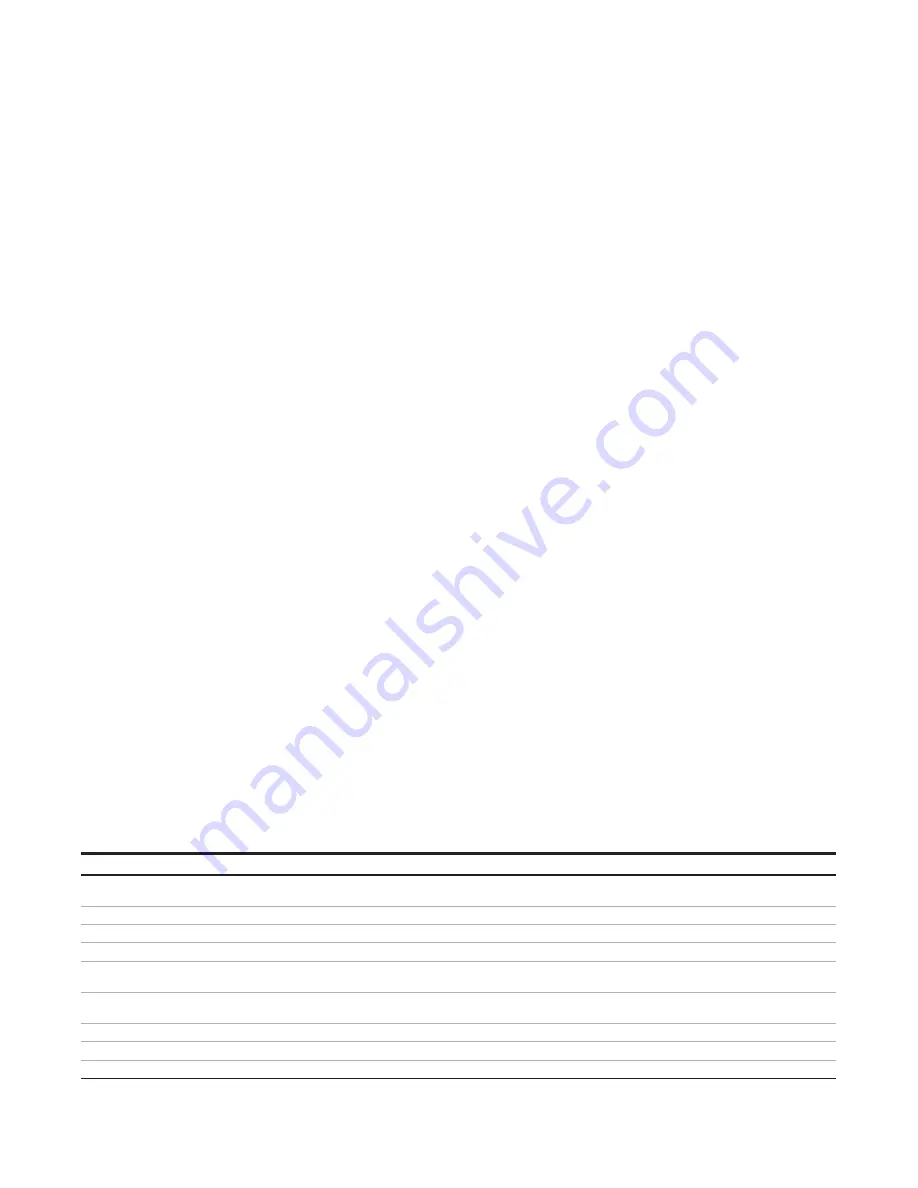
—
4 Configuring the Motor Protection Functions
General Information
The UMC provides comprehensive motor protection including phase failure detection, adjustable motor protection for stalled
motors during startup or normal operation, configurable current limits to generate trips or warnings and many more.
The different protection and monitoring functions generate warning signals, trip signals and measured or calculated process
values. All these data are available to the user to either display them on the LCD panel, transfer them to the control system or pro-
cess them in a custom specific application.
The UMC100.3 can be used with or without an additional voltage module or analog input module. The protection functions availa-
ble without a voltage module are described in section "Thermal and Current Motor Protection Functions". The protection functions
that require a voltage module are described in section "Voltage and Power Protection Functions". The voltage Dip function which
can be used with or without a voltage module is described in section "Voltage Dips, Load Shedding". The supervision functions
available with the analog input module are described in section "Temperature Supervision".
Automatic Reset of Protection Faults
The setting of the "
Fault autoreset
" parameter determines how the UMC manages protection trips.
• Off
(the default setting)
A protection trip must be acknowledged from the user. This can be done via LCD panel, fieldbus or the multifunction inputs
DI0-DI2 if configured.
• On
A protection trip is automatically acknowledged without intervention of a human operator if the trip condition has gone.
EOL and Current based Protection Functions
In this section you find information on how to configure the different motor current based protection functions of the UMC.
The following topics are covered:
Function and parameters of the electronic overload protection, the thermal memory and points to consider
if the motor is started cyclically (e.g. S3 motor operation mode)
• Long start, locked rotor protection during motor start
• Overcurrent and undercurrent protection during normal operation
• Imbalance protection
• Phase loss protection
• Phase sequence
• Thermistor motor protection
• Earth fault protection with auxiliary device CEM11-FBP or internally calculated
The following process values are available:
Process Value
Explanation
Data range
Motor Current
The average current of the three phases and
single phase currents
0…800 % of I
e
Motor Current
The average current of the three phases
In user selected unit (A, mA ...)
Earth Fault Current
Calculated earth fault current
in % of I
e
Thermal Load
Thermal load of the motor
0...100%. 100% is the trip level.
Current Imbalance
Imbalance of the motor current in the three
phases
0...100%
Time to Trip
Time until the EOL trips the motor
0 ... 6553 s
(6553 s means an infinite trip time)
Time to Cool
Time until the motor can be restarted
0 ... 6553 s
PTC Resistance
Value measured from the PTC input in ohms.
0 ... 4800
Line Frequency
Mains frequency
45 ... 65 Hz
36
U MC10 0. 3 U N IVE R SA L MOTOR CONTROLLE R
T EC H N I C A L D E S C R I P T I O N
Содержание UMC100.3
Страница 1: ... MANUAL Univeral Motor Controller UMC100 3 ...
Страница 159: ...159 ...