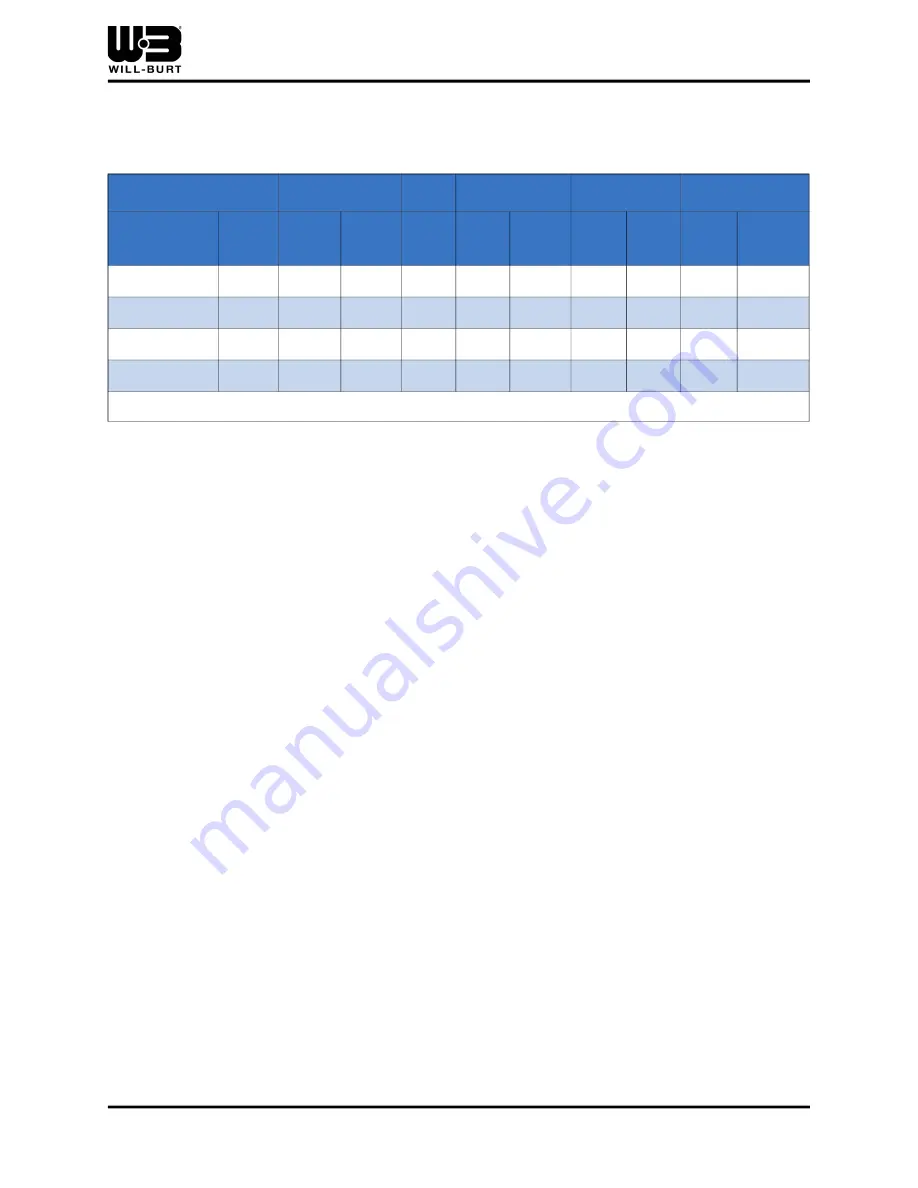
PAGE 65 OF 164
PNEUMATIC MAST WITH REMOTE LOCKING SYSTEM
OPERATING INSTRUCTIONS
TP-5580101-A
FEBRUARY 2022
4.5.6
Internal Mounting Kit Installation Specifications
Table 4-12 Internal Mounting Kit (Roof Flange and Roof Ring) Installation Specifications
Ø A
C
D
Ø
BCD
P/N*
Base
Tube
inch
mm
B
inch
mm
inch mm
inch
mm
905734
6 ¾
9 ¾
248
8
1.9
48.3
0.25
6.4
8 ¾
222
905733
9
12
305
8
1.9
48.3
0.25
6.4
11
279
910784
11 ¼ 14.25
362
8
1.8
45.7
0.25
6.4
13
330
5476101
13.5
16.5
419
8
1.75
44.5
0.25
6.4
15 ¼
387
* Part Numbers for clear anodized finish. Additional finishes are available.
Summary of Contents for 10-60 HDL
Page 2: ......