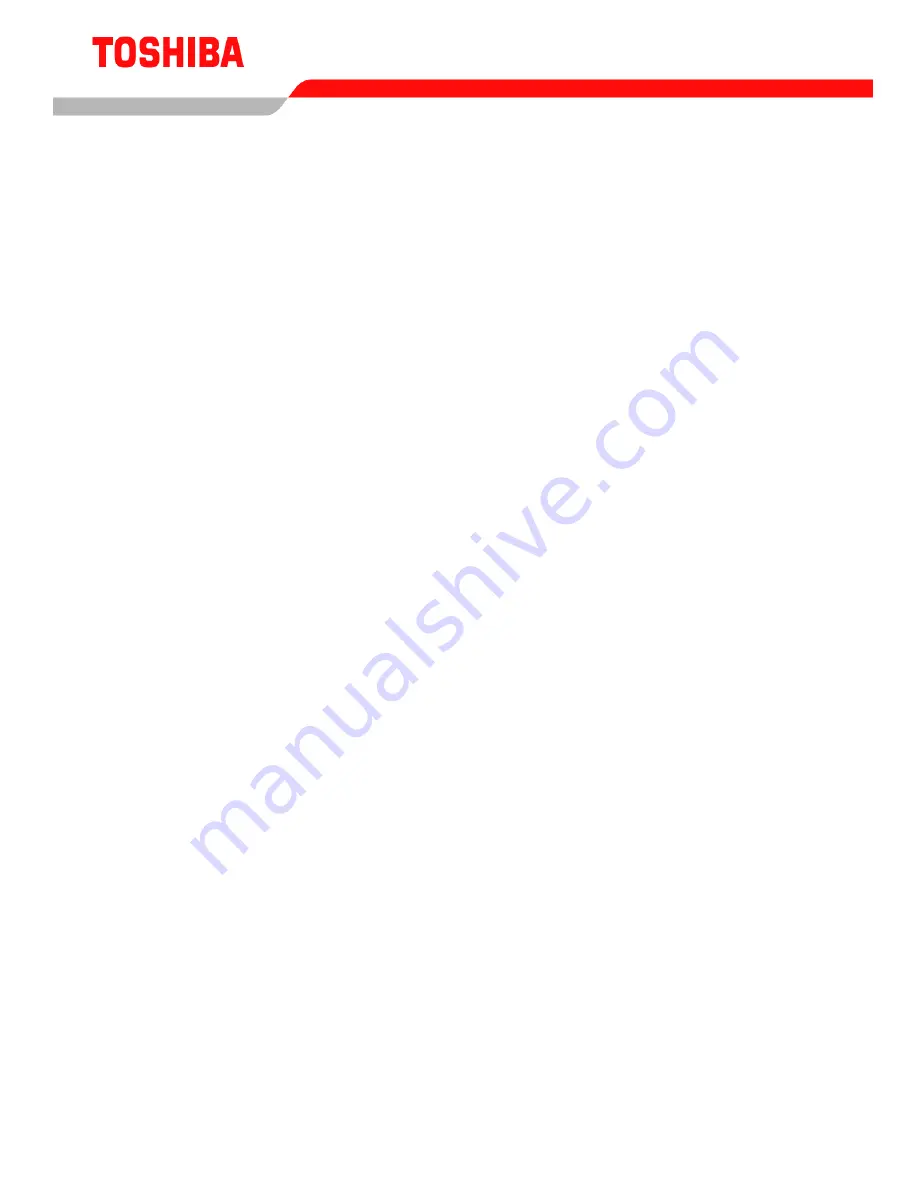
*
For additional assistance, please contact Toshiba Adjustable Speed Drive Marketing Dept. at (800) 872-
2192
82
If the S-20 interface will be used to start and stop the drive, change
Frequency Mode Selection
to ‘3' to
enable the communication option board as a valid input. For the same reason, change the
Command Mode
Selection
to ‘3'.
Enter the unblinded
Communication Parameters Group
:
%
Change
Communication Selection
to ‘3' to prepare for TOSLINE-S20 communication
%
Set the
TOSLINE-S20 Receiving Address
and
TOSLINE-S20 Sending Address
to the start address
specified previously in the S-LS system. Set-up is from the perspective of the G3 drive. The receiving
address is the start address that the T2 talks to, and the sending address is the start address which the
G3 talks to, (ie using the previous example table, 40 and 0 respectively).
%
Now set the
S-20 Command Input.
Setting this value to ‘3' allows starting and stopping as well as
setting a speed base value [bit 0: Command, bit 1: Speed Base Value, bit 2: Auxiliary Speed Base
Value, bit 3: External Current Limit Value, bit 4: Drooping on-line gain value]. Note that ‘3' in
decimal is equal to ‘0011' in binary.
%
The
S20 Monitor Output
parameter will choose which drive data are available through the S20 network
[bit 0: Status, bit 1: Speed Feedback Value, bit 2: Output Current Value, bit 3: Excitation Current
Value, bit 4: Torque Current Value]. A setting of ‘31' which is equal to ‘binary 1111', will allow all
selectable values to be monitored.
%
Set the
TOSLINE-S20 Frequency Reference Address Selection
to ‘1'
%
Specify the address to store the frequency in the
TOSLINE-S20 Frequency Reference Address.
To
continue the previous example, the frequency command was sent by the T2 PLC to address ‘42' which
falls within the previously specified range.
%
Finally, both the
TOSLINE-S20 Communication Error Mode
and
Communication Option Reset
can be
set to ‘0'. [For the former, this means that in the case of an error, a zero command/speed is commenced
instead of holding the data of the status prior to the error. For the later, nothing is done to the
communication board after an error where as a value of ‘1' would have reset the board after an error
(after reset this parameter would be set back to ‘0').]