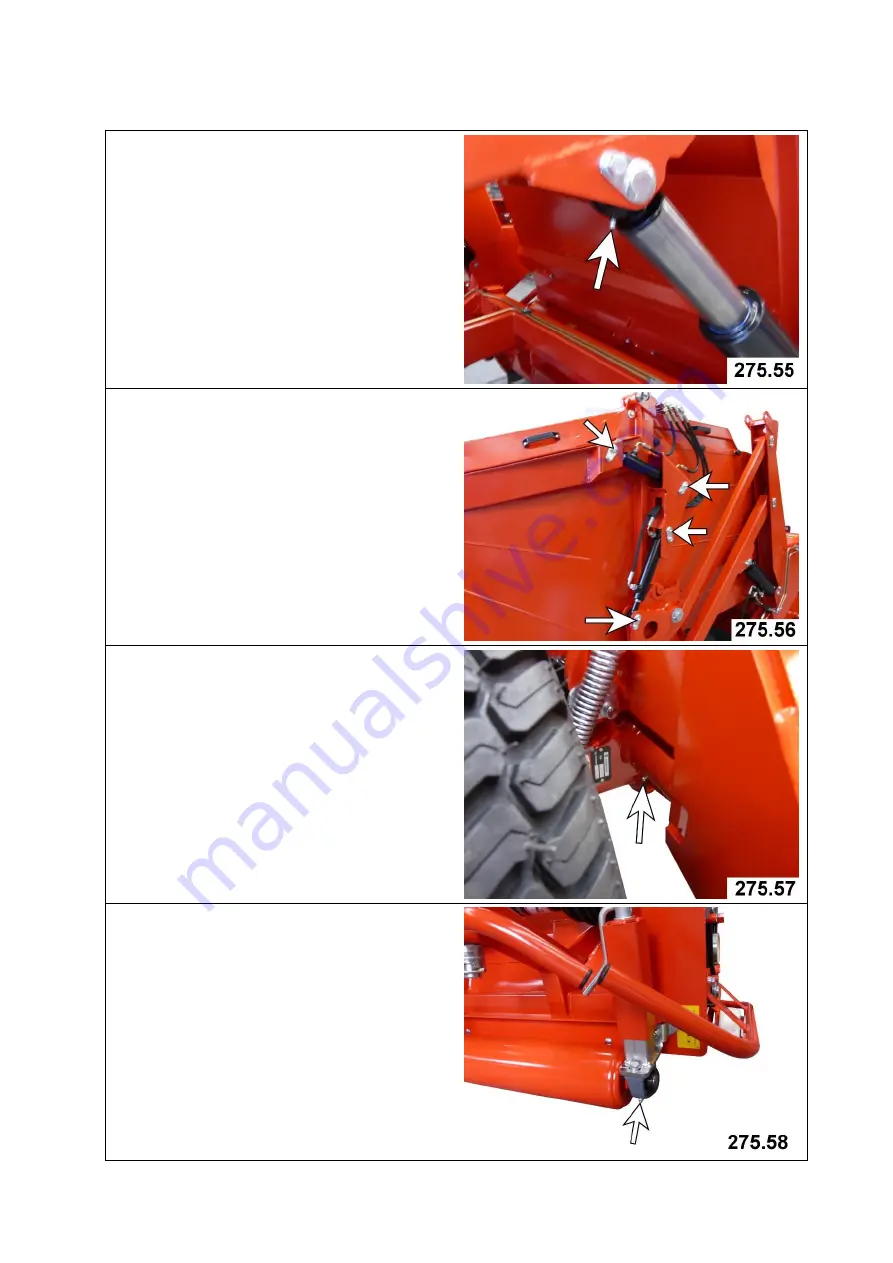
All information, illustrations and specifications in this manual are based on the latest information
available at the time of publication. We reserve the right to make changes at any time without notice.
52
8.0. Service
8.4. Lubricating points
8.4.5. Discharging the hopper
Bearing pins of hydraulic
cylinders on right and left
8.4.6. Discharging the hopper
Joint of telescopic cylinder
8.4.7. Pivot axle
Bearing bush
8.4.8
.
Front roller
pedestal bearing unit left