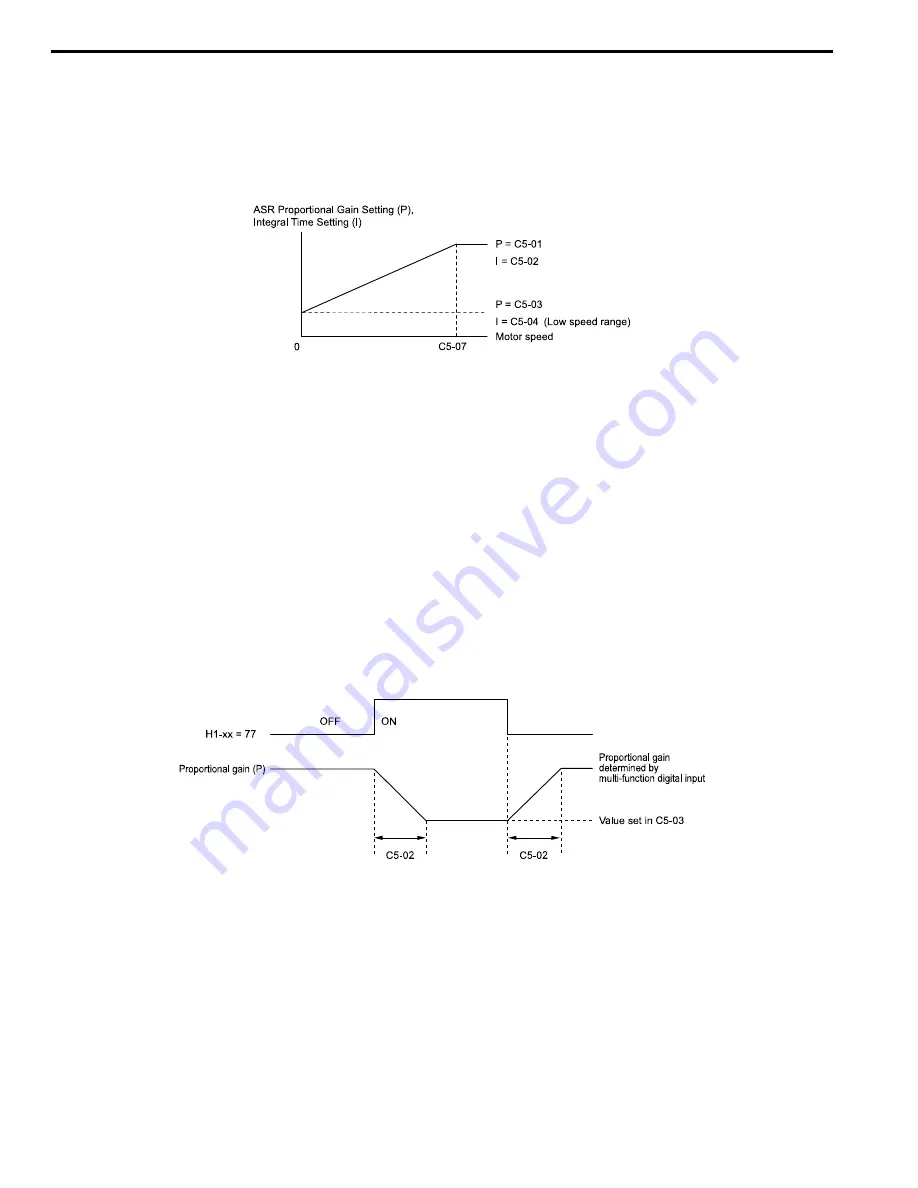
262
YASKAWA
TOEPYAIGA8002B GA800 Drive Programming
2. Run the motor at zero speed or low speed and decrease
C5-02 [ASR Integral Time 1]
until immediately before
vibration starts to occur.
3. Check for oscillation when you run the motor at maximum speed.
4. If oscillation occurs, increase
C5-02
and decrease
C5-01
.
When there is no oscillation, the adjustment procedure is complete.
5. Set the low-speed gain. Run the motor at zero speed or low speed and increase
C5-03 [ASR Proportional Gain 2]
until immediately before vibration starts to occur.
Figure 2.56 Low-speed/High-speed Gain Settings
6. Set the low-speed integral time. Run the motor at zero speed or low speed and decrease
C5-04 [ASR Integral Time
2]
until immediately before vibration starts to occur.
7. Set
C5-07 [ASR Gain Switchover Frequency]
.
8. Check for oscillation when you run the motor at speeds more than the setting in
C5-07
.
Note:
•
If overshooting occurs when acceleration ends, decrease the value set in
C5-01
and increase the value set in
C5-02
.
•
If there is undershoot at stop, decrease
C5-03
and increase
C5-04
.
■
Use MFDI Switch for Proportional Gain
Note:
If
A1-02 = 1 [Control Method Selection = V/f Control with Encoder]
, you cannot use this function.
You can use the input terminals set for ASR Gain (C5-03) Select
[H1-xx = 77]
to switch the proportional gains set
with
C5-01
and
C5-03
. When the configured input terminal is deactivated, the proportional gain set for
C5-01
is
selected. When the terminal is activated, the proportional gain set for
C5-03
is selected. The proportional gain
changes linearly over the time set in
C5-02 [ASR Integral Time 1].
The signals from this MFDI are more important
than
C5-07 [ASR Gain Switchover Frequency]
.
Figure 2.57 Proportional Gain through Multi-function Digital Input Switch
■
Speed Waveform Monitoring Method
To make small adjustments of ASR parameters, monitor the speed waveforms when you make the adjustments.
shows example settings of parameters to monitor speed waveforms.