the
SSOV and Gas Shut Off Valve. If a gas pressure reading is observed
replace the SSOV Valve and/or Actuator.
SSOV FAULT DURING
PURGE
See SSOV SWITCH OPEN
SSOV FAULT
DURING RUN
SSOV switch closed for 15 seconds
during run.
1.
Replace or adjust micro-switch in SSOV actuator. If fault persists,
replace actuator.
SSOV RELAY
FAILURE
1.
SSOV relay failed on IGST board.
2.
Floating Neutral.
3.
Hot and Neutral reversed at SSOV.
1.
Press
CLEAR
button and restart unit. If fault persists, replace
Ignition/Stepper (IGST) Board.
2.
The Neutral and Earth Ground are not connected at the source and
therefore there is a voltage measured between the two. Normally this
measurement should be near zero or no more than a few millivolts.
3.
Check SSOV power wiring.