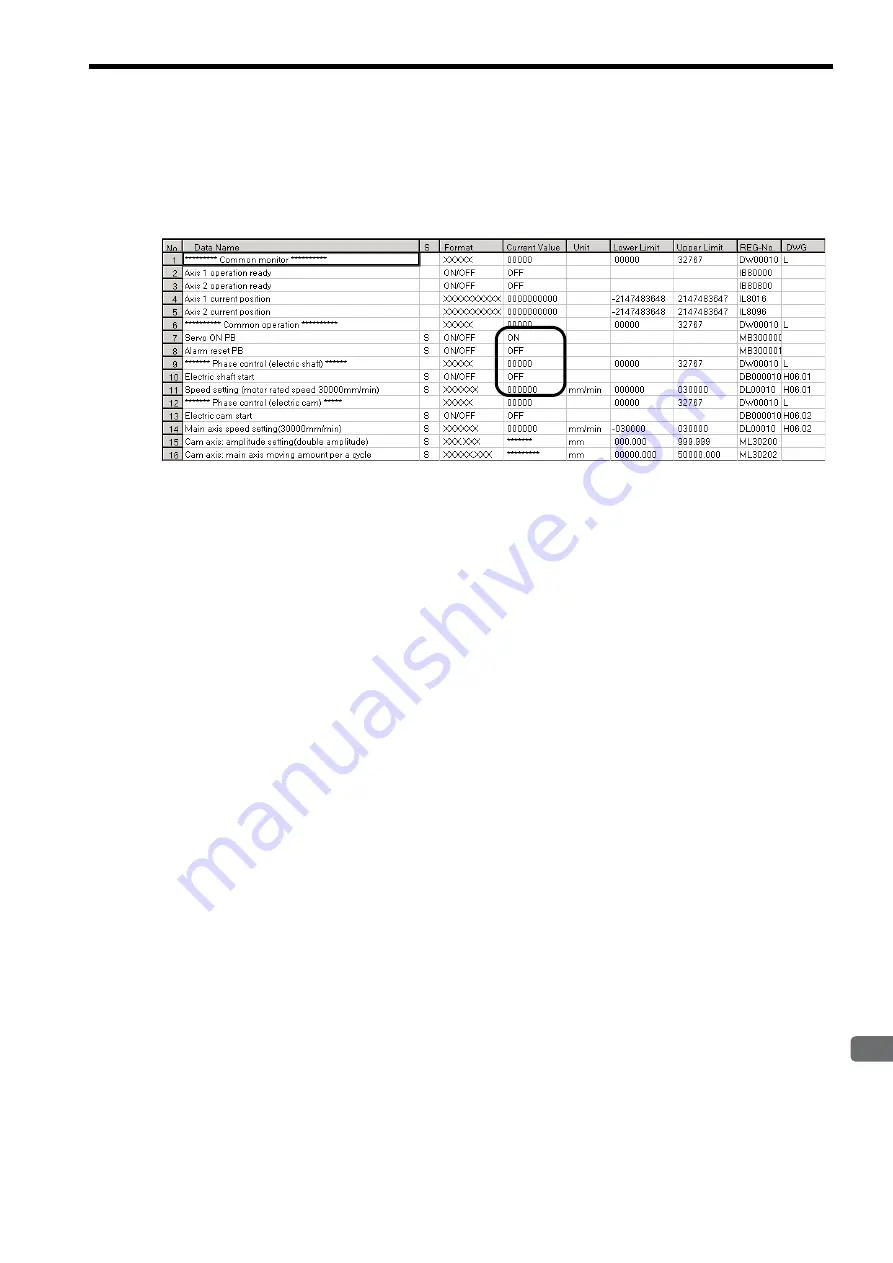
4.4 Checking Sample Program Operation
4-59
4
System Startup and Sample Programs
( 3 ) H06 Drawing Tuning Panel
Display the H06 Drawing Tuning Panel as shown in
4.4.1 How to Open the Tuning Panel Window
on page 4-44.
Model system operation can be controlled by writing the current values for
Common operation
and
Phase control
(electric shaft)
from the Tuning Panel.
( 4 ) Procedure
Use the following procedure to operate the Tuning Panel and check operation.
1.
Servo ON
Change the
Servo ON PB
current value from
OFF
to
ON
.
The Servomotor will turn ON and the Servo will be clamped.
2.
Electronic Shaft Start
Change the
Electric shaft start
current value from
OFF
to
ON
.
The mode will change to the phase control (electronic shaft) mode. Enter
OFF
to exit position control (electric
shaft) mode.
3.
Enter Speed Settings
Enter any value within the setting range (0 to 30000) as the current value of
Speed setting (motor rated speed
30,000 mm/min)
.
This operation synchronizes the speed for both axes to the speed of the virtual master axis and operation starts.
Change the
Electric shaft start
current value from
ON
to
OFF
when the check operation has been completed.
It is necessary to create routines within the actual application program in order to monitor and control the registers
corresponding to the signals and data listed in the table above.
The register numbers that correspond to the signals used in this sample program will be the register numbers
displayed under
REG-No
. next to
DWG
at the right of the Tuning Panel window.