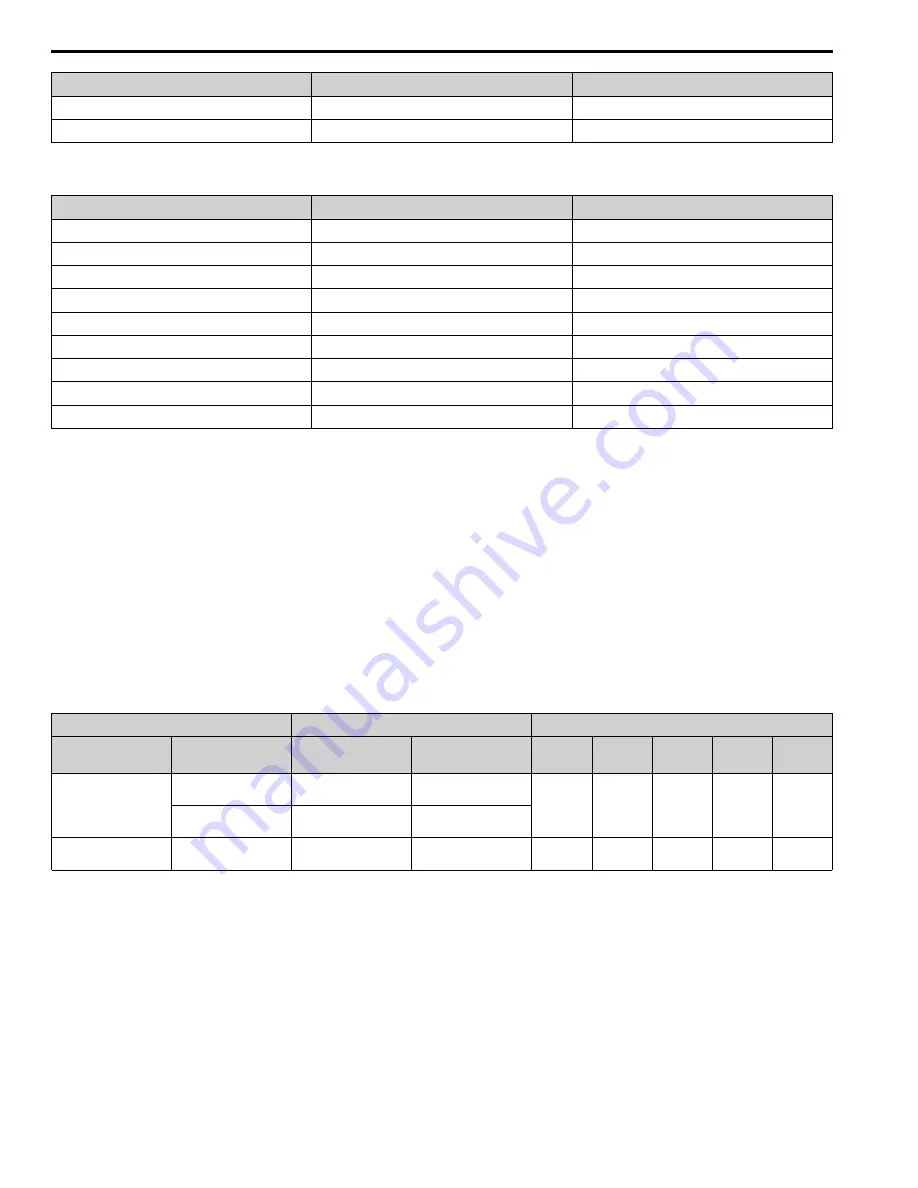
2.2 A: Initialization Parameters
184
YASKAWA
TOEPYAIGA8002B GA800 Drive Programming
No.
Name
Optimal Value
L2-01
Power Loss Ride Through Select
1: Enabled
L3-04
Stall Prevention during Decel
1: Enabled
The drive saves the parameters in
as user parameters.
Table 2.13 Parameters Saved as User Parameters with the Air Compressor Preset
User Parameter No.
Parameter No. Saved
Name
A2-01
b1-01
Frequency Reference Selection 1
A2-02
b1-02
Run Command Selection 1
A2-03
b1-04
Reverse Operation Selection
A2-04
C1-01
Acceleration Time 1
A2-05
C1-02
Deceleration Time 1
A2-06
E1-03
V/f Pattern Selection
A2-07
E1-07
Mid Point A Frequency
A2-08
E1-08
Mid Point A Voltage
A2-09
E2-01
Motor Rated Current (FLA)
■
Notes for Elevator Applications
When using the drive for elevator applications, read the safety descriptions and precautions, and safely and correctly
use the device.
Conditions to Open and Close the Brake
Set
L4-07 = 0 [Speed Agree Detection Selection = No Detection during Baseblock]
to open and close the holding
brake.
When
L4-07 = 1 [Detection Always Enabled]
, the output frequency increases when you input the Run command
although the external baseblock command is input. Because of this, speed detection operates and will open the brake
signal.
•
Set Related Parameters
shows examples of parameter settings to use the MFDO terminal (M1-M2) as the holding brake open
and close signal.
Table 2.14 Holding Brake Open and Close Signal Setting Example
Brake Open and Close Signal
Brake Open and Close Level Adjust
Applicable Control Methods (A1-02 Setting Value)
Signal Name
Parameter Settings
Signal Name
Parameter Settings
V/f
(0)
OLV
(2)
CLV
(3)
AOLV
(4)
CLV/PM
Frequency (FOUT)
Detection 2
L4-07 = 0
Speed Agree Detection
Level
L4-01 = 1.0 Hz to 3.0 Hz
x
x
-
x
-
H2-01 = 5
Speed Agree Detection
Width
L4-02 = 0.0 Hz to 0.5 Hz
During Frequency Output
H2-01 = 37
DC Injection/Zero Speed
Threshold
b2-01 = 0.1 Hz to 0.5 Hz
-
-
x
-
x
*1
When
A1-02 = 7 [PM Closed Loop Vector]
, make sure that the motor can rotate before you do Auto-Tuning or switch the encoder. Refer
to Closed Loop Vector Control for induction motors for information about the signal to use and the adjustment method.
*2
When
A1-02 = 2 [Open Loop Vector]
, it is the usual setting range. When
A1-02 = 0 [V/f Control]
, set
L4-01
to the rated slip frequency of
the motor + approximately 0.5 Hz. If you set the value too low, motor torque will not be sufficient and it will cause motor rollback. Set
the parameters to meet these conditions at the same time. If the setting is too high, overshoot is possible at start.
•
L4-01
>
E1-09 [Minimum Output Frequency]
•
L4-01
>
L4-02 [Speed Agree Detection Width]
*3
Use
L4-02
to adjust the detection width of Frequency Detection 2. If rollback occurs when the motor is stopped, set the frequency to
approximately 0.1 Hz.