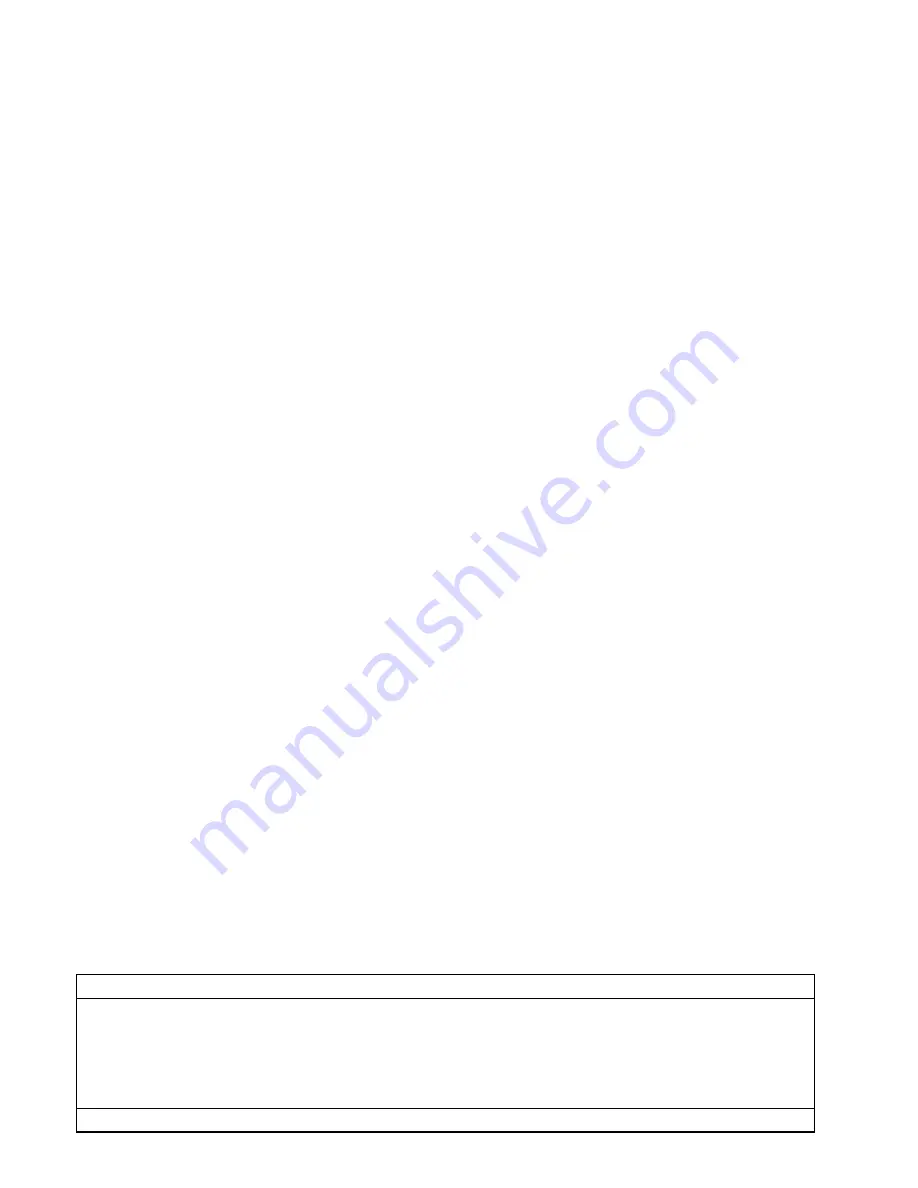
05TA Service Manual
MAINTENANCE
7/19/13
7-4
It is advisable to double-check the system to make sure that fouling is actually causing the trouble.
High head pressure alone does not mean a fouled condenser.
The following possibilities should always be checked before cleaning is undertaken:
1.
Non-condensables in system or faulty head pressure gauge? Check standby pressures
against refrigerant tables.
2.
Incorrectly set or defective water regulator valve? Check its setting and operation.
3.
Partly closed compressor discharge service valve? Check its setting. Stem should be
backseated.
4.
High water temperatures entering condenser? Check tower fan and system.
After the above possibilities have been eliminated, determine the temperature difference between the
water leaving the condenser and the refrigerant condensing temperature (saturation temperature,
from pressure-temperature chart, corresponding to head pressure). If this difference is more than
10
°
F, cleaning is indicated because this difference indicates a good heat exchange is not being made.
If this difference is less than 8
°
F, something other than a fouled condenser may be causing the high
head pressure. In normal operation, this difference will stay between 5
°
F and 10
°
F regardless of
water inlet temperature when the water flow is regulated by a pressure operated water valve. If this
difference is less than 5
°
F, restricted water flow or a low supply pressure is indicated. A restriction
can occur with foreign matter in the condenser, but it is also likely to be somewhere else in the
system.
Draining Condenser.
Draining of water cooled condensers is recommended in preparation for the
winter cold where units may be left exposed to ambient temperatures below 32
°
F. Theoretically, it is
easy to drain a condenser. In practice, the problem can be complex.
Despite the fact that a condenser my have vent and drain fittings, the opening of these fittings is not
sufficient for a natural gravity flow. Water will be retained in a tube due to (1) surface tension and
(2) the normal curvature between tube supports. Our experience shows that as much as 20% of the
water in the condenser can be retained. To break the surface tension on the tubes and to drain all
tubes completely, it is necessary to remove the back plate and actually tilt the condenser a minimum
of 5 degrees. Whether water left in the tubes will cause damage during a freeze-up will be dependent
upon how quickly the freeze occurs and the location of the water inside the condenser.
In the field it is recommended that the tubes be blown out individually with air. Alternatively, a
minimum of 25% ethylene glycol in the system will also prevent a freeze, which can rupture the
tubes.
Water Cooled Condenser Cleaning.
! CAUTION !
The following directions and precautions should be observed
when cleaning is undertaken. The warranty on condensers is void if
they are damaged by improper cleaning tools or methods. If
harsh chemicals are used, be sure to follow the manufacturer’s
recommendations regarding safety in handling those solutions.
! CAUTION !
Summary of Contents for P118F/HE100
Page 4: ...Vogt Tube Ice Machines Installation Service Manual and Parts Catalog 12A4171M06 05TA Model ...
Page 10: ...05TA Service Manual TABLE OF CONTENTS vi ...
Page 20: ...05TA Service Manual INTRODUCTION 7 19 13 1 10 ...
Page 40: ...05TA Service Manual INSTALLING YOUR TUBE ICE MACHINE 3 7 14 3 18 BLANK PAGE ...
Page 50: ...5 6 5TA Service Manual START UP AND OPERATION 7 19 13 Blank page ...
Page 106: ...05TA Service Manual SERVICE OPERATIONS 3 10 14 9 28 Blank ...
Page 114: ...Blank page ...
Page 115: ...05TA Service Manual TABLES CHARTS 3 10 14 11 1 11 Tables Charts ...